Welding of Ceramics: An In-Depth Examination
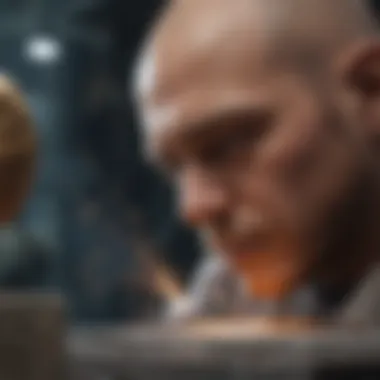
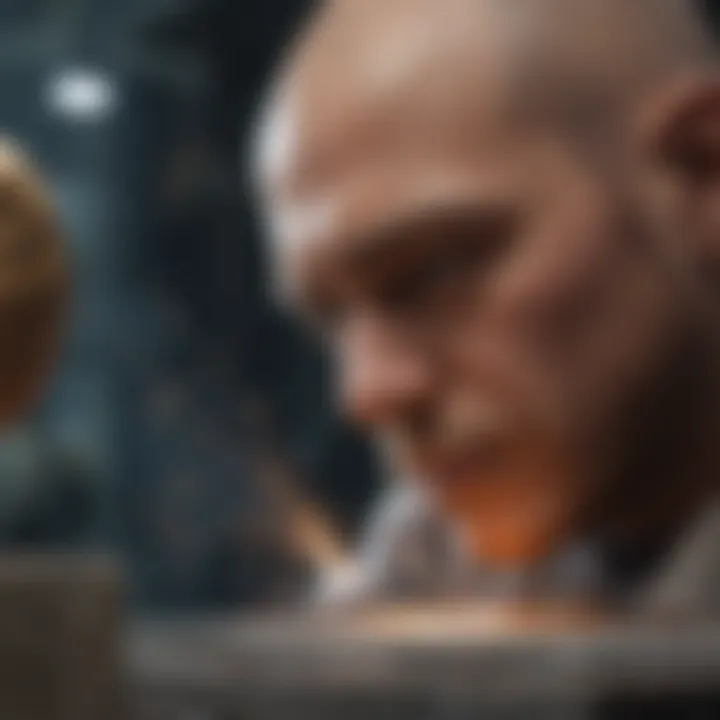
Intro
The welding of ceramics is a fascinating yet complex subject that intertwines principles from materials science and engineering. As industries increasingly seek advanced materials capable of withstanding extreme conditions, ceramic welding emerges as a critical field that addresses these needs. This article aims to explore the intricate process of welding ceramics, discussing essential methods, the challenges faced during the actual welding process, and the unique applications of welded ceramics in various industries.
The significance of ceramic welding cannot be overstated. With their exceptional hardness, thermal stability, and wear resistance, ceramics have become integral to fields such as aerospace, automotive, and electronics. By welding ceramics, manufacturers can create components that exhibit enhanced durability and performance, making the study of this topic particularly relevant for engineers and researchers alike.
Overview of Ceramic Welding
Ceramic welding represents a specialized area within material science and engineering, essential for advancing the production and functionality of ceramic components. This overview outlines its significance, exploring the intricate processes involved, the unique challenges, and the advantages it brings to various applications. Understanding these elements is vital for students, researchers, educators, and professionals working in relevant fields.
Definition and Concept
Ceramic welding encompasses the methods and techniques used to join ceramic materials through fusion. Unlike metals, ceramics exhibit unique properties such as high hardness but also high brittleness, which challenges conventional welding methods. The process typically requires precise techniques, including temperature control and suitable bonding agents, to achieve strong, durable joints. The primary goal is to maintain the integrity of the ceramic's mechanical and thermal properties while creating a reliable bond.
Historical Background
The journey of ceramic welding is intertwined with advancements in materials science. Historically, ceramics were primarily used in decorative and functional pottery. With the industrial revolution, engineers recognized the potential of ceramics in applications requiring high durability and heat resistance. Over time, researchers developed new welding techniques to enhance joint strength and reliability.
In the mid-20th century, innovations like laser welding and x-ray processing began to emerge, allowing for greater control over the welding environment. These developments marked a shift, as industries began to exploit ceramics extensively. Notably, the aerospace and biomedical sectors have propelled the need for advanced ceramic welding methods to create components that can withstand extreme conditions.
"Understanding the evolution of ceramic welding is essential for appreciating its current applications and future possibilities."
Material Characteristics of Ceramics
Understanding the material characteristics of ceramics is crucial in the context of welding. This knowledge not only informs the choice of suitable welding techniques but also dictates the strength, durability, and overall performance of the welded component. The distinct properties of ceramics, including mechanical, thermal, and chemical attributes, demand a specialized approach in welding processes.
Mechanical Properties
Ceramics are known for their high strength and stiffness, which come from their atomic structure. However, they also exhibit significant brittleness. This means that while they can withstand high loads under compression, they are prone to cracking under tension. This brittleness presents a significant challenge when it comes to welding, as any introduced stress can lead to fractures. Thus, it is essential to understand the mechanical properties in order to minimize these risks.
- High compressive strength, making them suitable for load-bearing applications
- Low tensile strength, requiring careful handling during fabrication
- Limited ductility, which affects how they can be joined to other materials
Thermal Properties
Ceramics are excellent insulators, which makes them suitable for high-temperature applications. They can endure extreme temperatures without deforming. However, thermal expansion coefficients vary among different ceramics. This difference can lead to thermal shock, especially when welding dissimilar materials. The welding process often generates localized heating, which can create stress from uneven expansion. Therefore, understanding thermal properties is vital for preventing damage.
- Ability to withstand high temperatures
- Lower thermal conductivity, requiring longer welding times
- Risk of thermal shock, necessitating controlled heat application
Chemical Resistance
One of the favorable attributes of ceramics is their chemical resistance. They typically resist corrosion and oxidation, extending their usability in aggressive environments. When welding ceramics, one must consider how various welding materials and methods may affect the chemical integrity of the ceramic itself. Certain welding techniques can introduce impurities that compromise this resistance.
- Resistant to chemical wear, making them ideal for industrial applications
- Compatibility issues during welding may affect overall performance
- Essential to select welding materials that do not introduce corrosive elements
Understanding the material characteristics of ceramics is essential for successful welding. It helps predict performance, enhances longevity, and ensures the integrity of welded joints.
In summary, the mechanical, thermal, and chemical characteristics of ceramics are foundational elements that influence welding outcomes. Each property presents its own set of challenges, but with proper knowledge and methods, successful welds can be achieved, thereby enhancing the application potential of ceramic materials in various industries.
Challenges in Welding Ceramics
The process of welding ceramics comes with a host of obstacles that require careful navigation. Understanding these challenges is crucial for anyone involved in ceramic welding, whether it be researchers, students, or industry professionals. Being aware of these difficulties allows for better planning and execution of welding processes. This section will cover key challenges including brittleness and fracture risk, thermal shock and stress, and the difficulties in joint design.
Brittleness and Fracture Risk
Ceramics are known for their brittleness. This property significantly impacts their performance during the welding process. The inherent fragility makes ceramics prone to fractures under stress. When subjected to welding heat, localized thermal stress can lead to structural failure if not managed appropriately. To mitigate fracture risks, precise temperature control is essential during the welding process.
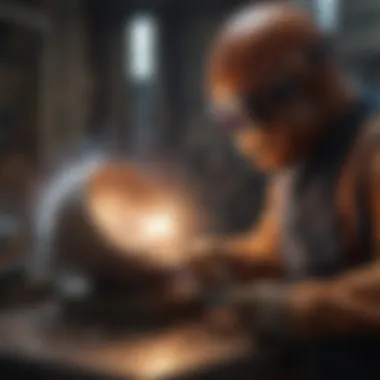
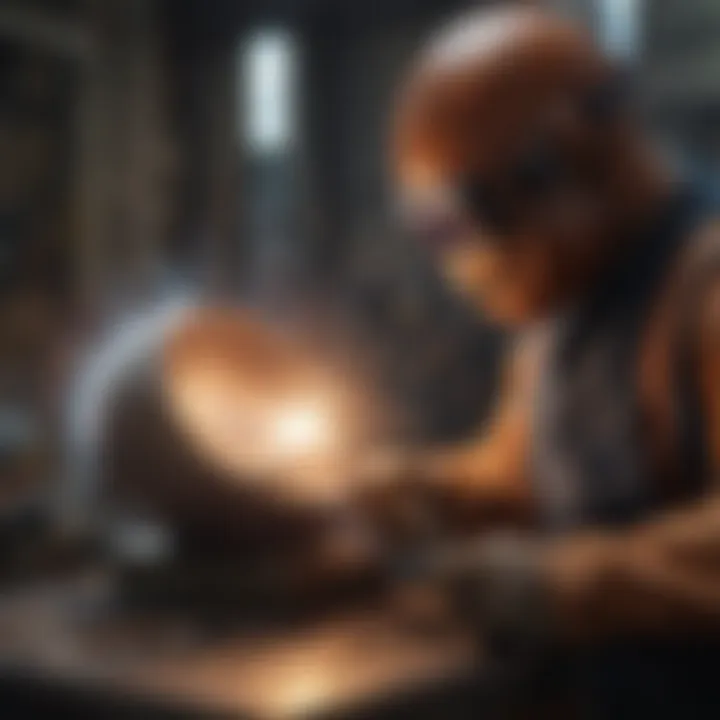
"Understanding material behavior under stress is vital in preventing fractures during ceramic welding."
Strategies can include gradual heating and cooling schedules which help in redistributing thermal stress more uniformly across the material. In addition, selecting the right filler material during welding can enhance toughness and improve overall joint integrity.
Thermal Shock and Stress
Thermal shock occurs when different temperatures in materials create stress, which can result in cracks. For ceramics, this is a significant concern. Rapid changes in temperature during welding can exacerbate pre-existing weaknesses in the materials. Therefore, it is necessary to consider the thermal properties of the ceramic being welded.
Techniques such as preheating the workpiece to reduce temperature gradients can help alleviate the risk of thermal shock. Continuous monitoring of temperature during welding is also advisable. This ensures more consistent results and preserves the material’s characteristics, thereby minimizing unwanted fractures.
Difficulties in Joint Design
An effective joint design is essential for successful welding of ceramics. However, traditional design methods often fail due to the unique properties of ceramics. The rigidity and brittleness of these materials limit the types of joints that can be used. This necessitates innovative approaches to create reliable joints, which often require a deep understanding of the material properties.
Moreover, the geometrical constraints of ceramic pieces can lead to complicated joint shapes that require advanced techniques for optimal alignment. Testing different joint configurations can be resource-intensive, making the design phase critical to the overall success of the welding operation.
In summary, the challenges in welding ceramics are multifaceted. Brittleness, thermal stresses, and design complexities demand innovative solutions and meticulous planning. Recognizing these challenges lays the groundwork for advancements in ceramic welding techniques, leading to successful applications in various industries.
Welding Methods for Ceramics
The welding of ceramics is not just a technical necessity but a cornerstone of modern manufacturing processes. Understanding different welding methods is essential for addressing specific needs in various applications. Each method has its own advantages, characteristics, and considerations that can influence the outcome of ceramic welding.
Direct Laser Welding
Direct laser welding is a highly precise method for joining ceramics. This technique uses focused laser beams to melt the edges of the ceramic parts being joined. The highly localized heat allows for minimal thermal impact, thus reducing the risk of damaging the surrounding material. One important advantage of direct laser welding is its ability to achieve high-quality welds with very fine tolerance. Moreover, this method supports automation, making it suitable for mass production.
Electron Beam Welding
Electron beam welding (EBW) employs a high-energy electron beam to create welds between ceramic components. This method is performed in a vacuum, which prevents contamination from air and other elements. EBW provides several benefits, including exceptional depth of penetration and the ability to weld thick materials. The precision it offers is advantageous for applications requiring intricate designs. However, the setup for electron beam welding can be expensive and complex.
Plasma Arc Welding
In plasma arc welding (PAW), an electrical arc generated between an electrode and workpiece creates a plasma jet that reaches extremely high temperatures. This enables the process to melt ceramics more effectively than other methods. Plasma arc welding is versatile and can handle various ceramics with different melting points. However, it requires careful control of the plasma parameters to prevent overheating or cracking during the welding process.
Traditional Methods
Traditional welding methods, like sintering and brazing, have their place in ceramic welding. Sintering involves heating the ceramic powder until it starts to fuse without reaching the melting point. Brazing, on the other hand, uses a filler metal to bond materials at a lower temperature than their melting point. While these methods may not be as high-tech as laser or electron beam welding, they can be effective for specific applications where high precision is not the primary goal.
Choosing the right welding method depends on a variety of factors including the material properties, design requirements, and production environments. Each method brings its own set of strengths and weaknesses that need to be carefully evaluated.
Innovative Techniques in Ceramic Welding
Innovative techniques are transforming the landscape of ceramic welding, making it more efficient and versatile. In this section, we will explore two significant advances: hybrid welding approaches and additive manufacturing integration. These methods address various challenges posed by traditional welding techniques and enhance the possibilities in ceramic applications.
Hybrid Welding Approaches
Hybrid welding combines two or more welding technologies to take advantage of their strengths. This approach can lead to better joint quality and improved mechanical properties. For ceramic welding, a hybrid method often merges laser welding with other techniques, such as traditional arc welding or electron beam welding.
This innovation is crucial because ceramics are notorious for their brittleness, making the welding process more challenging. By using hybrid processes, manufacturers can control heat input more precisely, reducing the likelihood of cracking and ensuring stronger joints. The potential for tailored microstructures in welded ceramics becomes achievable, contributing to better performance in demanding applications.
Considerations for implementation include the need for specialized equipment that can support multiple welding methods. Training for operators is also important to ensure that the nuances of each technology are understood and leveraged effectively. Overall, hybrid welding approaches represent a significant step forward in ceramic welding, allowing for greater flexibility and improved outcomes.
Additive Manufacturing Integration
Additive manufacturing, often known as 3D printing, is making its mark in the field of ceramic welding as well. This technique allows for the layer-by-layer construction of complex structures, which can be critical in sectors that require custom components, such as aerospace and biomedical devices. Integrating additive manufacturing with ceramic welding opens new doors for design and functionality.
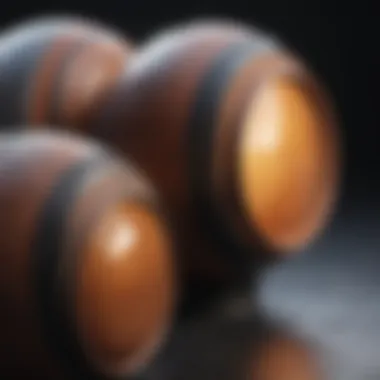
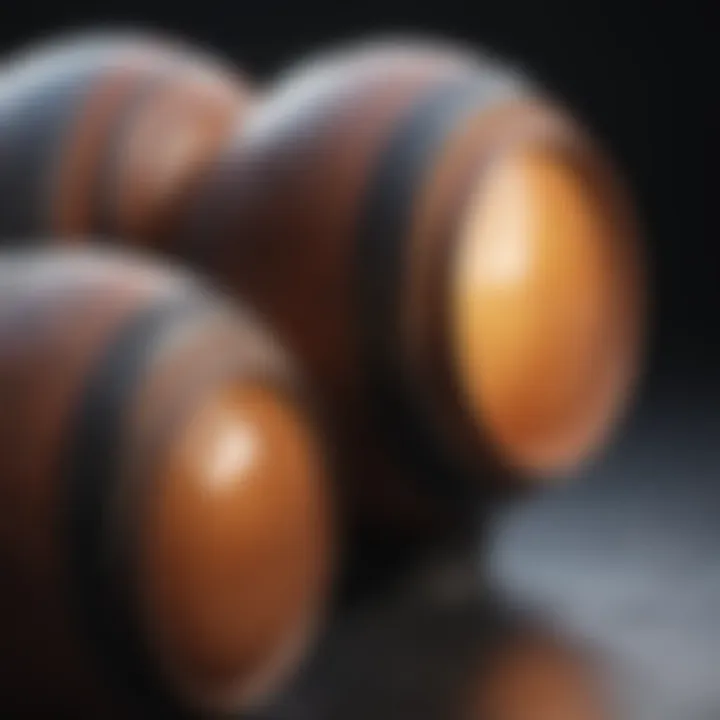
This technique allows for the creation of intricate ceramic components that traditional processes may not achieve. By printing ceramic materials and then welding them, engineers can achieve both precision and desired material properties. One benefit is the potential reduction in waste, as materials are only applied where needed. Additionally, this integration can lead to shorter lead times in production.
However, there are challenges as well. The compatibility of materials must be carefully managed to ensure successful bonding. Additive manufacturing also requires thorough understanding and optimization to avoid defects during the welding process.
"The integration of additive manufacturing with ceramic welding can revolutionize the way we design and produce complex ceramic parts, leading to enhancements in product performance and sustainability."
Properties of Welded Ceramics
The properties of welded ceramics play a crucial role in understanding their utility and performance in various applications. When different ceramic materials are welded together, the resulting joints must meet specific requirements to ensure functionality and durability. The study of these properties informs engineers about the suitability of certain welding methods for particular systems. In this context, we will explore three fundamental aspects of welded ceramics: mechanical integrity, thermal stability, and surface morphology. Each of these elements contributes uniquely to the overall effectiveness of ceramic components in real-world applications.
Mechanical Integrity
Mechanical integrity refers to the ability of welded ceramics to withstand applied forces without failing. This property is essential for the performance of ceramics used in load-bearing applications.
Welded joints must exhibit sufficient strength to resist stresses that occur during service. Factors affecting mechanical integrity include:
- Welding Technique: Different welding methods produce varying bond qualities. Techniques like electron beam welding often yield stronger joints than traditional methods.
- Material Compatibility: The types of ceramics combined influence integrity. Certain materials bond better than others due to differences in thermal expansion coefficients.
- Defects in Welds: Porosity, cracks, and inclusions can compromise joint strength. Quality control during the welding process is vital to minimize such defects.
In applications like aerospace or biomedical fields, failure of welded ceramics can lead to catastrophic results, which makes understanding mechanical integrity essential.
Thermal Stability
Thermal stability is another critical property of welded ceramics. It refers to the ability of a material to maintain its properties under temperature variations. Many ceramics are subjected to extreme heat in applications such as heat exchangers and turbine components.
Factors influencing thermal stability include:
- Thermal Conductivity: Materials with high thermal conductivity can lead to better heat dissipation, reducing thermal stress on welds.
- Thermal Expansion Mismatch: Differences in expansion rates between welded ceramics can cause joints to weaken under heating or cooling cycles.
- Phase Changes: Certain ceramics can undergo phase transformations at specific temperatures, affecting stability.
A thorough understanding of thermal stability aids in designing ceramic components that can perform reliably under expected operating conditions.
Surface Morphology
Surface morphology of welded ceramics plays a significant role in overall performance. This term encompasses the texture and topographical features of the welded joint. The surface characteristics can affect adhesion, corrosion resistance, and wear properties.
Considerations include:
- Surface Roughness: A rough weld surface may provide better mechanical interlocking with coatings or adjoining materials. However, excessive roughness might also lead to stress concentration points.
- Chemical Composition at the Surface: The presence of contaminants or oxides can alter the chemical interactions of ceramics with their environment, impacting durability.
- Porosity and Defects: The surface's porosity can affect its resistance to environmental factors such as erosion or corrosion.
Understanding the surface morphology is essential for optimizing the adhesion properties of coatings applied to welded ceramics.
Applications of Welded Ceramics
The applications of welded ceramics highlight the technological advancements and utility of ceramic welding in various industries. Understanding these applications provides insights into how welded ceramics meet the specific requirements of quality, performance, and safety. The introduction of welded ceramics opens avenues for innovative designs, particularly in sectors where high-performance materials are essential. The advantages of using welded ceramics include enhanced durability, lightweight structures, and resistance to extreme conditions. This versatility not only makes them attractive for manufacturers but also pushes the boundaries of what's possible in engineering and product design.
Aerospace Industry
The aerospace industry is one of the primary domains that benefit from welded ceramics. High-performance materials are crucial for aircraft components, as they must withstand harsh operating conditions, such as high temperatures and aggressive environments. Welded ceramic materials, such as alumina and zirconia, offer needed resistance.
The integration of welded ceramics in aerospace applications can lead to significant weight reductions. For instance, turbine blades manufactured from welded ceramics can enhance fuel efficiency and overall performance. Additionally, these materials are less prone to corrosion, which prevents the degradation that can occur with metals under similar conditions.
"In aerospace, every gram saved can lead to improved performance and lower costs."
Applications in structures like heat shields and thermal barriers also showcase the thermal stability of welded ceramics. This capability is essential for parts that are directly exposed to extreme heat during flight.
Biomedical Applications
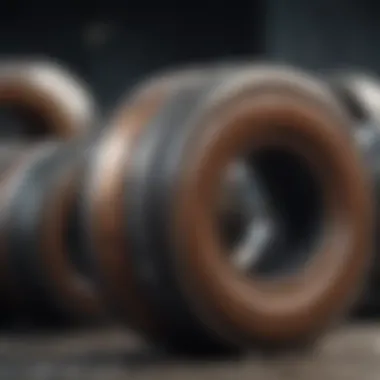
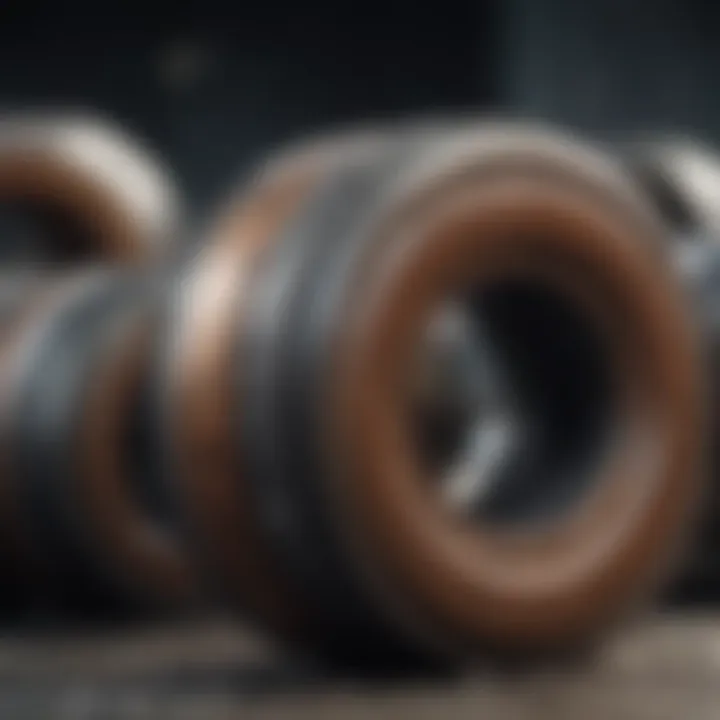
In the biomedical sector, welded ceramics serve as critical materials for implants and prosthetics. Their biocompatibility ensures that they do not provoke adverse reactions in the body. This property is essential for dental and orthopedic implants, where reliability and safety are paramount.
Welded ceramics can also improve the longevity of medical devices. Their hardness and wear resistance contribute to better performance in demanding environments. For instance, orthopedic implants made from welded ceramics can offer enhanced wear resistance compared to traditional metal implants.
Moreover, due to values like corrosion resistance, welded ceramics are ideal for surgical tools and equipment. Instruments that require high precision benefit from the rigid and stable characteristics of welded ceramics, which can maintain their sharpness and performance over time.
Electronics and Insulation
Within the electronics sector, welded ceramics are utilized primarily for insulative components. They help ensure reliability in electronic circuits by offering excellent dielectric properties. This quality makes them suitable for capacitors, insulators, and substrates in various electronic devices.
The ability to withstand high temperatures without sacrificing performance allows welded ceramics to be employed in components used in harsh environments. This is particularly advantageous in sectors like telecommunication and automotive electronics, where device performance is critical.
Additionally, welding techniques have allowed for the creation of complex shapes and designs in ceramic components. Customization enhances the functionality and effectiveness of electrical systems, leading to innovations in product design.
In summary, the diverse applications of welded ceramics underline their importance in several industries. Their unique characteristics make them suitable for specialized uses, highlighting the significance of ongoing research and development in ceramic welding.
Future Trends in Ceramic Welding
The field of ceramic welding is evolving rapidly. As technology advances, new trends are shaping the future of how ceramics are manufactured and welded. This section will explore key elements driving these future trends and their implications for industries that utilize ceramic components. By understanding these trends, stakeholders can make informed decisions that align with both technological advancements and marketplace demands.
Materials Innovation
Materials innovation is at the forefront of progress in ceramic welding. Researchers and engineers are developing advanced ceramics that possess improved mechanical and thermal properties. These innovations often focus on enhancing toughness and reducing brittleness. Examples include the use of doped zirconia and silicon carbide, which exhibit superior performance in high-stress environments.
Such improvements can lead to:
- Increased Lifespan: Greater durability means that components can withstand more wear and tear, reducing replacement costs.
- Wider Application Range: New ceramic materials can be tailored for specific applications, expanding their usability in various industries.
- Enhanced Performance: Higher thermal shock resistance translates to improved safety and efficiency in applications like aerospace or medical devices.
Sustainable Practices
Sustainability is becoming increasingly important in all manufacturing processes, and ceramic welding is no exception. The future of ceramic welding must consider environmental impact. Implementing sustainable practices involves not only the use of eco-friendly materials but also energy-efficient processes.
Some key sustainable practices include:
- Recycling of Waste Materials: Utilizing scrap ceramics in new welding applications can conserve resources and reduce waste.
- Energy Efficiency: Focusing on energy-efficient welding techniques, such as laser or electron beam welding, can minimize the environmental footprint.
- Life Cycle Analysis: Regular assessment of product life cycles to maximize efficiency during production and usage stages is essential.
Industry Collaborations
Collaborative efforts among industries, academia, and research institutions are crucial for driving innovation in ceramic welding. Cross-disciplinary partnerships can yield fresh insights and foster significant advancements. These collaborations help combine material science with engineering, leading to novel solutions in welding techniques.
Benefits of such collaborations include:
- Knowledge Sharing: Development of best practices and sharing of critical insights among varying sectors can accelerate progress.
- Funding Opportunities: Joint ventures can attract funding from governmental and private organizations, allowing for expanded research and development.
- Access to Advanced Technologies: Collaboration enables access to cutting-edge technologies and equipment that individual entities may lack.
"Future trends in ceramic welding indicate a clear shift towards innovative materials, sustainable practices, and collaborative efforts that will shape the future of this field."
The End
The conclusion of this article is paramount as it encapsulates the significant elements discussed under the theme of ceramic welding. This multidisciplinary field combines knowledge of materials science, engineering, and manufacturing practices. Understanding the intricacies of welding ceramics extends beyond mere technique; it fosters innovation in various sectors, including aerospace and biomedical applications.
Summary of Key Insights
Throughout this exploration, several vital points emerged.
- Complexity of Welding Ceramics: The process is intricate due to the unique properties of ceramics, such as their brittleness and thermal sensitivity.
- Challenges: We navigated the numerous challenges faced in ceramic welding, including fracture risks and thermal stresses, making it clear that careful consideration is crucial in joint design.
- Welding Methods: From direct laser welding to traditional approaches, various techniques exist, each with specific benefits and limitations.
- Innovative Technologies: Emerging methods such as hybrid approaches and integration with additive manufacturing are leading the way forward, enhancing efficiency and quality in welded ceramics.
- Applications: The application of welded ceramics in industries emphasizes their versatility and potential for future advancements.
These insights solidify the understanding that ceramic welding is not just a technical skill but a foundational element in modern manufacturing that warrants ongoing research and development.
Final Thoughts on Research and Development
Future prospects in ceramic welding present exciting possibilities. Innovations in materials science will likely facilitate the discovery of new ceramic composites that are easier to weld and more durable. Sustainable practices are increasingly important, encouraging the development of methods that minimize waste and energy consumption during the welding process. Furthermore, industry collaborations could lead to breakthroughs, fostering an environment where knowledge exchange accelerates advancements.
As researchers and professionals continue to delve deeper into this field, the accumulated knowledge will inform better practices, ultimately refining the welding processes for ceramics. Continuous exploration and investment in research are essential to unlock the full potential of this significant area in material engineering.