Exploring Plasma Atomic Layer Deposition Techniques
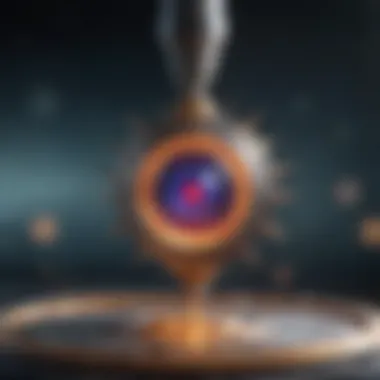
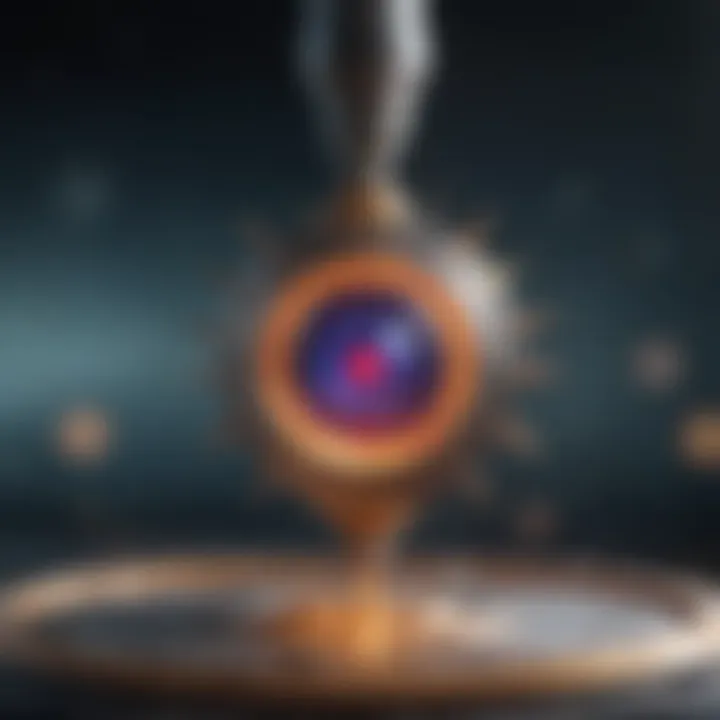
Intro
Plasma atomic layer deposition (ALD) stands as a crucial technique in the field of materials science. It allows for the fabrication of thin films with unparalleled precision and uniformity. This method employs plasma to drive surface reactions, distinguishing it from traditional chemical vapor deposition practices. As industries evolve, the need for advanced materials and coatings has surged. Plasma ALD meets this demand by offering tailored properties for various applications, from electronics to nanotechnology.
In this article, we will examine the principles of plasma ALD and explore its significance in current technological advancements. This overview will provide readers with insight into how plasma ALD operates and its place in modern industries, potentially inspiring further research.
Research Overview
Summary of Key Findings
Plasma ALD utilizes plasma to enhance atomic layer deposition by improving the reactivity of precursor materials. This process results in high-quality films with excellent conformity on complex three-dimensional structures. Key findings from current research indicate that:
- Plasma ALD is effective for depositing a wide variety of materials, including oxides, nitrides, and metals.
- The method improves film uniformity, reducing defects commonly seen in traditional deposition processes.
- Different plasma conditions can influence film properties, allowing for customizable outcomes based on specific needs.
These points underline the advantages of plasma ALD compared to conventional techniques, highlighting its essential role in various applications.
Relevance to Current Scientific Discussions
The exploration of plasma ALD is timely, considering the increasing demand for nanoscale materials and the miniaturization of devices. Recent discussions in the scientific community emphasize the importance of:
- Innovative applications in microelectronics, optics, and energy storage technologies.
- The challenges faced in scaling up plasma ALD processes for industrial use.
- Future research directions aimed at improving efficiency and expanding material options in plasma ALD.
This relevance points toward an exciting era of advancement in materials technology, driven largely by the capabilities of plasma ALD.
Methodology
Research Design and Approach
The examination into plasma ALD involves both theoretical and practical perspectives. Research typically includes experimental studies aimed at:
- Characterizing the plasma generation and its parameters.
- Evaluating how different chemistry influences film properties.
Data Collection and Analysis Techniques
Data collection in plasma ALD is critical for understanding the deposition mechanisms. Common techniques employed are:
- Spectroscopic methods for analyzing film composition.
- Surface analysis tools to assess film thickness and uniformity.
- Advanced microscopy for observing microstructure.
By deploying these methodologies, researchers can gather crucial data that informs the development of plasma ALD as a viable deposition technique.
Prologue to Plasma Atomic Layer Deposition
Plasma atomic layer deposition (ALD) represents a significant advancement in thin film deposition technology. It is important to recognize the unique aspects that plasma ALD brings to various industries, particularly in achieving high precision in film thickness and uniformity. With the increasing complexity of devices in sectors like electronics and energy, the demand for more sophisticated deposition techniques is evident. Plasma ALD meets this demand through its ability to deposit thin films with atomic-level control, providing a robust solution for modern manufacturing needs.
Definition and Overview
Plasma atomic layer deposition is a process used to create thin films on substrates through alternating exposure to precursors and plasma treatments. During the deposition cycle, a substrate is exposed to a chemical precursor, followed by plasma exposure, which promotes surface reactions at lower temperatures. This allows for the formation of high-quality films with controlled thickness at the atomic level. Interests in plasma ALD span from microelectronics to nanotechnology, making the understanding of its principles vital.
Historical Context
The concept of atomic layer deposition evolved from traditional chemical vapor deposition methods in the late 20th century. The introduction of plasma-assisted techniques heralded a new era, enhancing the properties of deposited films while allowing for lower processing temperatures. This historical evolution highlights the significance of plasma ALD in the journey toward advanced material synthesis and its increasing relevance in high-tech applications.
Differences from Traditional ALD
Plasma ALD differs from traditional ALD primarily through the incorporation of plasma in the deposition process. In traditional ALD, thermal energy drives the reactions, potentially leading to limited growth rates and higher temperatures. In contrast, plasma-assisted techniques utilize reactive species generated in plasma, enabling faster surface reactions and the ability to work with a broader range of materials. This capability can accommodate substrates that are sensitive to heat, expanding the scope of applications for plasma ALD in fields such as optoelectronics and biomedical devices.
The innovative use of plasma distinguishes ALD processes, enhancing the versatility and efficiency of film deposition.
Fundamentals of Plasma Technology
Understanding the fundamentals of plasma technology is essential for grasping the nuances of plasma atomic layer deposition. Plasma serves as a medium that significantly enhances surface reactions during the deposition process. This enhancement results in improved film uniformity, which is pivotal in applications spanning various industries. Moreover, plasma technology allows for the manipulation of film properties by adjusting process parameters, enabling researchers and professionals to achieve specific material characteristics. Hence, a thorough understanding of plasma technology's workings can deliver crucial insights for its application in thin film deposition.
Plasma Generation Methods
Radio Frequency Discharge
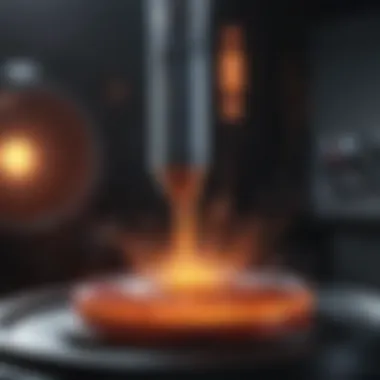
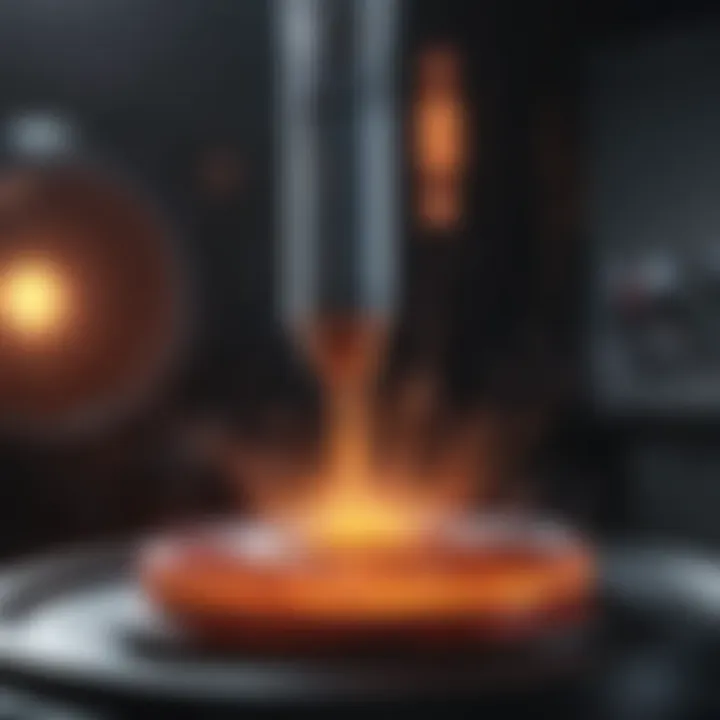
Radio frequency discharge stands out as a prominent method for generating plasma in atomic layer deposition. Utilizing alternating current at radio frequencies, this method effectively ionizes gas, producing a plasma state conducive to thin film deposition. One key characteristic of radio frequency discharge is its ability to operate at lower pressures compared to other methods. This feature enhances the control over thin film thickness and uniformity.
The high level of ionization achieved through this method also contributes positively to the energy efficiency during the deposition process. One beneficial aspect is the capability to generate uniform plasma even across complex substrate geometries. However, it is important to note that this method can entail higher equipment costs, which may pose a barrier for some users.
Microwave Discharge
Microwave discharge is another effective technique for plasma generation during atomic layer deposition. This method uses microwave electromagnetic waves to excite gas, resulting in a high-density plasma that enhances chemical reactions on the substrate surface. A key characteristic of microwave discharge is its efficiency in generating highly ionized plasmas at relatively low pressures.
One unique feature of microwave discharge is its ability to provide a larger uniform plasma volume, facilitating the deposition on larger substrates. This attribute greatly benefits industries where large coatings are needed. Nevertheless, the system's complexity can sometimes increase maintenance challenges and operational costs, making it less accessible for smaller-scale operations.
Characteristics of Plasma
Temperature and Density
The temperature and density of plasma are vital parameters influencing its performance in atomic layer deposition. The relationship between these aspects defines how reactive the plasma will be in the deposition process. Higher temperature plasma may facilitate rapid chemical reactions, leading to improved film growth rates. However, too high temperatures can harm sensitive substrates or alter desired properties of deposited films.
The density of the plasma also plays a significant role in determining the effective utilization of reactants and the overall deposition rate. For instance, higher density plasmas tend to generate more ions, which can enhance surface interactions.
Ionization and Electrical Fields
Ionization is a crucial process in forming plasma and affects the characteristics of the thin film being deposited. Ionized species contribute to surface reactions by increasing the reactivity of the plasma, thereby improving film quality. Electrical fields within the plasma can also influence the orientation and density of ions reaching the substrate. A key characteristic is that properly managed electrical fields can optimize film growth conditions.
The capability to control these electrical fields offers potential to mitigate defects in the deposited films, enhancing their overall performance. However, imbalances or improper adjustments of these fields can lead to undesirable outcomes, such as uneven deposition or film defects.
Successful plasma atomic layer deposition relies heavily on the careful management of plasma parameters including generation methods, temperature, density, ionization, and electrical fields.
Chemical Mechanisms in Plasma ALD
Understanding the chemical mechanisms in plasma atomic layer deposition (ALD) is crucial. These mechanisms dictate how materials are deposited, influencing both the quality and performance of the films formed. Plasma ALD operates by utilizing precisely controlled chemical reactions between gaseous precursors and surfaces. This results in films that exhibit high uniformity and conformity. The choice of precursor and the subsequent surface reactions greatly affect outcomes, making this knowledge vital for practical applications in various industries.
Precursor Selection
Types of Precursors
In plasma ALD, the selection of precursors is a key factor. The two main categories are metal-organic and inorganic precursors.
- Metal-organic precursors often provide a smooth film growth due to their volatility and high reactivity.
- Inorganic precursors tend to have strong metal bonds, resulting in high-quality films with robust characteristics.
The effectiveness of these precursors leads to considerable material coverage, which is a highly desirable trait in thin film technologies. Additionally, the use of suitable precursors minimizes impurities in the final product, enhancing its performance in electronic and optoelectronic applications.
Effects of Precursor Chemistry
The chemistry of chosen precursors significantly influences the resulting film properties. For example, the bond strength and molecular structure determine how quickly and uniformly a precursor can adsorb to a substrate.
A notable aspect of precursor chemistry is the reactivity. Precursors that are reactive can form layers more quickly, allowing for improved deposition rates. However, highly reactive precursors can also lead to unwanted byproducts if not carefully controlled. This duality makes understanding precursor chemistry essential for optimizing processes, balancing deposition speed and film quality.
Surface Reactions
Adsorption Processes
Adsorption is a critical phenomenon in plasma ALD where the precursor molecules adhere to the substrate surface. This process is essential for initiating the deposition of thin films.
Key characteristics of adsorption in plasma ALD include its time-dependent nature and dependency on substrate conditions. The strength of adsorption determines how readily precursors can bind, impacting film growth rates and uniformity. Effective adsorption ensures dense coverage of the substrate, minimizing voids and defects, which is crucial for applications that require high precision.
Desorption Mechanisms
Desorption mechanisms complement adsorption by removing unreacted precursors or byproducts from the surface. This regulation is pivotal because it ensures that only the intended materials are integrated into the film structure.
Different desorption rates can have a significant impact on the quality of the deposited thin film. If precursors are not adequately desorbed, they can lead to contamination or uneven film properties. Furthermore, controlled desorption can enhance repeating ALD cycles, promoting consistent and reliable thin film formation across multiple applications.
Benefits of Plasma ALD
Plasma atomic layer deposition (ALD) presents several advantages compared to other thin film deposition techniques. Understanding its benefits helps in appreciating the role it plays in various industrial applications. Plasma ALD enhances film uniformity, allows control over film thickness, and provides material flexibility. These characteristics make it especially valuable in fields such as electronics, optoelectronics, and biotechnology.
Uniformity and Conformality
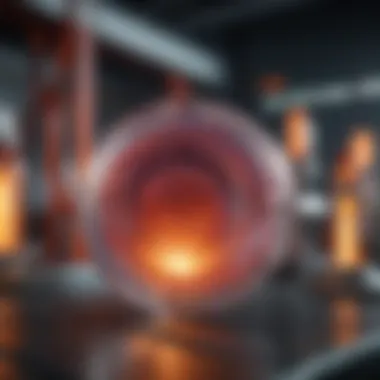
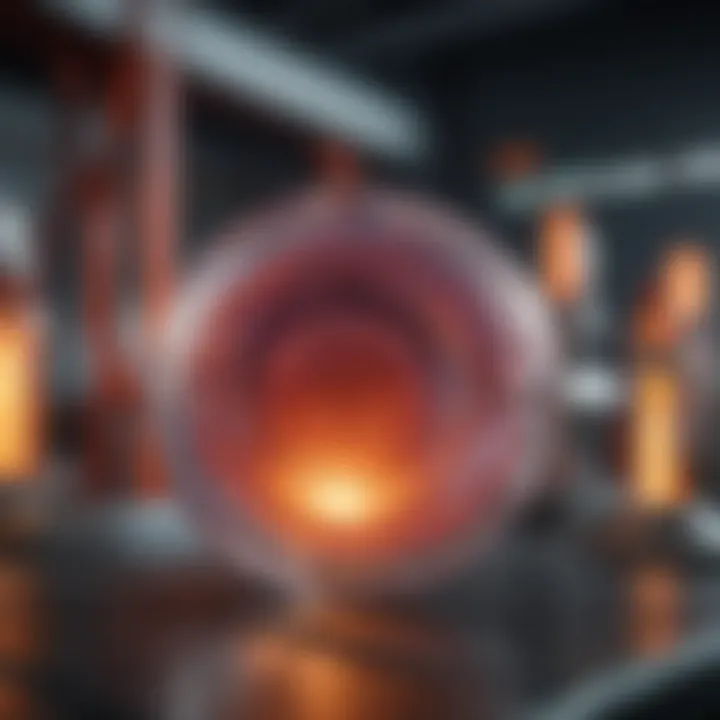
One of the cornerstone benefits of plasma ALD is its ability to deliver uniform and conformal thin films. Uniformity refers to the consistent thickness of the film across the substrate, while conformality emphasizes the film's ability to coat complex geometries.
In applications where precision is crucial, the uniform deposition is critical, especially in semiconductor devices where any irregularity can lead to function failure. Plasma ALD achieves uniformity by employing self-limiting reactions, ensuring that each layer is deposited at a constant rate. Conformality is equally important because many modern devices require coatings on intricate structures.
This capability allows plasma ALD to be the preferred method for devices with high aspect ratios, such as trenches and via holes in semiconductor devices.
Control over Film Thickness
Plasma ALD offers superior control over film thickness. Unlike traditional methods, where thickness can vary due to several factors, plasma ALD maintains precise nanoscale control throughout the deposition process. This level of accuracy is extremely benefitsl in the fabrication of devices that demand specific film thickness for optimal performance.
The ability to deposit thin films with atomic precision facilitates the production of sophisticated materials, such as high-k dielectrics in transistors. Such finetuning prevents the risk of over-deposition and wastage of material, making the process both economical and efficient.
Material Flexibility
The flexibility in material choice is another noteworthy advantage of plasma ALD. This process can accommodate various substrates and materials, making it highly versatile.
Compatibility with Various Substrates
Plasma ALD is compatible with a wide range of substrates, including silicon, metal, and glass. This attribute makes it applicable to different sectors, increasing its usability across industrial fields. The ability to deposit films on diverse surfaces is especially useful in electronics, where chips often have multiple layers of materials.
Moreover, substrates with different thermal and chemical properties can be used without compromising the film quality. This compatibility helps engineers and researchers to experiment with new designs and materials, further advancing technology.
Utilization of Diverse Materials
Plasma ALD allows for the use of various materials like oxides, nitrides, and metals. This versatility is advantageous as it opens the door for innovation in material applications. The technique can integrate complex compositions to yield advanced materials with unique properties, beneficial for high-tech applications.
By using different combinations, researchers can tailor the material properties, such as conductivity and dielectric strength, making plasma ALD an attractive choice for various applications. The possibility of deposition with a range of materials gives professionals the freedom to create custom solutions, making it a prime tool in fields demanding specialized materials.
Applications of Plasma ALD
The applications of plasma atomic layer deposition (ALD) make it a significant technique in various industries. Plasma ALD enhances material properties and provides precise control in the coating process. Its ability to deposit thin films on complex structures is valuable. Consequently, it plays a crucial role in next-generation electronic devices, energy solutions, optoelectronics, and biomedical applications.
Electronics Industry
Memory Devices
In the context of memory devices, plasma ALD enables the fabrication of high-performance and reliable components. One key aspect is its ability to create ultrathin films with excellent uniformity. This characteristic is essential for increasing component density. The stability and scalability of plasma ALD make it an attractive choice for manufacturers aiming to produce advanced memory solutions efficiently.
Furthermore, the unique feature of precise thickness control allows for the optimization of dielectric layers, which is crucial for minimizing power consumption in memory devices. However, this method can be costly, requiring significant investment in technology and equipment.
Transistors
For transistors, the specific facet that stands out is the capability of plasma ALD to deposit high-quality materials at low temperatures. This is advantageous for sensitive substrates that cannot withstand high process temperatures. The main characteristic of this deposition technique is its conformal coating ability, ensuring complete coverage on intricate geometries, which is vital for modern transistor designs.
Transistors made using plasma ALD can also exhibit superior electrical properties, leading to enhanced performance and efficiency. Nonetheless, scalability remains a challenge for mass production, which may impose limits on its adoption in certain applications.
Optoelectronics
LEDs
In the realm of optoelectronics, particularly in LEDs, plasma ALD is prominent for its role in creating optimized thin films for light-emitting layers. The precise film thickness achieved through plasma ALD improves the efficiency and brightness of LEDs. This method's ability to deposit high-purity materials prevents defects that could undermine LED performance. Moreover, a main advantage is its compatibility with various substrates, enabling diverse applications in lighting technologies.
On the downside, production time can be longer due to the nature of the process, which requires meticulous layering.
Solar Cells
Plasma ALD also plays a critical role in solar cell manufacturing. Its capability to produce uniform thin films improves the efficiency of solar panels by allowing for better light absorption. The primary characteristic of plasma ALD in this application is its ability to create defect-free semiconductor layers, which enhances the overall performance of solar cells.
This unique feature contributes to the generation of more sustainable energy solutions. However, the cost and complexity of integrating plasma ALD into existing production lines can be a limiting factor for widespread adoption.
Biomedical Applications
Biosensors
In the biomedical field, plasma ALD is significant for developing advanced biosensors. The specific aspect of surface modification allows for high sensitivity and specificity in detecting various biological analytes. A key characteristic is the ability to tailor surface properties at the nanoscale, which enhances sensor performance.
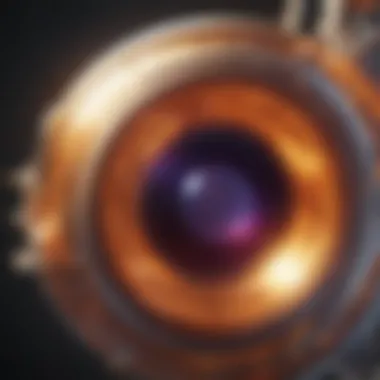
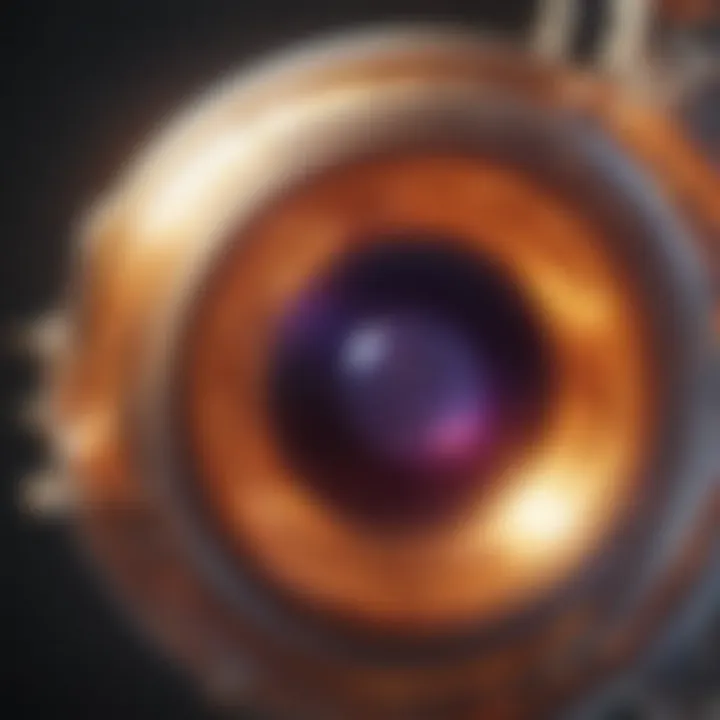
This feature makes plasma ALD a favorable choice for researchers seeking to create more effective biosensors. Despite this advantage, the translation from lab-scale to industrial applications can be challenging due to complexity in the process.
Coatings for Implants
Coatings for implants represent another crucial application. Plasma ALD provides a means to apply biocompatible layers that enhance the integration of implants with surrounding tissue. A notable characteristic is its ability to create thin films that resist corrosion and wear, ensuring longevity of implants.
Moreover, this method can improve the osseointegration process by promoting favorable biological responses. A disadvantage could be the time-consuming nature of the coating process, which might affect production timelines.
Energy Storage Devices
Batteries
In the context of batteries, plasma ALD enhances the performance of electrodes. The specific aspect of uniform coatings allows for an increase in surface area, which is vital for improving charge storage capacity. The key characteristic of this method is its precision, leading to consistent performance across batteries.
Plasma ALDβs unique feature of depositing conformal coatings helps to ensure a longer cycle life. However, one drawback is the potential increase in production costs associated with implementing this technology on a large scale.
Supercapacitors
For supercapacitors, plasma ALD is essential for improving energy density. The specific aspect here involves creating tailored materials that enhance charge and discharge rates. A primary benefit of plasma ALD in this context is its ability to produce porous structures that facilitate effective ion transport.
This unique feature can lead to better performance in energy storage solutions. On the other hand, the technologyβs complexity might deter some manufacturers focused on cost-effective solutions in the supercapacitor market.
Challenges in Plasma ALD
Plasma atomic layer deposition, despite its numerous advantages, faces significant challenges that can hinder its widespread adoption in various industries. Understanding these challenges is crucial for researchers and practitioners. By addressing these concerns, the overall effectiveness and application of plasma ALD can be optimized.
Equipment Costs
One of the primary barriers to the adoption of plasma ALD is the high cost associated with the necessary equipment. The machinery required to generate and maintain plasma is sophisticated and often expensive. These costs are due to several factors: high-quality components, precision engineering, and the necessity for advanced control systems.
Investment in equipment can be substantial. For many organizations, especially startups or smaller companies, this investment may be prohibitive. Not only must they purchase the tools, but they also need to ensure that they have skilled personnel to operate and maintain them. The need for ongoing maintenance and potential upgrades can compound initial costs. As a result, companies must weigh the benefits against these substantial financial requirements, limiting experimentation and exploration of this promising technology.
Scalability Concerns
While plasma ALD excels in creating thin films with precision, scalability remains a challenge. In laboratory settings, procedures are refined and controlled meticulously. However, when moving to larger production scenarios, maintaining the same level of quality and uniformity becomes complicated. Factors such as plasma uniformity across larger substrates or variations in deposition rates can lead to inconsistencies in film characteristics.
For industries that rely on high-throughput manufacturing, this limitation presents a serious concern. Adjusting the parameters of plasma ALD to achieve scalable uniform results requires extensive research and testing. Until solutions are developed, industries may hesitate to fully embrace plasma ALD due to these scalability issues, particularly when they compare it with more established deposition methods that are easier to scale.
Process Control and Repeatability
Another critical challenge in plasma ALD is achieving consistent process control and repeatability. The parameters involved in plasma generation, precursor interactions, and surface chemistry can vary even slightly, resulting in different outcomes. This variation can affect the overall quality and properties of the deposited films.
To ensure that film characteristics are reliable for their applications, researchers must establish stringent control over every variable in the process. This requirement can lead to increased labor and a need for advanced monitoring systems. Often, subtle changes in environmental conditions can influence results, making it difficult to replicate successful runs consistently. Companies may find that while plasma ALD can offer superior film qualities, the difficulty in process control may not justify the investment compared to simpler alternatives.
Ensuring consistent thickness and material properties through precise control of the plasma environment is fundamental for the viability of plasma ALD in commercial applications.
Future Directions in Plasma ALD Research
Plasma atomic layer deposition is gaining momentum in research. It presents vast potential for future applications. The relevance of exploring this topic cannot be overstated. This section looks into how plasma ALD can evolve, through material innovation and advanced processing techniques. The insights drawn will help in steering research toward achieving maximum capabilities of this technique.
Innovative Materials Development
The development of new materials is significant for the progress of plasma ALD. Current research focuses on finding materials with unique properties that could expand the application range. The materials can be nanoparticles, polymers, or even complex alloys. Exploring these new materials can lead to improved performance in electronic and optoelectronic devices.
Moreover, researchers are investigating bio-compatible materials that can be used for the biomedical field. The unique approach of plasma ALD allows for precise control over thin film morphology and texture, guiding the development of superior materials for various industries.
Advanced Process Techniques
Advanced process techniques are crucial for refining plasma ALD methods. One such technique is Plasma Pulse Techniques. This technique enhances deposition control by introducing pulsed plasma treatment, which allows precise deposition in short intervals. Pulsed plasma serves to control energy levels during the deposition, which may lead to better atomic layer eithers of films. It can effectively reduce defects while promoting uniformity. The benefit of this method lies in its ability to minimize unwanted reactions during the deposition phase.
Plasma Pulse Techniques
Plasma Pulse Techniques exhibit unique characteristics that set them apart from traditional processes. The ability to modulate process parameters allows researchers to optimize deposition conditions effectively. This flexibility results in high-quality films. Additionally, the pulsed operation reduces thermal stress, making this choice favorable, particularly for sensitive substrates. However, the complexity of controlling pulse parameters may present challenges in scaling lab processes to industrial applications.
Hybrid ALD Processes
Hybrid ALD Processes combine traditional ALD with new methodologies, creating a synergistic approach to thin film deposition. This method is gaining popularity due to its efficiency and versatility. In such processes, either a combination of different precursors or an integrated use of different techniques is involved. This method paves the way for the deposition of multi-layered films that exhibit specific characteristics beneficial for various applications.
One unique feature is the ability to achieve better throughput and uniformity. These collective advantages make Hybrid ALD a powerful tool in producing complex films. However, the complexity of such hybrid systems requires precise control, possibly complicating the reproducibility and scaling of the process.
"The future of Plasma ALD shows promise for evolving materials technologies and advanced processes that will redefine thin film applications."
Investing in these areas of research is critical. Continued exploration in innovative materials and advanced techniques will ensure plasma ALD remains at the forefront of thin film deposition technologies.