Understanding Aluminium Oxidation: Processes and Impacts
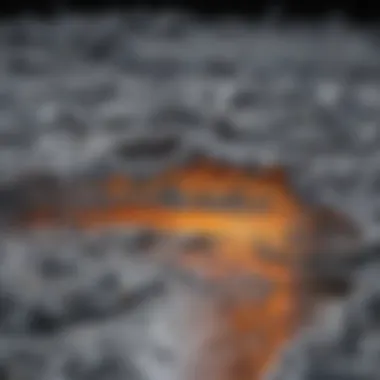

Intro
Aluminium oxidation is a critical subject in material science that addresses how aluminium interacts with oxygen. This process significantly affects both the physical properties of aluminium and its applications across numerous industries. Understanding these reactions helps in enhancing material durability, improving product design, and minimizing ecological impacts.
The relevance of aluminium oxidation is not limited to purely scientific exploration. Its implications are observed in fields such as engineering, manufacturing, and environmental studies. As industries increasingly rely on aluminium for its lightweight properties and resistance to corrosion, the mechanisms of its oxidation become vital knowledge.
In this overview, we explore various facets of aluminium oxidation, including the mechanisms involved, influencing factors, industrial applications, and environmental implications. Through this journey, readers will gain insight into both the complexities and practical outcomes of aluminium oxidation.
Fundamentals of Aluminium Oxidation
The fundamentals of aluminium oxidation are critical to understanding how aluminium interacts with its environment. This process not only affects the physical and chemical properties of aluminium but also has implications in various industrial applications and environmental considerations. A deep understanding of the basic principles can lead to better practices in manufacturing and maintenance, ultimately enhancing the performance and longevity of aluminium products. Moreover, recognizing how oxidation occurs can assist professionals in designing effective protective measures against deterioration.
Chemical Basis of Oxidation
The chemical basis of oxidation involves the reaction between aluminium atoms and oxygen molecules in the environment. When aluminium is exposed to oxygen, it tends to lose electronsโan essential aspect of oxidation. This reaction leads to the formation of aluminium oxide, which creates a protective layer that can shield the underlying metal from further degradation. The formation of this oxide layer is both beneficial and detrimental; while it provides a barrier against corrosion, it can also lead to issues in certain applications where bond strength is needed.
In more detail, the oxidation reaction can be expressed as follows:
[ ext4Al + ext3O_2 ightarrow ext2Al_2 extO_3 ]
This equation describes how four atoms of aluminium react with three molecules of oxygen to form two molecules of aluminium oxide. The aluminium oxide that forms is typically more stable than the metallic form of aluminium, thus giving it a certain level of resilience. Furthermore, this oxide layer tends to develop quickly; however, its effectiveness is influenced by several factors, including the composition of the atmosphere and the surface condition of the aluminium.
Electrochemical Mechanisms
Electrochemical mechanisms further elucidate the complexities of aluminium oxidation. When aluminium undergoes oxidation in the presence of moisture, it can participate in electrochemical corrosion processes. Here, aluminium acts as an anode and oxygen as a cathode in a galvanic cell, leading to the generation of an electrical current.
The corrosion can be influenced by various factors:
- pH levels: Acidic or basic conditions can either accelerate or inhibit oxidation.
- Conductivity of environmental media: Saline environments often expedite the corrosion process, while pure water presents a lower risk.
- Presence of other metals: Certain dissimilar metals can create galvanic cells, making the aluminium more susceptible to corrosion.
Understanding these electrochemical processes is vital for improving corrosion resistance technologies. Controlled studies can help in identifying optimal conditions that reduce the rate of oxidation while maintaining the beneficial properties of aluminium. By recognizing the specific electrochemical pathways, researchers and engineers can develop better alloys and surface treatments that enhance performance and durability.
Thermodynamic Factors
Thermodynamic factors play a crucial role in understanding the oxidation of aluminium. They help to elucidate the conditions under which aluminium reacts with oxygen. A solid grasp of these factors can yield insights into how to control the oxidation process. This, in turn, can lead to improved application and longevity of aluminium products.
Standard Electrode Potentials
Standard electrode potentials are vital in predicting the feasibility of the oxidation reactions involving aluminium. The more negative the electrode potential, the more prone a metal is to oxidation. For aluminium, the standard electrode potential is about -1.66 V. This means that when aluminium is in contact with moisture and oxygen, it has a high tendency to oxidize. This potential can vary based on the composition of the environment surrounding the aluminium. Environmental factors can include solution concentration, pH levels, and presence of other ions.
Furthermore, the standard electrode potentials are used to compare the oxidation tendencies of several metals. By understanding these values, researchers can determine the likelihood of aluminium undergoing oxidation in different scenarios.
Temperature Effects on Oxidation Rates
Temperature is a significant factor that impacts the rate of aluminium oxidation. As temperature increases, the kinetic energy of the reacting molecules also increases. This can lead to enhanced reaction rates. Studies have shown that the rate of oxidation of aluminium accelerates with temperature.
In various experiments, it has been observed that at elevated temperatures, the formation of aluminium oxide layers becomes quicker. This layer of oxide can serve as a protective barrier, but it may also encourage further oxidation under certain conditions. Subsequent research suggests that higher temperatures can result in both beneficial and detrimental effects, depending on the required application.
- A few key considerations regarding temperature effects:
- Optimal temperature ranges must be maintained for desired material properties.
- High temperatures can lead to increased diffusion of oxygen to the aluminium surface.
- Balancing temperature with oxidation times can help in creating desired oxide layers.
To summarize, thermodynamic factors such as standard electrode potentials and temperature significantly influence the oxidation of aluminium. Understanding these elements allows for better manipulation of the oxidation process to achieve favorable outcomes in both industrial applications and environmental impacts.
Environmental Influences
The examination of environmental influences on aluminium oxidation is crucial to understanding both the mechanisms involved and the implications for practical applications. Aluminium, while known for its resistance to corrosion due to the formation of a protective oxide layer, can still be significantly impacted by environmental factors. This section will discuss how elements such as humidity, moisture, and atmospheric contaminants play roles in the oxidation process of aluminium, highlighting their significance and the need to consider these factors in both research and industrial settings.
Impact of Humidity and Moisture
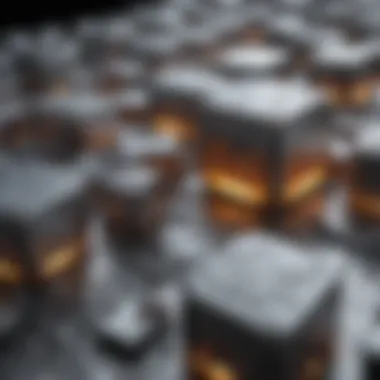

Humidity and moisture are two key environmental factors affecting the oxidation of aluminium. When aluminium is exposed to moisture in the air, it can lead to the formation of aluminium hydroxide, which subsequently converts to aluminium oxide upon drying. This process begins with the water molecules interacting with the metal surface, initiating a corrosion reaction that can compromise the integrity of the protective oxide layer. Increased humidity levels can accelerate this reaction, leading to faster rates of oxidation.
Research indicates that environments with high humidity can create conditions favorable for pitting corrosion, which can form localized areas of weakness within the metal. This is particularly concerning in industrial applications where structural integrity is paramount. Moreover, in coastal regions or areas with frequent rain, it is essential to monitor humidity levels to mitigate corrosion risks.
In summary, understanding the effects of humidity and moisture on aluminium oxidation is vital for industries that rely on aluminium components. Factors such as relative humidity percentages and exposure durations need careful consideration to prevent premature material degradation.
Effects of Atmospheric Contaminants
Atmospheric contaminants significantly influence aluminium oxidation. Various pollutants, including sulfur dioxide, nitrogen oxides, and chlorides, can exacerbate the oxidation process. These contaminants can react with the oxide layer on aluminium, leading to its breakdown and creating pathways for further corrosion.
For instance, in urban environments, the presence of acid rain can increase the rate of aluminium oxidation, as the acid reacts with the oxide layer. Similarly, chloride ions, often found in coastal air or as a product of industrial emissions, can cause rapid pitting and localized corrosion.
The impact of these contaminants cannot be understated. Industries should implement strategies to minimize exposure to harsh environmental conditions. Protective coatings and regular inspections are practices that can help combat the negative effects of atmospheric pollutants.
It is essential to recognize the role of environmental factors in aluminium oxidation to effectively manage the durability of aluminium products in diverse settings.
Oxidation Products and Their Properties
Understanding the oxidation products of aluminium is crucial for multiple reasons. First, these products govern the behaviour of aluminium in various environments. Second, they directly affect the material's applications in industries. Lastly, knowing these properties can lead to advancements in technology and sustainability practices. This section will cover the formation of aluminium oxide and the characteristics of alumina, summarizing their implications in various fields such as manufacturing and material science.
Formation of Aluminium Oxide
Aluminium oxidation primarily leads to the formation of aluminium oxide, commonly referred to as alumina. This process begins when aluminium interacts with oxygen in the presence of moisture and other environmental elements. The oxide layer that forms on the surface is typically a few nanometers thick. However, this thin layer plays a significant role in protecting the underlying metal from further corrosion.
The reaction for the formation of aluminium oxide can be expressed simply as:
Alumina forms through two main pathways: direct oxidation and the oxidation of pre-existing aluminium compounds. In direct oxidation, elemental aluminium reacts with oxygen to create Al2O3. This reaction occurs faster at higher temperatures, which is a critical consideration in industrial applications. Controlling the oxidation process is vital, as the properties of the formed alumina can vary significantly based on factors like temperature, pressure, and the presence of contaminants in the air.
Characteristics of Alumina
Alumina exhibits several unique characteristics that make it valuable across various applications. Some key properties include:
- Chemical Stability: Alumina is highly resistant to chemical reactions, which contributes to its use in harsh environments. This stability is beneficial in chemical processing industries.
- Mechanical Strength: Depending on its crystalline structure, alumina can be remarkably strong while remaining lightweight. This property is exploited in aerospace and automotive components.
- Thermal Resistance: Alumina can withstand high temperatures, making it suitable for insulating materials and refractory coatings.
- Electrical Insulation: Although pure alumina can conduct electricity at high temperatures, it is generally an excellent insulator. This makes it valuable in electronic applications.
In practical terms, the durability of alumina accentuates the longevity of aluminium products, especially in applications exposed to adverse weather conditions.
Utilizing the knowledge of alumina's characteristics can lead to innovative approaches in manufacturing processes. This understanding fosters developments in coating technologies that enhance corrosion resistance and material longevity, reducing waste and promoting sustainability.
A comprehensive grasp of aluminium oxidation products, especially alumina, informs both academic research and industrial practices. As technology progresses, the significance of these properties becomes increasingly apparent, opening avenues for future advancements.
Industrial Applications of Aluminium Oxidation
Aluminium oxidation presents significant industrial applications that leverage its unique properties. The oxidation process leads to the formation of aluminium oxide, which enhances the inherent qualities of aluminium, making it suitable for various applications. This section discusses the distinct roles that aluminium oxidation plays in material strengthening and corrosion resistance enhancements, highlighting its relevance in manufacturing and engineering sectors.
Role in Material Strengthening
Aluminium, when oxidized, forms a dense layer of aluminium oxide. This oxide layer increases the hardness of the surface, providing enhanced strength to the base material. Unlike many metals, aluminium benefits from this oxide layer because it does not peel off easily. Instead, it becomes part of the surface structure, offering greater abrasion resistance.
- Benefits of Strengthened Aluminium:
- Increased wear resistance
- Greater structural integrity
- Enhanced lifespan of components
In the aerospace and automotive industries, these features are crucial. The demand for lightweight but strong materials pushes engineers to select oxidized aluminium for components such as wing structures and engine parts. The improved strength-to-weight ratio allows for better fuel efficiency and overall performance.
Corrosion Resistance Enhancements
Corrosion poses a significant challenge for materials exposed to atmospheric conditions. Aluminium oxidation increases the corrosion resistance of the metal due to the protective oxide layer. This characteristic is vital in many applications where materials are subjected to harsh environments, such as marine or chemical processing settings.
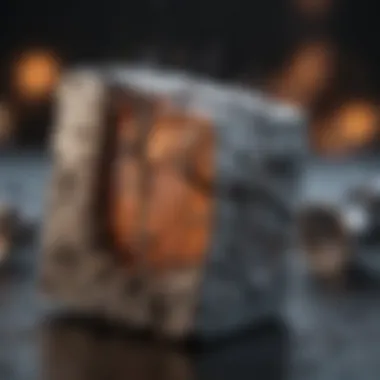

The protective oxide layer not only prevents further oxidation of the underlying aluminium but also acts as a barrier against moisture and contaminants.
- Key factors of corrosion resistance:
- Impermeable barrier against environmental factors
- Reduced maintenance costs
- Longevity of products
Manufacturers treat aluminium with processes like anodizing to enhance these properties further. Anodizing involves controlled oxidation, which thickens this protective layer. This technique is popular for architectural applications, including window frames and roofing, where durability and aesthetic attributes are essential.
In summary, the industrial applications of aluminium oxidation significantly contribute to material strengthening and corrosion resistance. These enhancements not only improve performance but also extend the usability of aluminium in various fields, highlighting its integral role in modern engineering.
Control Techniques for Aluminium Oxidation
Controlling aluminium oxidation is vital for maintaining its structural integrity and enhancing its lifespan. Oxidation inherently alters the material properties of aluminium, potentially compromising its utility in various applications. Hence, employing effective control techniques is essential to mitigate corrosion and oxidation-related issues. This section delves into the methods used to prevent or minimize aluminium oxidation, focusing on specific strategies such as preventive coatings and controlled atmosphere treatments.
Preventive Coatings
Preventive coatings serve as a primary line of defense against aluminium oxidation. These coatings act as barriers, preventing moisture and corrosive materials from coming into contact with the bare aluminium surface. Various types of coatings exist, each catering to different environmental conditions and application requirements.
Commonly used coatings include:
- Organic Coatings: These include paints and varnishes that provide good protection and aesthetic appeal. They often require periodic maintenance to replace worn or damaged layers.
- Inorganic Coatings: Materials like anodic oxide films offer robust protection due to their hardness and chemical stability. Anodizing involves an electrochemical process that enhances corrosion resistance while preserving electrical conductivity.
- Metallic Coatings: These can be applied through methods like hot-dip galvanizing or electroplating. Coatings with materials such as zinc or aluminum provide sacrificial protection, where the coating material corrodes preferentially, thus protecting the underlying metal.
When selecting a coating, considerations such as the intended use, environmental exposure, and the desired longevity are crucial. Effective application techniques also influence the performance of these coatings.
Controlled Atmosphere Treatments
Controlled atmosphere treatments are another significant approach to managing aluminium oxidation. These processes modify the environmental conditions surrounding the aluminium to reduce the likelihood of oxidation. By controlling the humidity, temperature, and presence of reactive agents, the rate of oxidation can be minimized.
Key techniques and processes include:
- Inert Gas Purging: In applications where aluminium components are fabricated or processed, purging the environment with inert gases like nitrogen prevents oxygen from reaching the surface.
- Humidity Control: Maintaining a low humidity level in storage or operational areas can significantly reduce oxidation risks. Dehumidifiers are often employed in sensitive environments.
- Temperature Optimization: Lowering the temperature during processing can decelerate oxidation rates, although care must be taken to ensure it does not adversely affect other material properties.
Implementing controlled atmosphere treatments requires an understanding of the specific conditions that contribute to oxidation in a given environment. By tailoring these approaches to match the challenges posed by the operating conditions, manufacturers can enhance the durability of aluminium products.
Efficient control of aluminium oxidation not only prolongs the material's service life but also enhances its performance across various applications. This is crucial as industries rely heavily on aluminium for its lightweight and corrosion-resistant properties.
In summary, both preventive coatings and controlled atmosphere treatments represent effective strategies for managing aluminium oxidation. It is essential to assess the specific design and operational requirements when determining the best technique to use. This careful consideration ensures optimal performance while minimizing the risks of degradation.
Ecological Considerations
The topic of ecological considerations regarding aluminium oxidation is essential within the broader context of material science and environmental studies. Understanding how aluminium oxidation affects the environment provides insights into ecological sustainability, manufacturing processes, and the lifecycle impact of aluminium products. The oxidation of aluminium not only reflects its chemical properties but also poses various environmental implications and necessitates an examination of sustainable practices in aluminium usage.
Impact of Aluminium Oxidation on the Environment
Aluminium oxidation generates aluminium oxide, which is generally considered non-toxic and inert. However, the environmental impact is more complex and should be examined through various lenses.
- Resource Extraction and Processing: The production of aluminium involves mining bauxite ore. This process can lead to significant ecological disruption, including deforestation, soil erosion, and biodiversity loss.
- Lifecycle Analysis: Aluminium products, after their useful life, can end up in landfills where they can undergo oxidation and react with various environmental factors.
- Ecosystem Impact: Aluminium can accumulate in some ecosystems, potentially impacting wildlife and plant life. Research indicates that elevated aluminium levels may affect plant growth and aquatic life, disrupting local ecosystems.
- Energy Consumption: The smelting process for aluminium is highly energy-intensive, contributing to greenhouse gas emissions.
- Waste Management: By-products from aluminium extraction, including red mud, pose disposal challenges that can contribute to land and water pollution.
- This can affect soil and water quality due to leaching of metals and other contaminants.
- Recycling rates for aluminium are relatively high, which can mitigate some environmental impacts, but awareness and proper recycling practices are crucial.
"One cannot separate the chemistry of aluminium oxidation from its ecological footprint; both are intertwined and crucial for informed decision-making in material usage."
Overall, while aluminium oxide itself might be harmless, the processes involved in aluminium extraction and use can pose serious environmental challenges that must be addressed.
Sustainable Practices in Aluminium Usage
Sustainability is imperative in the context of aluminium oxidation. To lessen ecological impacts, various practices can be adopted during different stages of aluminium's lifecycle:
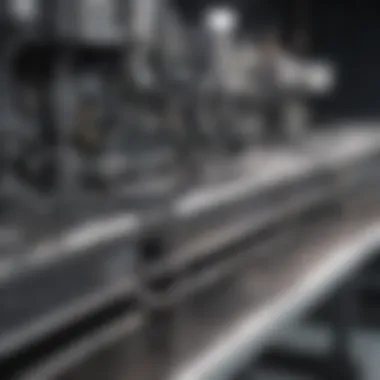

- Recycling: The most effective method to enhance sustainability is through aluminium recycling. Recycling aluminium requires only 5% of the energy needed for primary production.
- Eco-friendly Manufacturing Techniques: Technologies such as hydrometallurgy and electrolysis can reduce harmful emissions during production. Some modern smelting techniques use renewable energy sources, which can lower the carbon footprint.
- Innovative Coatings: Using sustainable coatings that do not leach harmful substances can protect aluminium surfaces from oxidation while having minimal environmental impact. Some companies develop eco-friendly alternatives that ensure longer product life.
- Biodegradable Products: Research into biodegradable alternatives or coatings can further lessen the ecological footprint. Sustainable products, when available, can be utilized in place of traditional aluminium coatings that contribute to pollution.
- Lifecycle Assessments: Conducting thorough assessments helps manufacturers to pinpoint environmental hazards related to aluminium production and use. This practice supports efforts in reducing energy consumption and waste production throughout the product's lifecycle.
Incorporating sustainable practices requires collective effort from manufacturers, consumers, and regulatory bodies. Addressing aluminium oxidation and promoting eco-friendliness is a shared responsibility that can lead to a significant positive change for the environment.
Future Research Directions
The field of aluminium oxidation is ever-evolving. As understanding grows, deeper exploration of this phenomenon is crucial. Future research directions will focus on new methodologies, materials, and the ecological impacts of aluminium oxidation. These studies will not just shed light on the fundamental aspects of oxidation but also enhance the application of aluminium in various industrial fields.
There are significant elements to consider for future research.
- Novel Coating Techniques: Development of advanced coatings to prevent unwanted oxidation.
- Real-Time Monitoring: Systems to analyze oxidation in real-time can help improve processes and extend the life of aluminium components.
- Understanding Alloy Behavior: Further studies should look at how different aluminium alloys behave under varying oxidation conditions.
Research in these areas will provide substantial benefits. Improved oxidation resistance can lead to better performance in applications ranging from aerospace to construction.
"Investing in research allows us to innovate and confront the challenges posed by aluminium oxidation effectively."
Moreover, innovations will enable industries to adapt and enhance sustainability practices. It will also pave a path for reducing environmental impacts associated with aluminium oxidation. Overall, solid attention on these areas will lead to significant advancements.
Advanced Analytical Techniques
The application of advanced analytical techniques is pivotal in the study of aluminium oxidation. These methods can offer insights that traditional techniques cannot match. For example, techniques like atomic force microscopy (AFM) can be used to observe the microscopic changes on the aluminium surface as oxidation occurs. This observation helps in understanding how surface roughness affects subsequent oxidation rates.
Another notable technique involves spectroscopy. Methods such as X-ray photoelectron spectroscopy (XPS) can evaluate the oxidation state of aluminium oxides and help identify their compositions. Recognizing the nature of these oxides is crucial because different oxidation states can influence both physical properties and chemical reactivity.
Benefits of Advanced Analytical Techniques:
- Precision Measurement: Enhanced accuracy in assessing alumina layers and their properties.
- Real-time Data Acquisition: Ability to monitor changes in oxidation instantaneously.
- Deeper Insights: Broader understanding of underlying oxidation mechanisms.
Future research will likely integrate these advanced analytical techniques to provide a clearer picture of aluminium oxidation on a molecular level.
Innovations in Aluminium Alloys
Innovations in aluminium alloys represent another key focus for future research. As industries seek stronger and lighter materials, new alloys with improved oxidation resistance are essential. Current research is directing attention on the alloying elements that can effectively enhance corrosion resistance.
For instance, the incorporation of elements like lithium and magnesium into aluminium alloys has shown prospective benefits. These elements can improve the mechanical properties while also contributing to enhanced resistance to oxidation. Furthermore, optimizing the processing methods, such as aluminum extrusion and rolling technologies, can yield alloys with fine microstructures that further resist oxidation.
Key Considerations for Alloy Innovations:
- Performance vs. Cost: Balancing enhanced performance with manufacturing costs.
- Mechanical Properties Analysis: Studying the impact of compositions on strength, ductility, and thermal stability.
- Long-term Behavior Studies: Understanding how alloys respond to prolonged exposure to oxidizing environments.
Summary and Endings
Understanding aluminium oxidation is essential for multiple reasons. It illuminates the fundamental processes that occur when aluminium interacts with oxygen in various environments. This interaction not only influences the durability of aluminium products but also determines the structural integrity required for industrial applications. The mechanisms of oxidation are complex, yet they reveal critical insights into how to enhance and protect aluminium materials.
In this article, we covered several key aspects of aluminium oxidation, providing a comprehensive exploration of its mechanisms, processes, and consequences. We discussed the thermodynamic factors, including standard electrode potentials and temperature effects, shedding light on how these elements impact oxidation rates. External conditions, such as humidity and atmospheric contaminants, were also reviewed to understand their influential roles.
The formation and characteristics of aluminium oxide were analyzed, emphasizing how these oxidation products contribute to corrosion resistance and material strengthening. The industrial applications highlighted not only showcase the benefits of controlled oxidation but also present opportunities for innovation in the field.
Furthermore, ecological considerations demonstrate that awareness of aluminium oxidation processes is vital for sustainable practices in manufacturing and material usage. The future research directions indicate promising areas for exploration, highlighting the importance of developing advanced analytical techniques and innovations in aluminium alloys.
Overall, aluminium oxidation is a crucial subject that intersects multiple domains, from material science to environmental sustainability. Recognizing its mechanisms and implications holds the key to advancing both industrial practices and ecological stewardship.
Key Takeaways
- Aluminium oxidation is a natural process that can lead to both beneficial and detrimental effects. Understanding this process is crucial for optimizing performance in various applications.
- Thermodynamic and environmental factors play a significant role in influencing oxidation rates and outcomes.
- Effective control techniques can enhance the protective qualities of aluminium, making it more resilient to corrosion and wear.
- Continued research is necessary to further comprehend the implications of oxidation and to develop innovative solutions that align with ecological concerns.
Implications for Future Work
The understanding of aluminium oxidation opens pathways for future research that can improve material performance and environmental impact. Here are some specific areas for consideration:
- Advanced Coatings: Developing novel coatings that enhance protection against oxidation while maintaining environmental compatibility.
- Material Innovation: Researching new aluminium alloy compositions that may exhibit better resistance to oxidation.
- Analytical Techniques: Utilizing cutting-edge technologies to analyze and characterize the oxidation process at a molecular level.
- Life Cycle Assessments: Evaluating the environmental impact of aluminium production and oxidation throughout its entire life cycle.
Future advancements in these domains will not only enhance our understanding of aluminium oxidation but also significantly contribute to more sustainable industrial practices.
"Understanding the mechanisms of aluminium oxidation is crucial for optimizing both material properties and ecological impact."