Comprehensive Study on Electron Beam Melting of Titanium
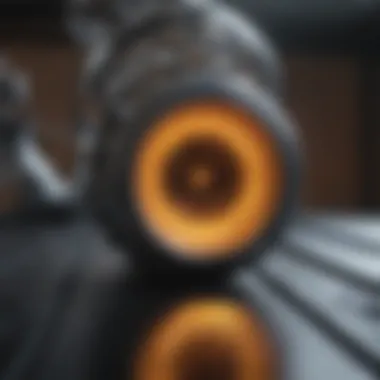
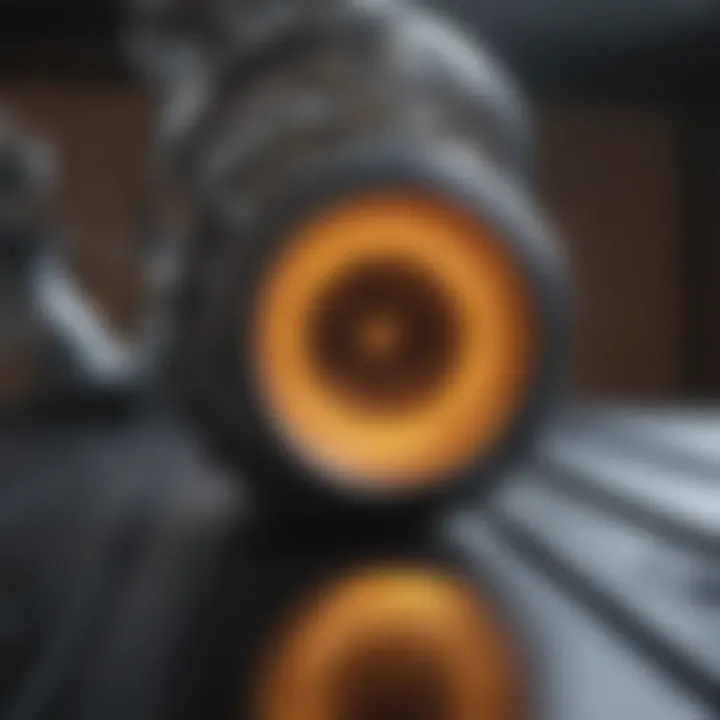
Intro
The realm of manufacturing has seen significant transformations due to advancements in technology. Particularly, the electron beam melting (EBM) process has garnered attention in the realm of titanium fabrication. This article aims to explore EBM as it applies to titanium, a material widely valued for its strength-to-weight ratio and corrosion resistance. By harnessing the unique properties of electron beams, EBM provides a method of additive manufacturing that is precise and efficient. This introduces numerous possibilities for various industries including aerospace, medical, and automotive sectors.
Understanding EBM involves delving into its fundamental principles, advantages, and limitations. Moreover, considering the evolving nature of technology, it's essential to discuss recent advancements and innovations in this field. As titanium increasingly becomes integral to modern engineering solutions, the need for efficient production methods like EBM cannot be overstated.
Research Overview
Summary of Key Findings
This comprehensive study reveals critical insights regarding EBM in titanium production. Key findings highlight:
- Fundamental principles: The process utilizes an electron beam focused into a small spot to melt titanium powder layer by layer, effectively creating intricate structures with high precision.
- Advantages: EBM offers significant advantages such as reduced material wastage, no need for support structures in complex geometries, and the ability to manipulate properties at the microscopic level.
- Limitations: Despite its benefits, challenges remain, including constraints related to build size, material costs, and the specific environmental conditions required for effective operation.
- Applications: Industries implementing EBM range from aerospace to medical implants, showcasing its versatility in producing high-performance parts.
Relevance to Current Scientific Discussions
EBM’s relevance extends beyond traditional manufacturing discussions. It ties into broader themes of sustainability and efficiency in production. As the industry moves towards greener technologies, EBM stands out by minimizing material usage and energy consumption when compared to traditional subtractive techniques. Advances in this discipline raise questions about future manufacturing paradigms and the role of titanium as a central material in these developments.
Methodology
Research Design and Approach
This study employs a qualitative approach. By reviewing existing literature and analyzing case studies, the discussion articulates the intricate processes involved in EBM. This allows for comprehensive insights into both theoretical and practical applications in the titanium sector.
Data Collection and Analysis Techniques
Data was obtained from a variety of academic journals, industry reports, and technical documents focusing on EBM technology. The analysis is structured to compare and synthesize these resources, leading to an effective understanding of the state of EBM regarding titanium. The synthesis process ensured that all relevant aspects were covered, fostering a rounded perspective on the topic.
"The electron beam melting process not only revolutionizes titanium manufacturing but also sets a precedent for future material processing techniques."
The study aims to be a vital asset for students, researchers, and professionals in the field. By providing in-depth analysis and critical perspectives, the discussion serves to enhance understanding of EBM and its implications for titanium production.
Preamble to Electron Beam Melting
The exploration of Electron Beam Melting (EBM) offers significant insights into advanced manufacturing processes, especially concerning titanium. EBM is an additive manufacturing technique that uses focused electron beams to melt and fuse materials layer by layer. This process is crucial for producing complex titanium parts that are both lightweight and strong, making it particularly valuable in sectors such as aerospace, medical, and automotive industries.
Understanding EBM is crucial for those involved in materials science, engineering, and manufacturing. The article investigates the underlying principles of this technology, its advantages, limitations, and various applications. By examining these elements, we can better appreciate how EBM contributes to the development of innovative titanium components necessary for demanding applications.
Definition of Electron Beam Melting
Electron Beam Melting (EBM) is an additive manufacturing process that uses a high-energy electron beam in a vacuum environment to melt titanium powder. The process deposits and fuses powdered titanium, layer by layer, to create a solid part from a digital model. The electron beam is controlled by electromagnetic fields, allowing precise aiming at specific areas of the powder bed. As the beam melts the titanium powder, it solidifies rapidly, forming a dense and strong part.
EBM operates under specific conditions, primarily in a vacuum, which prevents oxidation and contamination of the material. This feature is particularly advantageous for titanium, a material known for its reactivity at elevated temperatures. The ability to process titanium in these controlled conditions enhances the quality and performance of the final product.
Historical Context
The development of Electron Beam Melting technology can be traced back to the late 1980s when researchers began exploring electron beam welding and melting techniques for additive manufacturing. The journey started with industrial applications and slowly advanced into the realm of complex part fabrication.
In the 1990s, EBM gained significant attention due to its effectiveness in producing intricate geometries and its higher precision compared to traditional manufacturing methods. Initially, it was mostly applied in the aerospace sector, where titanium components are highly sought after due to their strength-to-weight ratio. Over the years, advancements in EBM technology have led to broader applications, including medical implants and high-performance automotive components. This evolution reflects not only improvements in the technology itself but also the growing demand for tailored, high-performance materials in various industries.
The ongoing research and development in EBM continue to shape its application landscape, ensuring it remains a vital technology in the context of modern manufacturing.
Fundamentals of the Electron Beam Melting Process
Understanding the fundamentals of the Electron Beam Melting (EBM) process is essential for grasping its significance in titanium manufacturing. EBM technology employs controlled electron beams to melt titanium powder layer by layer, thus allowing for precise and complex geometries. This section will break down the operating principles, components essential to the EBM system, and the interaction between the electron beam and the titanium material itself. Such knowledge is crucial not just for practical applications but also for exploring further innovations in the field.
Operating Principles
The operating principles of EBM revolves around directing focused electron beams onto powdered titanium. The process begins inside a vacuum environment, where the absence of atmospheric oxygen helps prevent oxidation of titanium. The electron beam, generated by an electron gun, hits the surface of the titanium powder selectively based on a pre-defined 3D model. Each layer is melted and fused, creating a solid structure as it cools.
This layer-by-layer approach minimizes heat distribution, reducing thermal stress that often leads to warping. Additionally, temperature control is vital, as it influences the microstructure and mechanical properties of the finished part. The capability to finely control the melting process is one of EBM's core advantages, making it suitable for applications requiring high precision.
Components of the EBM System
The EBM system consists of several key components that work in tandem to ensure a successful build.
- Electron Gun: Generates the high-energy electron beam required for melting.
- Vacuum Chamber: Maintains a low-pressure environment to prevent oxidation.
- Powder Feed System: Distributes titanium powder onto the build plate.
- Build Platform: Serves as the foundation where the part is constructed.
- Control Software: Governs the operation of the machine, ensuring accuracy in melting and scanning.
Each component must function correctly for optimal results. The electron gun must produce a stable and focused beam, while the vacuum chamber must maintain proper pressure to facilitate high-quality prints.
Interaction of Electron Beam and Material
The interaction between the electron beam and titanium is critical in defining the mechanical properties of the finished product. As the beam strikes the powder, it transfers energy which leads to rapid heating and melting of the titanium particles. This not only fuses individual layers but also influences how the titanium solidifies and crystallizes.
The energy density of the beam can be adjusted, allowing for variations in melting speed and penetration depth. A higher energy density typically leads to a denser and more homogeneous structure, which translates to improved mechanical properties. Moreover, understanding how the electron beam interacts with the material can help in developing strategies to mitigate defects like porosity, which may impact performance in demanding applications.
The fundamental principles of EBM demonstrate its capability for producing intricate geometries with superior mechanical properties, essential for industries such as aerospace and medical devices.
Properties of Titanium Relevant to EBM
Understanding the properties of titanium is crucial in the context of electron beam melting (EBM). Titanium's unique characteristics significantly influence the EBM process and determine the quality of the final product. This section will cover important aspects such as material characteristics and reactivity concerns.
Material Characteristics
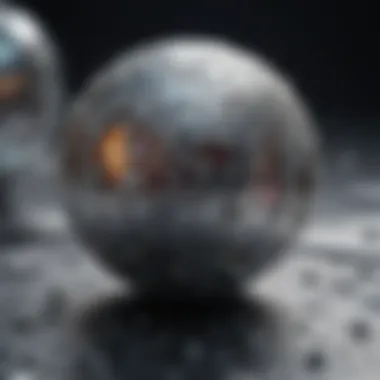
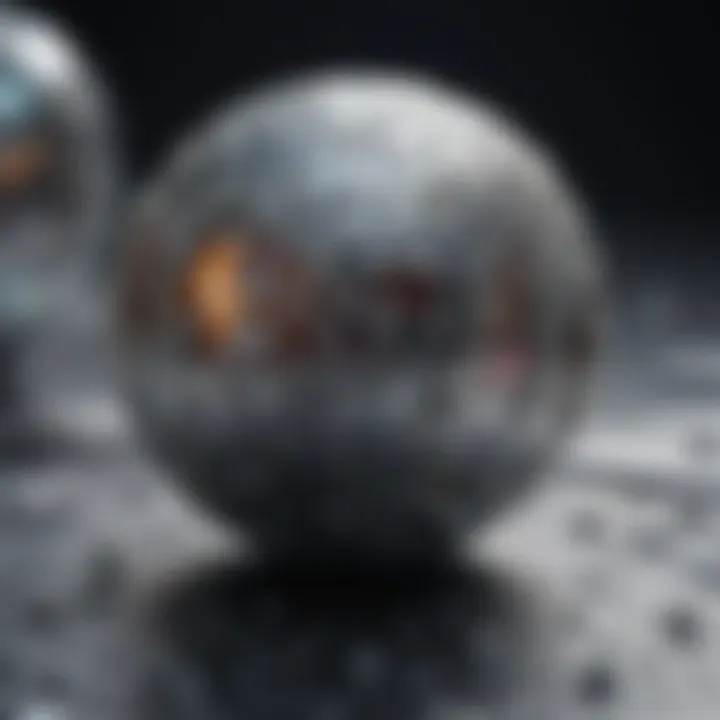
Titanium possesses a high strength-to-weight ratio, which makes it ideal for applications requiring lightweight materials without sacrificing strength. It has a low density, usually around 4.5 g/cm³, which is significantly less than steel while still offering comparable strength. This characteristic is beneficial in industries like aerospace and automotive, where reducing weight leads to improved fuel efficiency and performance.
Another important property of titanium is its excellent corrosion resistance. This occurs due to the formation of a naturally occurring oxide layer on its surface, which protects the underlying metal. Corrosion resistance is particularly essential in marine and chemical environments where materials face harsh conditions. The ability to withstand extreme temperatures also adds to its versatility; titanium can maintain its integrity at high temperatures without losing its mechanical properties.
Additionally, titanium exhibits great biocompatibility, making it highly valued in the medical field, especially for implants and prosthetics. As the demand for advanced medical devices expands, the significance of titanium in EBM becomes even more apparent.
Reactivity and Oxidation Concerns
Despite its beneficial properties, titanium is highly reactive, especially at elevated temperatures. The interaction of titanium with oxygen is particularly concerning due to its tendency to oxidize. This oxidation can lead to defects within the material, such as embrittlement and compromised mechanical properties. In the context of the EBM process, a controlled atmosphere is crucial during fabrication to mitigate these risks.
Most EBM systems utilize a vacuum or inert gas environment to prevent undesirable reactions with atmospheric elements. This control ensures that the titanium powder remains unoxidized, preserving its desirable qualities. Without proper precautions, the oxidation process can undermine the advantages of titanium, resulting in components that do not meet required specifications.
Advantages of Electron Beam Melting for Titanium Production
The advantages of Electron Beam Melting (EBM) in titanium production are manifold and hold significant importance in the current landscape of manufacturing. Titanium is renowned for its strength-to-weight ratio and corrosion resistance, making it desirable across various industries, including aerospace and medical. EBM offers unique benefits in processing this metal, which greatly enhance its applicability and overall performance in end products.
Precision and Accuracy
One of the foremost advantages of EBM is its high precision and accuracy in layer-wise manufacturing. The electron beam achieves a focus on a very small spot size, which allows precise melting of titanium powder. This characteristic is critical when producing complex geometries and parts with intricate designs.
In traditional methods, achieving such accuracy can be extremely challenging. EBM provides the capability to build parts with tolerances that meet stringent industry standards. This level of precision results in a reduction of post-processing needs, thus promoting cost-effectiveness in manufacturing. Furthermore, enhanced accuracy aids in producing components that can pass rigorous tests and inspections.
Reduced Material Waste
Another vital advantage of EBM is the reduced material waste during the production process. Unlike subtractive manufacturing methods that remove material from a solid block, EBM utilizes a powder bed approach, where only the necessary material is melted and solidified. The deposition of titanium powder is highly efficient, ensuring that minimal excess material is generated.
In practical terms, this means that manufacturers can achieve significant cost savings and sustainability. The use of titanium powder minimizes wasted resources, which is especially important given the high cost and rarity of titanium. Scrap metal is also often recyclable, further enhancing the eco-friendliness of this process.
"Significantly reduced material waste leads to both financial efficiency and environmental sustainability, making EBM a forward-thinking choice."
Enhanced Mechanical Properties
The mechanical properties of titanium parts produced by EBM are notably superior due to the rapid solidification rates and controlled cooling environments. This process allows for refined microstructures within the titanium, resulting in enhanced tensile strength, fatigue resistance, and overall durability.
Parts manufactured through EBM often exhibit a more homogeneous structure than those created via conventional methods. The microstructural integrity translates to enhanced performance during service, making EBM-fabricated components ideal for demanding applications in aerospace and medical fields. Additionally, the ability to tailor properties through controllable parameters adds strategic benefits in design and functionality.
In summary, the advantages of Electron Beam Melting in titanium production underline its importance as a pioneering manufacturing method. This process not only ensures precision and accuracy but also leads to significant material savings and superior mechanical properties for titanium components. Such capabilities position EBM as a formidable option for industries requiring high-performance titanium parts.
Limitations and Challenges of EBM in Titanium Manufacturing
Understanding the limitations and challenges of Electron Beam Melting (EBM) in titanium manufacturing is crucial for potential applications and advancements in this field. Despite its many benefits, EBM faces several roadblocks that could impact its adoption in various industries. Addressing these limitations can lead to improved processes and enhanced outcomes for titanium production. Evaluating the technical and financial considerations gives a comprehensive view of why overcoming these challenges is essential.
Technical Constraints
Technical issues in EBM revolve around the complexity of the process and the equipment used. Key constraints include:
- Process Parameters: The need for precise control of parameters such as beam speed, focus, and energy density can affect the final product's quality. Any deviation can lead to defects in the titanium parts.
- Equipment Costs: EBM machines require substantial investment in high-precision components and materials. This results in higher initial costs compared to other manufacturing methods.
- Material Limitations: Certain titanium alloys may not perform well in the EBM process. Finding optimal materials that can sustain the high temperatures and energy levels required remains a challenge for manufacturers.
- Cooling Rate Management: Rapid cooling rates can cause residual stresses that affect mechanical properties. Managing heat dissipation is vital to maintaining integrity in titanium parts.
Addressing these technical issues is critical. Improving the design of EBM systems and refining process control methods could help enhance the viability of this manufacturing technique.
Financial Considerations
The financial implications of EBM in titanium manufacturing also present notable challenges. Key points include:
- High Initial Investment: The upfront cost for EBM technology is considerable. This expense can discourage smaller companies or startups from investing in EBM systems.
- Operational Costs: Operating and maintaining EBM machines requires skilled personnel and consistent investment in spare parts and maintenance. This can increase the overall cost of the manufacturing process.
- Market Competition: With competing technologies like Selective Laser Melting (SLM) being more prevalent, there is constant pressure on EBM technologies to prove their cost-effectiveness.
- Return on Investment: Many companies find it challenging to justify the return on investment for EBM compared to traditional methods. Risk assessment becomes increasingly complex, impacting decision-making processes.
"Understanding the limitations is the first step towards innovation and improvement."
By examining these aspects, manufacturers, researchers, and policymakers can collaboratively devise strategies that facilitate the growth and wider adoption of Electron Beam Melting for titanium production.
Applications of Electron Beam Melting Technology
The applications of Electron Beam Melting (EBM) technology are wide-ranging. This section discusses its uses across multiple industries, emphasizing the unique advantages and considerations each sector faces when implementing EBM for titanium production.
Aerospace Industry
The aerospace sector necessitates materials that can endure extreme conditions, including high temperatures and pressures. EBM is particularly relevant here due to titanium's strength-to-weight ratio. In this industry, components such as airframes, turbine blades, and structural parts benefit from EBM’s ability to produce intricate geometries. Moreover, EBM creates dense metals, which is crucial for safety in aerospace applications.
One notable example includes the development of lightweight titanium parts for aircraft. The reduced weight improves fuel efficiency and overall performance. Furthermore, the application of EBM leads to fewer defects than traditional manufacturing methods, which is vital when working with materials for aircraft.
Medical Devices
In the medical field, precision and biocompatibility are paramount. EBM technology facilitates the production of complex geometries that are often required in prosthetics and implants. Its capability for customizing products to fit individual patient needs is a significant advancement.
Titanium is preferred for many medical implants due to its corrosion resistance and strength. Examples include orthopedic implants and dental devices. EBM allows for improved surface characteristics, which enhance osseointegration—the process where bone grows around an implant. This feature significantly contributes to device longevity and effectiveness.
Automotive Sector
The automotive industry also recognizes the benefits of EBM for titanium components. As manufacturers focus on reducing vehicle weight to improve efficiency, titanium parts produced via EBM can serve as replacements for heavier materials.
Applications in this sector include high-performance components such as valves, exhaust systems, and suspension parts. These components benefit from the customizability of EBM, allowing for designs that significantly enhance performance while maintaining durability. Additionally, the lower production waste associated with EBM aligns with current trends in sustainability within the automotive industry.
Post-Processing of EBM Titanium Parts
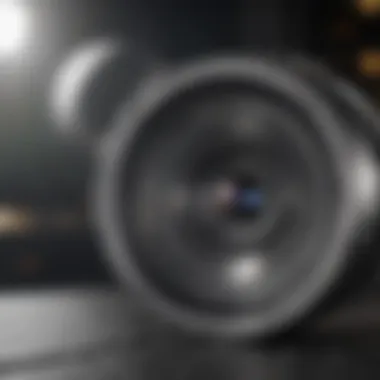
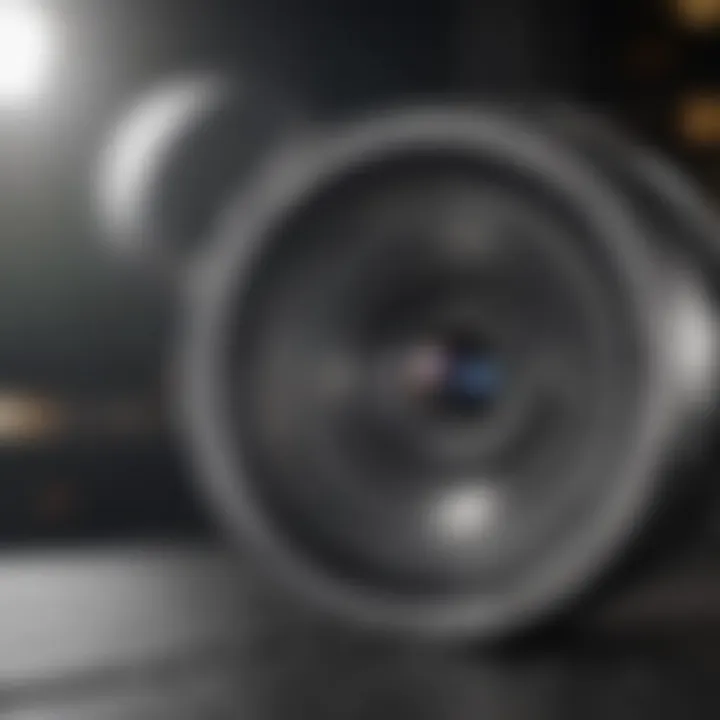
Post-processing is a crucial aspect in the production of titanium parts using electron beam melting (EBM). After the initial fabrication process, the parts often exhibit a range of physical characteristics that may not meet the desired specifications for specific applications. The post-processing phase aims to refine these properties to achieve the final product suitable for industrial use. The two primary focus areas of post-processing include heat treatment and surface finishing techniques. Both elements significantly impact the overall performance and reliability of EBM-fabricated titanium parts.
Heat Treatment
Heat treatment serves several purposes in post-processing EBM titanium structures. The EBM process typically results in complex microstructures within the titanium, affected significantly by build parameters. By implementing heat treatment protocols, one can tailor mechanical properties such as strength, ductility, and toughness.
There are various heat treatment methods available, including solution treatment, aging, and annealing. Each method targets specific material characteristics:
- Solution Treatment: This process involves heating titanium to an elevated temperature to dissolve phase constituents. The titanium is then rapidly cooled, which allows for a homogenous microstructure.
- Aging: Following solution treatment, aging is performed to enhance strength by allowing unwanted phases to precipitate out of the solid solution. This step optimizes mechanical properties while ensuring material stability.
- Annealing: This method reduces residual stresses in the titanium parts. Minimizing stress is vital, especially in applications where fatigue resistance is critical.
Surface Finishing Techniques
Surface finishing plays a pivotal role post EBM, as the surface integrity of titanium parts is critical for performance, particularly in highly corrosive or wear-intensive applications. The surface characteristics, such as roughness and porosity, can directly affect the mechanical performance and longevity of titanium components.
Several surface finishing techniques have emerged as effective processes to enhance the quality of EBM components:
- Mechanical Finishing: Techniques such as grinding, polishing, and shot peening can remove surface imperfections and improve surface smoothness.
- Electropolishing: This electrochemical process not only smoothens the surface but also enhances the corrosion resistance by removing defects and contaminants from the surface.
- Coating: Applying coatings can significantly enhance the wear resistance and can be tailored to meet specific environmental challenges. Options include ceramic coatings and metallic overlays.
In summary, applying appropriate surface finishing techniques is crucial in maximizing the performance and durability of EBM-fabricated titanium parts. Overall, both heat treatment and surface finishing represent two essential stages of post-processing, ensuring the realization of titanium parts that meet specific industrial requirements.
Mechanical Properties of EBM-Fabricated Titanium
Understanding the mechanical properties of titanium components produced through Electron Beam Melting (EBM) is crucial for many applications. These properties determine the material's performance under different conditions. EBM is known for its ability to produce parts with superior characteristics, which can enhance their usability in demanding industries like aerospace and medical technology.
The mechanical properties significantly affect how titanium behaves under stress, its longevity, and its performance in real-world situations. Analyzing these attributes provides insights relevant to engineers and manufacturers who rely on EBM for high-quality parts.
Tensile Strength
Tensile strength refers to the maximum amount of tensile stretching force a material can withstand before breaking. In the context of EBM-fabricated titanium, tensile strength is vital. Research indicates that EBM titanium generally exhibits higher tensile strength compared to other additive manufacturing methods. This strength translates to better load-bearing capabilities, which is essential in engineering applications.
A key factor influencing tensile strength is the layer-by-layer build of EBM. The controlled heating and cooling processes during this method lead to refined microstructures in the titanium. This refined structure can result in a desirable balance of strength and ductility, making it particularly suitable for critical components.
Fatigue Resistance
Fatigue resistance defines a material's ability to withstand cyclic loading over time. This property is important for components used in environments where they undergo repeated stress. Titanium made through EBM often shows excellent fatigue resistance due to the relatively defect-free nature of the parts produced.
The uniform microstructural properties resulting from the EBM process play a crucial role. Parts fabricated through this method can endure high cycle counts without significant degradation. Such characteristics make EBM titanium particularly attractive for aerospace and automotive industries, where parts experience cyclical stress.
Corrosion Resistance
Corrosion resistance is another pivotal mechanical property of titanium. This characteristic is especially critical in applications involving harsh environments, such as marine or chemical processing. Titanium is well-known for its natural resistance to corrosion. The EBM process can enhance this property by creating a dense and homogeneous microstructure that limits the pathways for corrosive agents.
Furthermore, the controlled atmosphere of the EBM process minimizes contamination during fabrication, which can further improve corrosion performance. As such, EBM-fabricated titanium is often employed in medical implants and aerospace applications, where longevity and reliability in corrosive environments are non-negotiable.
In summary, the mechanical properties of EBM-fabricated titanium, including tensile strength, fatigue resistance, and corrosion resistance, contribute to its desirable performance in various industries. These properties set EBM apart from traditional manufacturing methods, solidifying titanium's role in advanced applications.
Recent Advances in Electron Beam Melting Technology
The field of electron beam melting (EBM) has witnessed notable advancements in recent years. As industries push for more efficient and reliable manufacturing methods, understanding these developments becomes crucial. Recent advances have focused on enhancing both equipment design and process control, driving the technology toward greater precision and utility in titanium manufacturing.
Innovations in Equipment Design
Modern EBM systems have undergone significant upgrades in their design. These innovations prioritize not just performance, but also user experience and safety. One major improvement is the integration of real-time monitoring systems that allow operators to oversee the melting process closely. This capability enables immediate adjustments, minimizing defects in the finished titanium products.
Moreover, advancements in electron beam technology have led to the creation of more compact and powerful electron guns. These upgrades allow for better beam focus and increased energy density, which ultimately improves melting rates and material quality. New materials for the build plates, designed to better withstand the high temperatures involved, are also a key innovation. As equipment becomes more sophisticated, the potential for intricate geometries and complex part production grows.
Improvements in Process Control
Alongside the hardware innovations, process control in EBM technology has made leaps forward. Advanced algorithms and automated feedback systems have been developed to manage the melting process more effectively. These systems can analyze data from previous runs to optimize subsequent iterations, ensuring consistent quality in titanium parts. By fine-tuning parameters like beam current and scanning speed, manufacturers can achieve specific material properties tailored to their needs.
Furthermore, the implementation of artificial intelligence has provided another layer of sophistication. AI systems can predict material behavior in real-time, leading to proactive adjustments during the EBM process. This capability reduces waste and enhances the overall efficiency of titanium manufacturing. By understanding how different variables interact, manufacturers can achieve not just better mechanical properties but also reduce time and resources spent on post-processing.
Advancements in EBM technology not only enhance the manufacturing process but also drive material innovation, leading to new applications and possibilities in various industries.
In summary, the recent advances in EBM technology are transforming the landscape of titanium manufacturing. Innovations in equipment design lead to enhanced functionality, while improvements in process control drive operational efficiency. As these technologies continue to develop, they promise to reshape the future of additive manufacturing.
Future Prospects of Electron Beam Melting in Titanium Manufacturing
The future of Electron Beam Melting in titanium manufacturing holds significant promise due to continuous innovations in technology and increasing demand across multiple industries. As industries seek more efficient and sustainable manufacturing methods, EBM stands out as a compelling option. Its ability to create complex geometries while minimizing material waste enhances its appeal.
One major factor influencing the future prospects of EBM is the growing market for titanium components. The aerospace sector, in particular, demands high-performance materials that can withstand extreme conditions while maintaining lightweight characteristics. Similarly, the medical device industry is accumulating interest in titanium's biocompatibility, driving the need for advanced production methods. EBM's ability to produce intricate shapes and fine details aligns well with these market needs, creating opportunities for increased adoption.
Moreover, advancements in automation and software tools present avenues for improving the efficiency of the EBM process. Enhanced software for process control can help minimize human error and optimize production cycles. As these tools evolve, they will likely streamline operations and reduce lead times, which is crucial in competitive markets.
"The potential for EBM technology goes beyond existing applications, opening new avenues for innovation in material science and engineering."
Market Trends and Demand
The current trends showcase a strong upward trajectory in demand for titanium components produced via Electron Beam Melting. Industries are increasingly recognizing the benefits of EBM for producing lightweight yet strong parts necessary for advanced applications. The rise in passenger air traffic fuels the aerospace industry's growth, leading to heightened requirements for durable and efficient materials. Consequently, manufacturers are investing in EBM technologies to meet these demands.
In terms of regional markets, areas like North America and Europe are leading in EBM adoption, primarily driven by the aerospace and medical sectors. The adoption rates in emerging markets also indicate a rising interest in additive manufacturing. Factors such as increased investment in research and development, coupled with a focus on sustainability, contribute to this trend.
Potential Research Directions

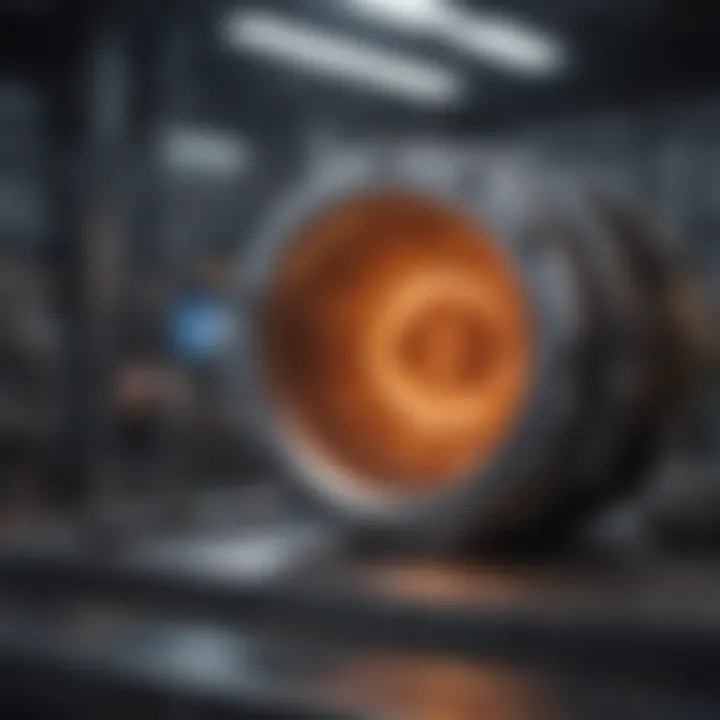
Looking ahead, several promising research directions could significantly enhance EBM technology's effectiveness and versatility. First, developing new titanium alloys tailored for EBM can pave the way for improved mechanical properties while addressing specific application challenges. Additionally, exploring innovative techniques such as multi-material EBM could open fresh possibilities in design and application.
Another valuable area for research involves optimizing the process parameters to refine the melting and cooling stages. Achieving better control over the thermal profile during fabrication can lead to enhanced microstructural properties, directly affecting the performance of the final components.
Investments in experimental studies that assess the interactions between the electron beam and titanium at various conditions could yield important insights. Understanding these interactions more deeply will contribute to improved reliability and consistency in EBM-produced components.
As the technological landscape continues to evolve, the future for Electron Beam Melting in titanium manufacturing indeed appears bright. The trajectory of market growth combined with innovative research and ongoing technological advancements suggests a transformative potential in the field.
Environmental Considerations in EBM
Understanding the environmental implications of electron beam melting (EBM) is crucial. This awareness aids in crafting manufacturing processes that align with sustainability goals. EBM, being an advanced manufacturing technique, presents opportunities as well as challenges for minimizing ecological footprints. The following subsections delve into two pivotal aspects of environmental considerations: energy consumption and waste management strategies.
Energy Consumption
Energy efficiency is a fundamental concern in the sector of additive manufacturing, and EBM is no exception. The EBM process operates in a vacuum, which conserves the energy output significantly compared to traditional melting processes. However, the initial energy input for generating the electron beam is substantial. It is imperative to balance the energy requirement against the benefits realized from the efficiency of the final product.
Several factors contribute to energy consumption in EBM:
- Vacuum maintenance: Maintaining the vacuum necessary for effective operation requires continuous energy, impacting overall energy costs.
- Beam generation: The electron beam must be generated and controlled accurately, requiring considerable energy input upfront.
- Process optimization: Advances in controlling the beam and optimizing build parameters can significantly reduce energy use.
Implementing energy-efficient technologies and practices is essential. For instance, using renewable energy sources for the EBM system can mitigate the carbon footprint, aligning production with global sustainability initiatives.
Waste Management Strategies
Managing waste in the EBM process is pivotal to ensuring environmental responsibility. The EBM method inherently produces less waste than many traditional melting techniques. This reduction is largely due to its layer-by-layer additive nature, which allows for more precise material usage. However, there are still particular waste management strategies to consider and implement:
- Recycling metal powder: Unused titanium powder can be collected and reused in subsequent builds. This not only minimizes waste but also lowers raw material costs.
- Material recovery systems: Implementing systems for extracting and recycling residual powder efficiently is crucial for reducing environmental impact.
- Environmental regulations compliance: Adhering to pertinent waste disposal regulations can help in maintaining responsibility towards the environment.
The proper execution of waste management strategies can transform EBM into a more sustainable manufacturing choice.
"Sustainable practices in manufacturing not only contribute to environmental preservation but enhance the reputation of a company in the market."
Comparative Analysis with Other Additive Manufacturing Techniques
A comparative analysis of additive manufacturing techniques is crucial for understanding the unique positioning and capability of Electron Beam Melting (EBM) in the field of titanium production. This analysis not only highlights the advantages and challenges of EBM but also places it within the broader spectrum of additive manufacturing technologies. By assessing other techniques, one can discern specific elements, benefits, and considerations that influence material selection, production efficiency, and application suitability.
Selective Laser Melting
Selective Laser Melting (SLM) is one significant competitor to EBM. SLM employs a laser to melt and fuse metallic powder, layer by layer, to create parts with complex geometries. One of the key strengths of SLM is its ability to work with a diverse range of metal powders. This flexibility allows manufacturers to explore various alloys to optimize performance for specific applications. Additionally, because SLM can operate at lower temperatures than EBM, it reduces the risk of thermal stresses, which can lead to warping or other deformities in the final product.
However, SLM has its limitations. The process generally requires a larger amount of support structures, which can complicate post-processing. Moreover, SLM might produce parts with less density compared to those manufactured by EBM. This difference arises from the varying interaction mechanisms between the laser and the material, impacting the final mechanical properties.
In summary, SLM is an efficient method for producing detailed geometries with varied metal powders, but it faces challenges related to support structures and possibly lower density components.
Direct Metal Laser Sintering
Direct Metal Laser Sintering (DMLS) operates on principles similar to SLM. It utilizes a focused laser beam to selectively sinter powdered metal, binding it to create a solid structure. One notable characteristic of DMLS is its quicker build times compared to EBM due to the faster scanning speeds of lasers. DMLS also allows for intricate designs which can enhance product functionality, especially in dynamic load-bearing applications.
Despite its advantages, DMLS shares some drawbacks with SLM, such as the tendency to create residual stresses due to rapid thermal cycling, which can compromise part integrity. Additionally, the variability in powder grades can affect the final quality of the manufactured part, making consistency a concern in some cases.
Furthermore, the fineness of the powder in DMLS can also lead to some peculiarities in the finish quality of parts, where a rougher surface texture might present issues in certain applications.
The comparative landscape of additive manufacturing brings to light critical insights that guide the selection of processes based on desired outcomes, mechanical properties, and economic factors.
Ultimately, in understanding EBM's position, one sees how it uniquely leverages the properties of titanium, making it highly relevant in fields such as aerospace and medical applications where precision and material integrity are paramount.
Finale
In summation, the exploration of Electron Beam Melting (EBM) of titanium showcases the technology's transformative potential in advanced manufacturing. The significance of this process cannot be understated as it merges precision with efficiency in a unique manner. The benefits of EBM are notable, including the production of complex geometries, reduced material waste, and enhanced mechanical properties of titanium components.
The multifaceted nature of EBM extends beyond mere functionality. It poses opportunities for innovation in several sectors, particularly aerospace, medical devices, and automotive industries. Each sector gains from the tailored properties of titanium that EBM can provide, which ultimately contributes to more sustainable practices in manufacturing.
However, challenges remain. Technical constraints and financial considerations must be addressed for broader adoption. The requirement for specialized equipment and high levels of expertise can limit accessibility to EBM processes. Despite these challenges, the ongoing innovation in equipment design and process control highlights a promising trajectory for EBM technology.
As we look toward the future, the alliance between EBM technology and titanium production appears set to deepen. Unexpected advancements may emerge, fueling further growth and application within diverse industries.
Overall, the insights shared in this article emphasize that understanding EBM is crucial for professionals seeking to navigate the complexities of modern manufacturing involving titanium.
Summary of Key Points
- Electron Beam Melting is a critical technology for titanium manufacturing, allowing for high precision and complex geometries.
- The advantages include reduced material waste and improved mechanical properties.
- Key applications span industries like aerospace, medical devices, and automotive, highlighting its versatility.
- Current challenges involve technical constraints and financial considerations.
- Future developments promise exciting advancements and potential growth in EBM applications.
Final Thoughts on EBM and Titanium
Electron Beam Melting stands at the intersection of technology and material science, specifically in titanium production. As industries increasingly demand high-performance materials, advanced techniques like EBM become essential. The ongoing evolution in the field signals a robust future marked by increased efficiency and innovation.
The dynamic relationship between EBM technology and titanium will likely drive future research and development. It encourages a thorough understanding of the process among engineers and researchers, fostering a collaborative effort to address existing hurdles. EBM is not just a method; it is a step towards a more advanced, capable, and eco-friendly manufacturing environment.
Importance of Key Sources
Moreover, the selection of references reflects the breadth and depth of research undertaken. Citing a variety of high-quality sources—from peer-reviewed journals to authoritative books—demonstrates a comprehensive understanding of the field. Readers gain insight into:
- The evolution of EBM technology and its adaptations.
- Recent advancements and innovations, highlighting ongoing developments.
- Applications across different industries, showcasing real-world relevance.
"A well-structured reference section not only enhances credibility but also sparks curiosity for further reading and investigation."
Key Aspects to Consider
When compiling references for an article of this nature, it is important to focus on several elements:
- Variety of Sources: Include academic journals, industry reports, and relevant websites to provide a well-rounded perspective.
- Recency of Publications: Emphasize recent studies to reflect the latest advancements in technology.
- Reputable Publishers: Select sources from established publishers to ensure the reliability of the information.