Exploring 3D Printing Raw Materials: Innovations & Trends
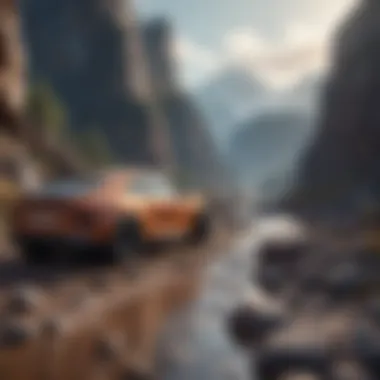
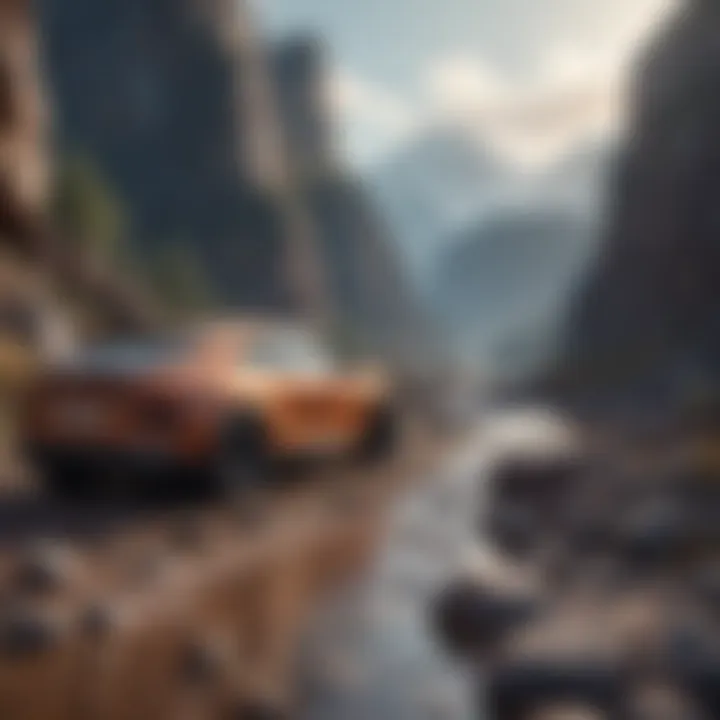
Intro
The world of 3D printing is rapidly evolving. Central to this development is the diverse range of raw materials. These materials define the capabilities, quality, and applications of 3D printed items. Understanding these materials is crucial for both innovation and effective utilization.
As 3D printing technology advances, the variety of raw materials expands. This includes traditional materials like plastics and metals, as well as newer options such as bio-based materials and composites. Each material type brings unique properties that can greatly influence the final product’s performance and sustainability.
Research Overview
Summary of Key Findings
The exploration of 3D printing raw materials reveals significant insights. Certain materials offer higher strength, while others are more flexible. Plastics such as PLA and ABS are common, but newer materials like nylon and TPU provide distinct advantages for specific applications. The rise of biodegradable options also highlights a shift towards sustainability in manufacturing.
Relevance to Current Scientific Discussions
This topic is relevant for ongoing discussions in materials science and engineering. Researchers are examining how to improve material properties and reduce environmental impact. The focus on sustainable materials aligns with global efforts to enhance production methods that do not deplete resources or harm the environment.
Methodology
Research Design and Approach
This study employs a qualitative approach to assess various raw materials used in 3D printing. Emphasis is placed on understanding their properties, uses, and innovations.
Data Collection and Analysis Techniques
Data is collected from academic sources, industry reports, and expert interviews. Analysis includes comparing material performance, sustainability benefits, and potential for future developments. By synthesizing this information, the article aims to present a clear and informative narrative around the landscape of 3D printing raw materials.
Overview of 3D Printing Technology
The realm of 3D printing technology has transformed rapidly over the past few decades, becoming a central focus in manufacturing, engineering, and design. It signifies a notable advancement that alters how products are conceptualized, designed, and produced. Understanding this technology is crucial because it lays the foundation for discussing the raw materials integral to 3D printing. In essence, 3D printing, also known as additive manufacturing, involves creating three-dimensional objects by employing computer-generated designs.
Definition and Principles
3D printing is defined as a method of fabrication that builds objects layer by layer from digital models. The principle is simple yet revolutionary. Unlike traditional subtractive manufacturing methods, which cut away material from a solid block, 3D printing adds material only where necessary. Various techniques are employed, including Fused Deposition Modeling, Stereolithography, and Selective Laser Sintering, among others. Each method has distinct characteristics and applications, providing designers with flexibility to meet diverse needs.
The process begins with a 3D model created using computer-aided design (CAD) software. The model is then broken down into thin horizontal layers, a process that prepares it for production. This preparatory stage is vital, as any flaw at this point can result in defects in the final product.
This technology's innovative nature enables complex geometries and highly customized designs. It's not just about producing standard items; it allows for the creation of unique products tailored to specific requirements. Therefore, understanding the principles behind 3D printing is essential to grasp how raw materials influence the manufacturing process and the quality of the end products.
Historical Development
The historical progression of 3D printing technology reflects a remarkable journey filled with ingenuity and evolution. The roots trace back to the early 1980s when Charles Hull invented Stereolithography. This initial method allowed for the first functional prototypes to be produced directly from CAD models. The technology has evolved significantly since then.
Throughout the 1990s, other methods were developed, such as Selective Laser Sintering and Fused Deposition Modeling, broadening the range of materials and applications in the field. As these technologies matured, they moved from hobbyist and rapid prototyping use to more robust applications across industries such as aerospace, automotive, and medical.
The introduction of new materials and enhancements in software has only accelerated this growth, making 3D printing accessible to a wider audience, including small businesses and educational institutions. Today, it is essential in fields like prototyping, tooling, and, increasingly, production, showcasing its versatility and importance.
This development journey showcases the increasing integration of 3D printing in various sectors, establishing a framework for examining the significant role that raw materials play in shaping this technological landscape.
Significance of Raw Materials in 3D Printing
Raw materials play a crucial role in the realm of 3D printing. Their significance is multifaceted, influencing not only the quality of finished products but also the overall efficiency of the printing process. Understanding the importance of these materials enables users to make informed choices that affect design, production deadlines, and costs.
Impact on Final Product Quality
The quality of the raw materials directly determines the characteristics of the printed object. This includes mechanical strength, aesthetic appeal, and functional capabilities. For instance, the selection between ABS and PLA plastics will dictate factors such as durability and finish. ABS is known for its toughness and heat resistance, while PLA offers ease of printing and biodegradability. Therefore, the judicious selection of materials aligns closely with the intended end-use of the product.
Moreover, inconsistencies in raw materials can lead to defects in the printing process. Flaws such as warping, cracking, or poor adhesion can significantly diminish the integrity of the final output. Consequently, choosing high-quality, reliable materials is fundamental in ensuring that the finished product meets the required specifications and standards.
Role in Process Efficiency
The efficiency of the 3D printing process is also reliant on the materials employed. Each type of material exhibits distinct melting points, flow characteristics, and cooling behaviors. Understanding these properties helps in optimizing printing parameters, such as temperature and speed, which can lead to time savings and reduced production costs. For instance, using materials that allow for faster cooling times may lead to quicker layer solidification, thereby enhancing build speed without sacrificing quality.
In addition, the compatibility of raw materials with various printing technologies impacts overall workflow. Materials suited for selective laser sintering (SLS) differ from those optimal for fused deposition modeling (FDM). This distinction influences equipment selection and operational procedures, ultimately determining the efficiency of production cycles.
"Choosing the right raw materials is essential for translating designs into functional parts."
Types of 3D Printing Raw Materials
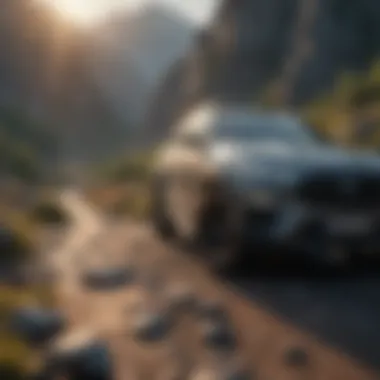
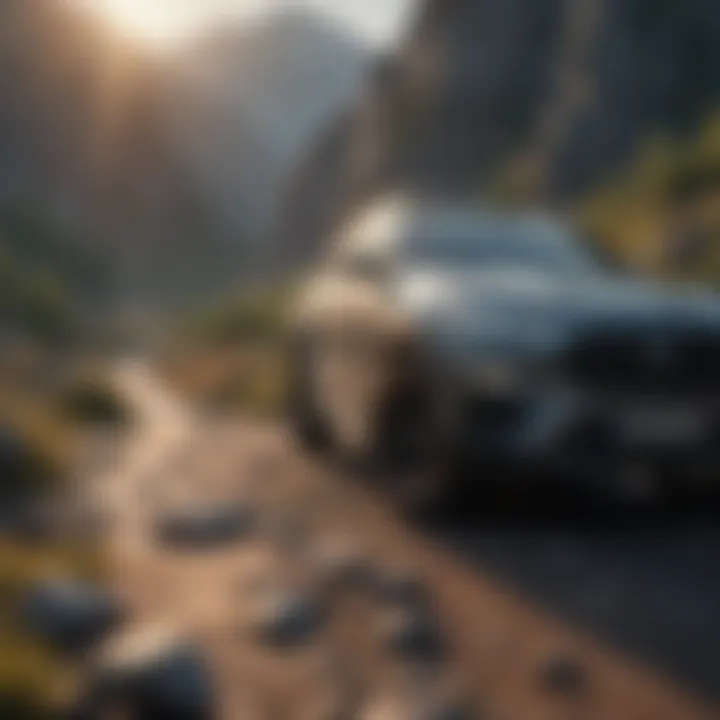
In the realm of 3D printing, the selection of raw materials is a pivotal factor that determines not only the cost but also the overall output quality. As 3D printing technology evolves, understanding the varieties of available materials can help users enhance their projects. Each type of material brings its own set of characteristics, advantages, and disadvantages, which play essential roles in both the design and production phases of 3D printing. The ongoing advancements in material science further expand the possibilities for what can be achieved with 3D printing. Here are the main types of raw materials commonly used in 3D printing, starting with plastics and moving to metals, ceramics, composites, and biomaterials.
Plastics
Plastics are the most widely used raw materials in 3D printing. Their versatility, affordability, and ease of use make them popular choices among hobbyists and professionals alike.
ABS
Acrylonitrile Butadiene Styrene (ABS) is notable for its strength and durability, making it a favored choice in many applications. It is resistant to impact and can withstand higher temperatures compared to other plastics. Unlike some other materials, ABS can be easily post-processed and painted, enhancing the finished product's appearance.
- Key Characteristic: Sturdy and heat resistant
- Advantages: Easy to print, post-processor friendly
- Disadvantages: Emission of fumes can be a concern; thus, printing should be done in well-ventilated areas.
PLA
Polylactic Acid (PLA) is a biodegradable plastic derived from renewable resources like corn starch or sugarcane. This aspect enhances its appeal in terms of sustainability. PLA is known for its ease of printing and produces high-quality surface finishes. It is widely used in educational settings and for prototyping due to its accessibility.
- Key Characteristic: Biodegradable and derived from renewable sources
- Advantages: Environmentally friendly and easy to use
- Disadvantages: Less heat resistant than ABS, making it unsuitable for high-temperature applications.
Nylon
Nylon is favored for its exceptional strength and flexibility. This material resists abrasion and is often used for creating functional parts that require durability. Its ability to absorb moisture can lead to dimensional changes, which must be managed during the printing process.
- Key Characteristic: Strong and flexible
- Advantages: Ideal for functional applications with moving parts
- Disadvantages: Requires specific printing conditions to avoid warping or other issues.
Metals
Metal materials enable the production of parts that require high strength and thermal resistance. They are typically used in engineering and manufacturing sectors, where precision and durability are crucial.
Stainless Steel
Stainless Steel is noted for its corrosion resistance and mechanical properties. This material is suitable for a range of applications, including medical instruments and industrial parts. Its durability and strength make it a reliable choice for demanding environments.
- Key Characteristic: Corrosion-resistant and strong
- Advantages: Long-lasting and versatile for various applications
- Disadvantages: Printing can be expensive and may require specialized equipment.
Aluminum
Aluminum is lightweight, making it a preferred choice for applications where weight is a factor. It also exhibits good thermal conductivity and has the ability to be finished smoothly. Aluminum parts can be used in the aerospace, automotive, and consumer goods industries.
- Key Characteristic: Lightweight and good thermal conductivity
- Advantages: Offers strength with reduced weight
- Disadvantages: Can be prone to warping and may need specific printing techniques.
Titanium
Titanium is highly versatile and known for its strength-to-weight ratio. It is particularly effective in aerospace and medical applications, where both biocompatibility and durability are critical. Though expensive to print, its benefits often outweigh the costs in specialized applications.
- Key Characteristic: High strength-to-weight ratio
- Advantages: Excellent for high-performance parts
- Disadvantages: Printing cost is notably higher compared to other metals.
Ceramics
Ceramics provide unique properties, including high-temperature resistance and hardness. Their use is growing in applications ranging from art to engineering, where thermal stability is vital. While they may not be as widely used as plastics or metals, their specialized applications make them essential in certain fields.
Composites
Composite materials enhance the characteristics of basic materials. By combining two or more materials, such as carbon fiber with resin, composites can offer improved strength and reduced weight. This technology is utilized in various industries to optimize performance and durability.
Biomaterials
Biomaterials are increasingly relevant in medical applications, such as implants and tissue engineering. These materials are designed to interact safely with biological systems, and their development is ongoing. The properties of biomaterials are crucial for ensuring patient safety and efficacy in medical devices.
Properties of 3D Printing Raw Materials
Understanding the properties of 3D printing raw materials is essential for anyone involved in this technology. The properties determine how a material behaves under various conditions and how it will perform in the final product. Factors like strength, heat endurance, and resistance to chemicals all play significant roles in deciding which material to use for a specific application. Having a good grasp of these properties not only enhances product quality but also optimally utilizes resource efficiency.
Mechanical Properties
Mechanical properties are among the most critical aspects of raw materials in 3D printing. They define how materials respond to loads or forces, impacting the durability and reliability of the final products.
Tensile Strength
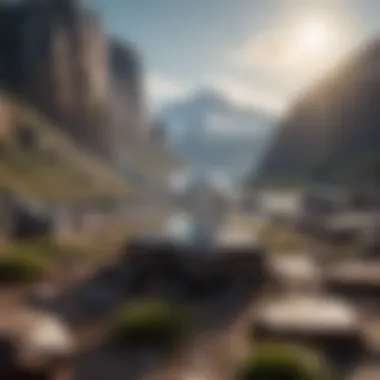
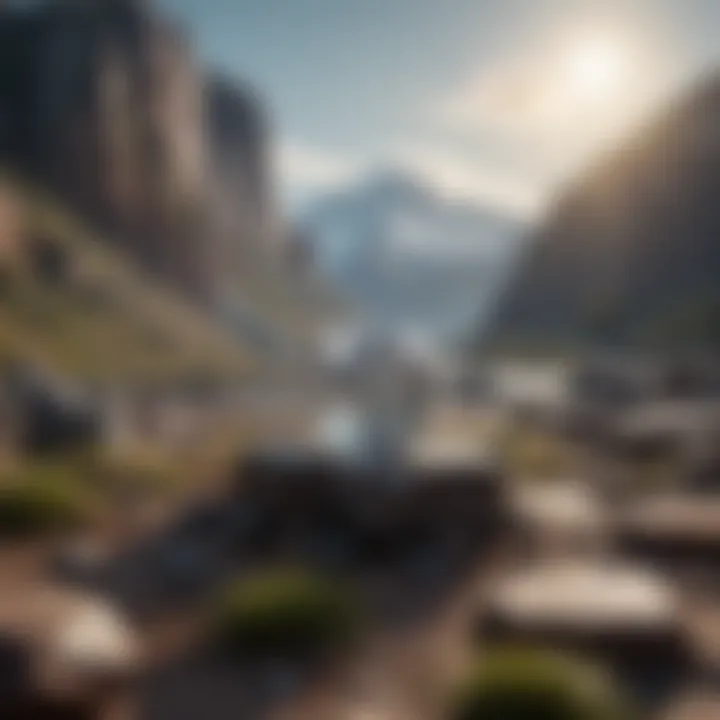
Tensile strength refers to the maximum amount of stretching force a material can withstand before failing. It is crucial for any application where the printed objects will undergo tension. A higher tensile strength usually indicates a reliable, durable product. It is a popular choice in industries where strength is non-negotiable, such as aerospace and automotive. One notable feature of tensile strength is that it varies with different materials. For instance, Nylon, known for its excellent tensile strength, allows the creation of structural components that endure significant stress. The disadvantage, however, is that materials with high tensile strength may also be more brittle than softer options.
Flexural Strength
Flexural strength is the ability to resist deformation under load. This characteristic is vital when printed parts are subjected to bending forces. High flexural strength is beneficial in parts that experience loads from multiple angles. For example, ABS plastics exhibit strong flexural strength, making them suitable for applications ranging from consumer goods to automotive parts. However, the trade-off is often a compromise in other aspects like thermal resistance.
Durability
Durability encompasses the material’s ability to withstand wear, pressure, or damage. It is an essential property for items expected to endure harsh conditions. Materials such as Polycarbonate are known for their durability. They are commonly used in safety equipment, lending longevity to the products. However, durable materials may come with the drawback of being more challenging to print, requiring specific settings and equipment.
Thermal Properties
Thermal properties examine how materials respond to heat. Understanding these aspects is essential for applications that involve high temperatures or require specific thermal performance.
Melting Point
The melting point is the temperature at which a solid material turns into liquid. This characteristic influences the printing process since different materials have various melting points. For example, PLA has a relatively low melting point, making it easier to work with. This is significant in ensuring that the printed object does not deform during printing. However, low melting points can also lead to issues in high-temperature environments, making different materials more suitable for specific applications.
Thermal Conductivity
Thermal conductivity measures a material's ability to conduct heat. This property holds importance in applications where heat dissipation is necessary. For instance, materials like Aluminum have high thermal conductivity and are preferred for components in heat sinks. However, materials with high thermal conductivity may also face challenges such as heat resistance during printing.
Chemical Resistance
Chemical resistance is vital for materials used in environments where they will be exposed to various substances. Strong chemical resistance prevents degradation and maintains the integrity of the printed items. For instance, certain types of Nylon can withstand exposure to chemicals, making them suitable for industrial applications. However, some high-performance materials may have limited flexibility or higher costs, which must be considered when selecting materials for specific applications.
In summary, the properties of 3D printing raw materials significantly affect the outcomes in various industries. Knowing the mechanical, thermal, and chemical characteristics of these materials enables better choices that enhance product durability and performance.
Innovation in Raw Materials for 3D Printing
The realm of 3D printing is constantly evolving. One of the vital aspects of this evolution is the innovation of raw materials. Changes in material composition and structure can significantly affect the capabilities and possibilities of 3D printing technologies. Innovations in materials lead to improved mechanical properties, new applications, and even increased sustainability in production processes.
Examining innovations gives insight not just into material performance but also broader industry trends. For instance, enhanced materials can facilitate more efficient production with less waste. This progress benefits not only manufacturers but also end-users who seek greater functionality in their printed objects.
Development of New Materials
The development of new materials is a fundamental area of focus in 3D printing innovation. Recent advancements have enabled the introduction of a variety of materials, including high-performance plastics, metals, and biocompatible materials. Each of these materials has unique properties that cater to specific needs in various industries.
- High-Performance Plastics: Materials such as polyether ether ketone (PEEK) demonstrate excellent temperature resistance and strength, making them suitable for the aerospace and medical sectors.
- Advanced Metals: Innovations have also led to the creation of novel alloys specifically designed for 3D printing. These materials can improve strength-to-weight ratios and thermal properties.
- Biocompatible Materials: Derived from natural substances, these materials find applications in medical devices and implants, ensuring compatibility with human tissue.
The exploration of these new materials not only improves product quality but also opens doors to entirely new applications that were previously unattainable.
Nanotechnology in Materials
Nanotechnology plays a crucial role in developing advanced raw materials for 3D printing. By manipulating materials at the molecular or atomic level, scientists can create composites that possess enhanced properties. This includes improvements in strength, durability, and thermal stability.
Nanomaterials can also enable the fabrication of lighter and stronger products. For example, integrating nanofillers such as carbon nanotubes into thermoplastics can significantly augment mechanical performance without adding much weight. This aspect is particularly attractive in areas such as aerospace, where efficiency is vital.
Furthermore, nanotechnology allows for the creation of materials with unique functionalities, such as self-healing properties. As materials age or sustain damage, they can automatically repair themselves, increasing the longevity and reliability of 3D printed components.
The continued exploration of advanced raw materials through innovation and nanotechnology positions 3D printing as a rapidly growing field, enhancing its relevance across multiple sectors.
Advancements in raw materials are foundational for ensuring that industry demands are met. Each innovative development has the potential to affect the efficiency, sustainability, and functionality of 3D printing processes.
Sustainability of Raw Materials
Sustainability in the context of 3D printing raw materials has gained increased importance. It is crucial to address the environmental implications of material sourcing, usage, and post-production. Companies and researchers are increasingly recognizing that sustainability affects not just their brand image but also the long-term viability of the technologies they deploy.
To understand sustainability more clearly, one must consider both the ecological footprint of raw materials and their life-cycle impacts. By employing sustainable practices, manufacturers can reduce waste, conserve resources, and contribute to a healthier ecosystem.
Source Materials and Environmental Impact
Source materials used in 3D printing predominantly come from fossil fuels or mining activities. Plastics like Acrylonitrile Butadiene Styrene (ABS) and Polylactic Acid (PLA) exemplify this dichotomy. ABS, while offering excellent mechanical properties, is derived from petroleum, posing concerns about depleting non-renewable resources. On the other hand, PLA is made from renewable resources like cornstarch or sugarcane. This distinction affects not only the source of the materials but also how they impact the environment.
Moreover, the extraction processes for metals, such as Titanium, can lead to significant land degradation and pollution. Advancements in sustainable sourcing emphasize the use of materials that are abundant and renewable.
When evaluating environmental impact, one must also consider the carbon footprint associated with transportation and production. Using local materials can mitigate some of these impacts, thus promoting local economies while reducing emissions.
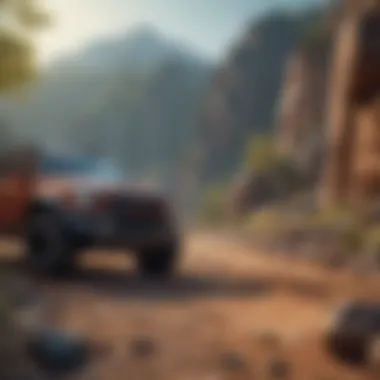
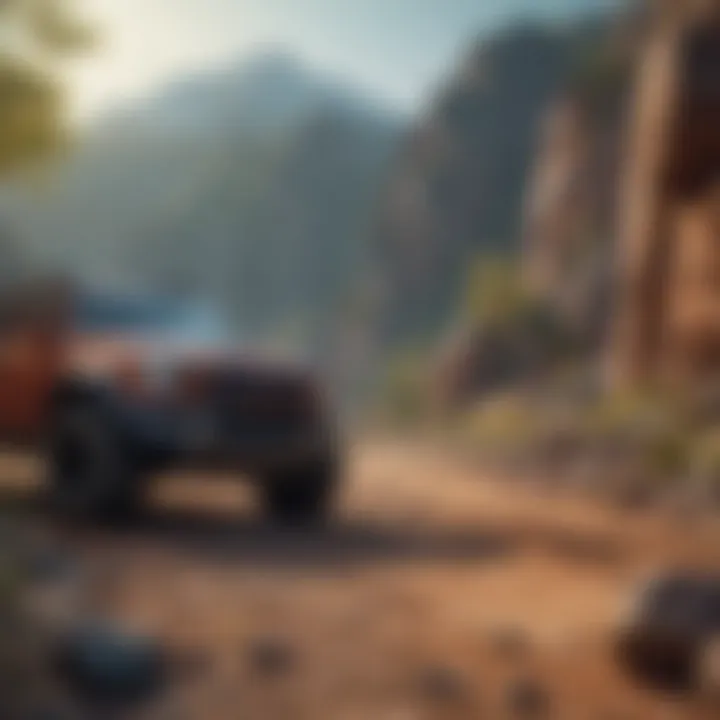
"The choice of raw materials is not merely a technical decision; it encompasses broader environmental responsibilities that define the sustainability of 3D printing practices."
Recyclability and Waste Management
Recyclability is a central theme of sustainability within 3D printing. The industry produces a considerable amount of waste from failed prints and support structures. Addressing this waste is essential for improving the overall sustainability of the process. Methods like reusing failed prints and recycling support materials can significantly minimize waste.
Current trends show a shift toward materials that can be recycled more efficiently. For instance, thermoplastics such as PLA can be reprocessed into new filaments or products, creating a circular economy model. Furthermore, companies are developing bioplastics that are not only compostable but also designed for reusability.
Waste management strategies are also evolving. With enhanced recycling technologies, more materials can be reincorporated into the manufacturing cycle. Effective waste management, therefore, is not just about disposal but understanding product life cycles, enhancing material recovery facilities, and encouraging consumers to participate in recycling initiatives.
Overall, the focus on sustainability in raw materials for 3D printing is not simply an ethical choice; it represents a fundamental transformation in manufacturing processes that balances economic viability with environmental stewardship.
Future Trends in 3D Printing Raw Materials
The landscape of 3D printing continues to evolve rapidly, driven by advancements in technology and materials. Understanding future trends in 3D printing raw materials is crucial for grasping the direction this industry is headed. These trends not only impact the technical aspects of how products are printed, but also influence design choices and manufacturing processes across various sectors.
The exploration of future trends involves examining several key elements. Among these, market forecasts provide valuable insight into where investments and developments are likely to flow. Additionally, emerging applications showcase the practical utilization of these materials in innovative ways, expanding the horizons of what 3D printing can achieve.
Market Forecasts
Market forecasts for 3D printing raw materials illustrate a robust growth trajectory. According to various industry reports, the 3D printing materials market is expected to witness significant expansion over the next five to ten years. Factors driving this growth include an increasing adoption of additive manufacturing in various industries such as aerospace, healthcare, and automotive.
To highlight some statistics:
- Market Value: The global market for 3D printing materials was valued at approximately $1 billion in 2020 and is projected to exceed $3 billion by 2025.
- Growth Rate: The compound annual growth rate (CAGR) is estimated to be around 25% during the forecast period.
Such growth is attributed to the demand for customized products and the benefits of rapid prototyping capabilities offered by 3D printing. The emergence of new materials, such as bioprintable substances and multi-material composites, further fuels market expansion.
Emerging Applications
The realm of emerging applications for 3D printing raw materials is vast and varied. Increasingly, researchers and industries leverage these materials for innovative solutions. Here are some noteworthy applications that are gaining traction:
- Biomedical Devices: The healthcare sector is seeing a rise in the use of 3D printing for custom implants and prosthetics made from biomaterials. These devices can be tailored to fit individual patients, enhancing both comfort and functionality.
- Construction: Large-scale 3D printing is being explored for constructing buildings. Materials like concrete mixtures that can be extruded through a printer are showing promise for cost-effective housing solutions.
- Aerospace: With the pursuit of lightweight and durable components, aerospace industries utilize materials such as titanium and carbon fiber in 3D printing to create parts that meet stringent regulatory standards with reduced weight.
- Consumer Products: Companies are increasingly using 3D printing for creating unique, custom products that appeal to customer individuality while minimizing waste.
"The adoption of 3D printing technologies will redefine traditional manufacturing paradigms, allowing for the creation of parts that were previously impossible to fabricate."
Overall, the exploration of future trends in 3D printing raw materials reveals a landscape lively with potential. It emphasizes the need for continuous innovation and adaptation to stay relevant in a rapidly evolving market.
The End
The conclusion is a vital component of any article, offering a synthesis of the information presented and reiterating the importance of the discussed topics. In this article, the examination of 3D printing raw materials has shed light on several key elements that resonate deeply with various stakeholders in the field.
First, the discussion on different types of raw materials explored how each category — such as plastics, metals, ceramics, composites, and biomaterials — can influence the performance and applications of 3D-printed products. Knowing which material to select is crucial for achieving desired properties, enhancing performance, and ensuring product longevity.
Moreover, the properties of these materials, including mechanical, thermal, and chemical characteristics, enable manufacturers to tailor their approaches for specific applications. Understanding these attributes allows engineers and designers to make informed decisions that greatly affect product quality and manufacturing efficiency.
The importance of innovation cannot be understated. As new materials are developed, such as composites enhanced with nanotechnology or eco-friendly bioplastics, they expand the horizons of what is possible in 3D printing. This drive for progress plays a critical role in advancing additive manufacturing technologies and improving their applicability across diverse industries.
Sustainability stands out as one of the more pressing considerations in today's manufacturing landscape. The promise of using recycled materials and striving for lower environmental impact aligns with global trends towards greener industrial practices. Addressing the recyclability and sourcing of materials ensures that 3D printing remains a forward-thinking approach in production.
In summary, this exploration not only highlights the technical specifications of various materials but also emphasizes their implications for future trends. Market forecasts and emerging applications signal an ongoing evolution in the field, making it essential for students, educators, and professionals to remain attuned to these developments. Thus, understanding raw materials for 3D printing is not merely academic; it is imperative for staying relevant in technology and manufacturing domains. This article serves as a comprehensive resource to enrich your knowledge and help guide thoughtful decisions in this vibrant field.
References and Resources
In the exploration of 3D printing raw materials, having access to reliable references and resources is crucial for enhancing understanding and staying updated with the rapidly evolving field. The significance of curated materials lies in their capacity to provide in-depth knowledge, support research efforts, and inspire innovation. As 3D printing technology progresses, a solid foundation of information becomes vital for students, educators, and professionals alike.
Importance of References
- Credible Information: It is essential to access materials from reputable sources to ensure the accuracy and reliability of the information. Academic papers, industry reports, and authoritative websites serve as benchmarks for understanding complex topics related to 3D printing raw materials.
- Research Support: For students and researchers, a robust set of references is crucial for crafting well-informed projects. Accessing peer-reviewed journals helps in finding empirical data that can support claims and enhances the overall credibility of academic work.
- Trend Analysis: Keeping track of the latest advancements in materials is fundamental. Comprehensive resources help identify patterns in the development of new materials and innovations, aiding in professional growth and decision-making.
Recommended Resources
- Wikipedia: A good starting point to get overviews and basic information about various aspects of 3D printing materials. However, always cross-reference with more authoritative sources.
- Encyclopedia Britannica: Offers well-researched articles and insights into the history and technical details regarding 3D printing and its materials.
- Academic Journals: Journals such as Additive Manufacturing and Journal of Materials Processing Technology publish the latest research on materials used in 3D printing, covering both theoretical aspects and practical applications.
- Online Forums: Communities on platforms like Reddit can provide unique insights and real-world experiences from users and professionals.
- Industry Reports: Organizations like MarketsandMarkets and Smithers Pira provide market forecasts and analyses focusing on emerging trends in the materials sector of 3D printing.
Considerations
When utilizing references, critical evaluation is necessary. Not all information is equally valuable. Always consider the date of publication, the qualifications of the authors, and the methodologies used in the studies cited. Moreover, diving into diverse types of resources fosters a comprehensive viewpoint and encourages innovative thinking concerning the application and sustainability of 3D printing materials.