Thermal Oxidation Process: An In-Depth Analysis
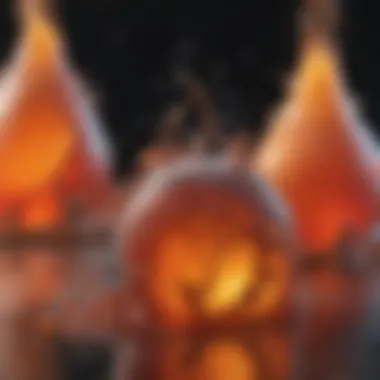
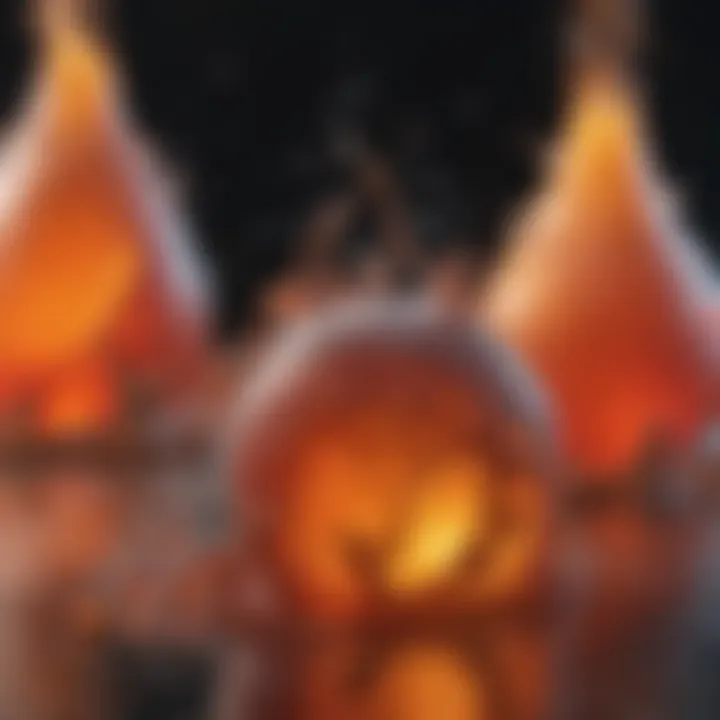
Intro
The thermal oxidation process is essential in both scientific research and industrial applications. It involves the chemical reaction between materials and oxygen at elevated temperatures. This reaction can lead to significant changes in the properties of the materials involved, and understanding these changes is crucial for various sectors, including semiconductor manufacturing, material synthesis, and waste treatment.
Increasingly, researchers focus on how temperature, time, and controlled environments influence the outcomes of this process. These factors are central to the optimization efforts aimed at maximizing efficiency while minimizing negative environmental impacts. As such, this article delves into the complex mechanisms behind thermal oxidation, showcasing its relevance in diverse fields.
By unpacking the principles and advancements in this area, we aim to provide a robust framework for both practitioners and scholars.
Research Overview
Summary of Key Findings
The examination of thermal oxidation has revealed several key findings:
- Elevated temperatures significantly enhance the reaction rate, resulting in improved oxidation efficiency.
- Controlled environments, such as inert gas atmospheres, minimize unwanted side reactions.
- Ultimately, optimizing these conditions leads to better quality and performance of materials.
This process not only aids in the development of more resilient materials but also extends the lifespan of components used in various technologies.
Relevance to Current Scientific Discussions
In current discussions, the thermal oxidation process intersects with topics like sustainability and material innovation. As industries trend toward greener technologies, understanding the environmental impacts of thermal oxidation becomes paramount. This includes evaluating emissions generated during reactions and strategies for energy efficiency. Researchers are now exploring novel methods to mitigate these effects, ensuring that the advancements in thermal oxidation do not come at the cost of the environment.
For those interested in further information, resources like the articles on Wikipedia and Britannica can provide additional insight into this important area.
Prolusion to Thermal Oxidation
Thermal oxidation is an essential process in various scientific disciplines and industrial applications. It plays a crucial role in material science and chemical engineering, serving diverse functions ranging from the production of silicon dioxide in semiconductor manufacturing to the reduction of volatile organic compounds in waste management. Understanding the fundamentals of this process can significantly impact effectiveness in these applications, leading to improved efficiencies and functionality.
Definition and Overview
Thermal oxidation can be defined as a method which involves the reaction of a material, typically silicon, with oxygen at elevated temperatures. The goal is to form an oxide layer on the surface of the material. This process is characterized by its ability to produce high-quality oxide films that are essential in many technological applications. For instance, in semiconductor fabrication, thermal oxidation creates an insulating layer of silicon dioxide that is crucial for device performance.
In addition to semiconductors, thermal oxidation is also used to enhance the durability of certain materials. oxidative layers can protect against environmental degradation, making products last longer in harsh conditions. Furthermore, the process can lead to changes in the physical and chemical properties of the material, enhancing its potential applications.
Historical Context
The origins of thermal oxidation can be traced back to the early research in semiconductor technology. In the mid-20th century, researchers discovered the significance of silicon dioxide layers in achieving effective electrical isolation in integrated circuits. As technology progressed, the techniques for achieving thermal oxidation improved. The introduction of controlled furnace environments allowed for precise temperature and time management, resulting in uniform oxide growth.
By the 1970s, thermal oxidation had established itself as a fundamental process within the semiconductor industry. The advancements in oxidation furnace technology greatly influenced the scalability of semiconductor manufacturing. In parallel, environmental concerns began to arise, leading to further exploration of thermal oxidation as a remediation technique for pollution control. This dual focus has made thermal oxidation an essential area of study, reflecting its importance across multiple sectors and its ongoing evolution.
> "Thermal oxidation is not just a fundamental process; it is a bridge connecting multiple disciplines, including material science and environmental engineering."
In summary, the introduction of thermal oxidation reveals its significance in both historical and modern contexts. It presents multiple layers of relevance, from its foundational role in electronics to its applications in environmental protection. As we delve deeper into the intricacies of this process, it becomes clear that thermal oxidation is more than just a chemical reaction; it is a cornerstone of multiple technological advancements.
Fundamentals of Thermal Oxidation
Thermal oxidation stands as a foundational technique in material science and chemical engineering, offering essential insights into the behavior of materials under elevated temperatures. Understanding these fundamentals is critical for students, researchers, educators, and professionals analyzing both the process's efficiency and its outcomes. By grasping the core principles and reactions involved, one can not only optimize the thermal oxidation process but also better appreciate its numerous applications in various industries.
Core Principles
The core principles of thermal oxidation revolve around the oxidation of materials, typically silicon or silicon dioxide, in an oxygen-rich environment. This process strengthens materials, making them more durable by forming a protective oxide layer. Key aspects include the interaction between thermal energy and reactants, which affects the rate of oxidation. When materials are heated, the kinetic energy increases, consequently enhancing reaction rates. The high temperature accelerates the diffusion of oxidants into the material, resulting in faster oxidation.
Achieving precise control over temperature is vital. The temperature must be optimized to ensure an efficient reaction without damaging underlying materials. In many applications, temperatures between 800°C and 1200°C are common. The balance between temperature and time is crucial. It determines the thickness and quality of the oxide layer formed during the oxidation process.
Key Reactions Involved
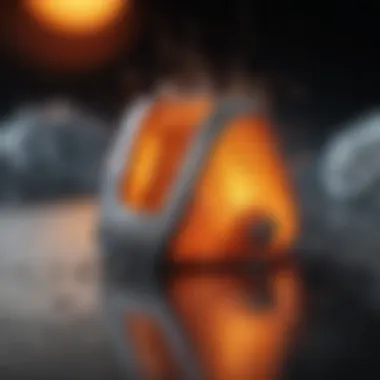
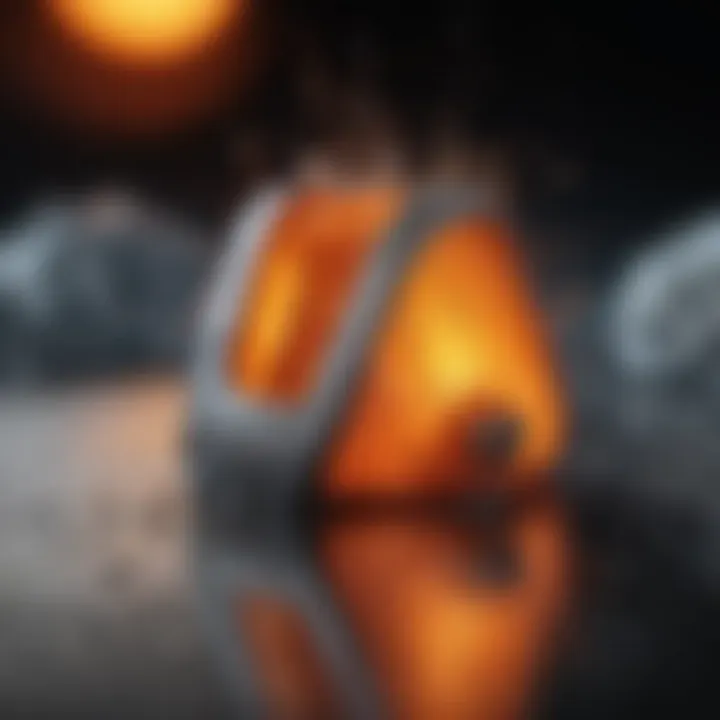
The primary reactions that underlie the thermal oxidation process typically involve the interaction between the material and oxygen. For silicon, the reaction can be summarized as follows:
- Silicon Oxidation: Si + O₂ → SiO₂
This reaction illustrates how silicon reacts with oxygen to generate silicon dioxide, a compound known for its insulating properties and resistance to corrosion.
When examining the kinetics of oxidation, two distinct regimes emerge: the initial oxidation phase and the linear growth phase. During the initial phase, a thin layer of oxide forms rapidly, while in the linear phase, the growth becomes more gradual. These phases can be described using Arrhenius equations, revealing how temperature influences reaction rates and the energy barrier for oxidation.
Thermodynamics of the Process
Thermodynamics plays a critical role in understanding how thermal oxidation processes operate efficiently. The Gibbs free energy change (ΔG) dictates whether a reaction will proceed spontaneously. In thermal oxidation, the reactions tend to be exothermic, meaning they release energy, which can facilitate further reactions.
The stability of the formed oxide layer depends on several factors, including temperature and partial pressure of oxygen. This results in different growth rates of the oxide layer depending on the conditions. The equilibrium between the oxidizing species and the material reflects intricacies of thermal oxidation.
In general, understanding the thermodynamic aspects helps predict the viability of the oxidation process under various environmental conditions.
"The ability to control thermal oxidation parameters is crucial for tailoring material properties to meet specific application requirements."
The Role of Temperature and Time
Temperature and time are critical factors in the thermal oxidation process. These variables directly influence the efficiency, effectiveness, and final outcomes of oxidation reactions. Understanding their roles can help optimize the process across various applications, from industrial manufacturing to environmental remediation.
Temperature Control Mechanisms
Temperature control is essential for maintaining the desired reaction rates during thermal oxidation. The process often involves high temperatures that can range from a few hundred to several thousand degrees Celsius. To achieve optimal results, precise control mechanisms ensure the temperature remains within a specified range.
Common methods for controlling temperature include:
- Thermal Sensors: Devices that continuously monitor the temperature in real-time, enabling adjustments as needed.
- Feedback Systems: Automated systems that alter heat input based on sensor readings, maintaining stability.
- Heat Exchangers: Equipment designed to regulate heating or cooling to achieve desired temperatures efficiently.
By utilizing these mechanisms, industries can minimize energy consumption while maximizing reaction rates, which is vital for sustainable processes.
Duration of Exposure and Its Effects
The duration of exposure is equally significant in thermal oxidation. Each material or substrate reacts differently to the length of exposure to high temperatures. Extended exposure might enhance oxidization, leading to improved material properties. However, too long an exposure can result in undesired degradation or damage to the substrate.
Key effects of exposure duration include:
- Oxide Layer Growth: Prolonged exposure can lead to thicker oxide layers, which may be beneficial in semiconductor applications but detrimental in other contexts.
- Material Integrity: Continuous high heat can negatively impact the structural integrity of certain materials.
- Rate of Reactions: Longer exposure usually increases the likelihood of secondary reactions, which may complicate outcomes.
In summary, both temperature control and duration of exposure are central to optimizing the thermal oxidation process, influencing material characteristics and overall process efficiency.
Applications of Thermal Oxidation
The applications of thermal oxidation are vast and crucial in a variety of fields. This technology provides solutions for numerous challenges both in industrial contexts and environmental management. Understanding how thermal oxidation is utilized can illuminate its significance. The process not only serves industrial needs but also plays an essential role in maintaining environmental standards.
Industrial Utilizations
In many industries, thermal oxidation is a necessary step in the manufacturing and processing of materials. For instance, in the chemical industry, it helps in the purification of gases by breaking down volatile organic compounds. This leads to cleaner emissions and compliance with environmental regulations.
Thermal oxidation is also essential within the oil and gas sectors. Here, it is used to treat waste gases that are produced during extraction and refining processes. By converting harmful compounds into less toxic emissions, companies ensure they minimize their environmental footprint.
Moreover, industries involved in the production of plastics and rubber often rely on thermal oxidation to control the quality of their end products. The technique helps in removing residual solvents and degrading polymers that could cause defects in the final products.
Environmental Remediation
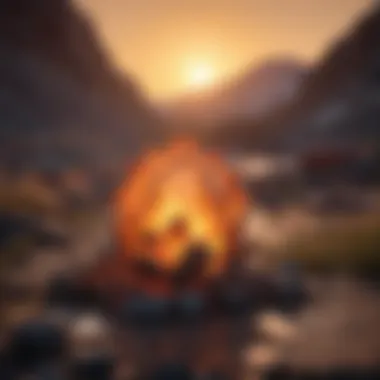
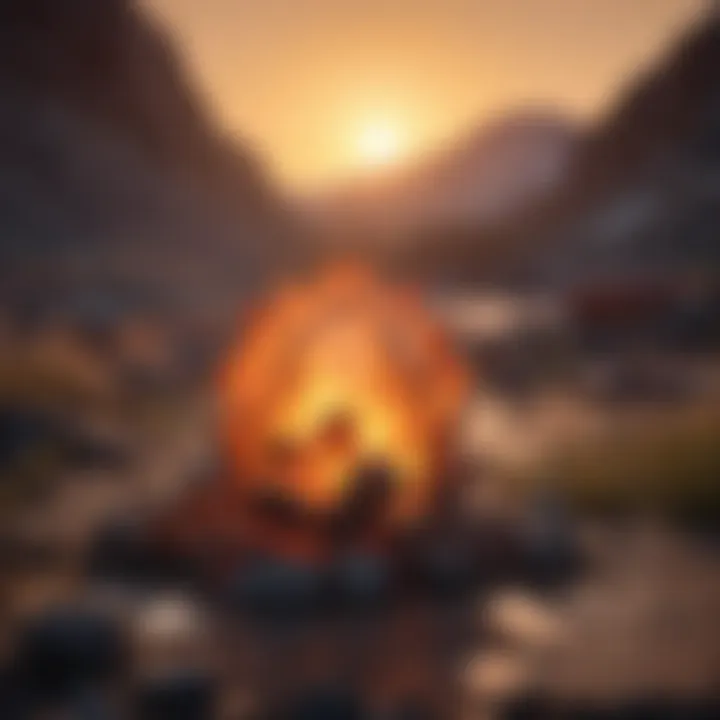
Thermal oxidation is increasingly employed for environmental remediation. As pollutants accumulate in the environment, traditional methods may not suffice to manage the level of toxicity present. This is where thermal oxidation presents a valuable alternative.
The technique can destroy hazardous waste, including solvents and other organic materials. Implementing thermal oxidation in contaminated sites leads to the effective breakdown of pollutants, resulting in a safer environment. Furthermore, it aids in remediation projects related to groundwater or soil contamination, thereby protecting human health and ecosystems.
"Thermal oxidation deploys heat to ensure that hazardous materials can be effectively transformed into harmless byproducts."
The ability to manage and mitigate risks associated with hazardous waste has made thermal oxidation a preferred choice in remediation efforts.
Role in Semiconductor Manufacturing
In the semiconductor industry, thermal oxidation plays a critical role in creating electronic devices. This process allows for the formation of silicon dioxide layers, which are essential for semiconductor devices. These layers serve as insulators and also protect the underlying silicon.
The precision of thermal oxidation ensures that there is uniformity and control over the oxide thickness. This is vital in nano-scale manufacturing, where minute variations can lead to device failures. By employing this technique, manufacturers can achieve the desired electrical properties and improve the reliability of their products.
Advanced Techniques in Thermal Oxidation
The realm of thermal oxidation has seen numerous advancements, resulting in sophisticated techniques that optimize production and reduce waste. This section will delve into these advanced methodologies, highlighting their benefits and important considerations. By incorporating cutting-edge strategies, professionals in various industries can significantly enhance the efficiency of thermal oxidation processes.
Innovations in Process Control
Process control is at the heart of successful thermal oxidation. Innovations in this area have made it possible to achieve consistent results while minimizing variances that can lead to subpar outcomes. One key aspect is the automation of temperature and pressure monitoring systems. By implementing advanced sensors and real-time analytics, operators can respond immediately to fluctuating conditions, ensuring optimal performance.
Moreover, PID (Proportional–Integral–Derivative) controllers are increasingly utilized. They allow for precise adjustments based on past, present, and anticipated process behaviors. This leads to a significant reduction in material consumption and enhances product quality. Enhanced computer models also aid in predicting thermal behavior in various circumstances, leading to improved planning and execution strategies.
Emerging Technologies
Emerging technologies are reshaping the landscape of thermal oxidation. For instance, plasma-assisted oxidation represents a leap forward. This method employs plasma to enhance reaction rates at lower temperatures, resulting in energy savings and reduced thermal stress on materials. This is particularly beneficial in sectors where delicate substrates must be treated without compromising their integrity.
Nanotechnology also plays a critical role in evolving thermal oxidation processes. By utilizing nanoparticles as catalysts, reactions can occur more efficiently, leading to faster processing times and higher yields. Furthermore, these nanoparticles can support the oxidation of exotic materials that are otherwise challenging to process.
The integration of these emerging technologies into thermal oxidation processes offers a competitive edge by enhancing efficiency while mitigating environmental impact.
In summary, embracing innovations in process control and recognizing the potential of emerging technologies will greatly benefit industries relying on thermal oxidation. These advancements promise increased efficiency, cost savings, and a reduced environmental footprint in thermal oxidation applications.
Environmental Considerations
The thermal oxidation process has significance beyond its industrial application. This technique plays a vital role in addressing environmental concerns. As societies strive towards sustainability, understanding the environmental considerations regarding thermal oxidation is crucial. The process does not merely involve combustion; it is essential for reducing harmful emissions and managing waste.
Impact on Air Quality
Thermal oxidation can significantly impact air quality. During the oxidation process, volatile organic compounds (VOCs) and other hazardous pollutants are subjected to high temperatures. This results in their conversion into less harmful substances. Chemicals like benzene and formaldehyde, if released into the atmosphere, can pose serious health risks. Therefore, implementing thermal oxidation systems helps mitigate these risks.
The effectiveness of different thermal oxidation setups varies. High-efficiency thermal oxidizers demonstrate an ability to reduce emissions by up to 99%. This is a clear benefit, especially for industries dealing with high VOC outputs. The reduction of airborne pollutants leads to improved air quality, which is beneficial for public health and the environment. Less pollution translates to fewer respiratory illnesses and better overall community health.
Regulatory Standards and Compliance
Regulatory standards are pivotal in ensuring that thermal oxidation processes are carried out within safe limits. Various international and national regulations oversee the emissions resulting from industrial processes. In the United States, for instance, the Environmental Protection Agency (EPA) has strict guidelines concerning air quality. Companies must comply with these standards to avoid penalties and ensure operational sustainability.
Key regulations include:
- National Emission Standards for Hazardous Air Pollutants (NESHAP)
- New Source Performance Standards (NSPS)
Meeting these standards typically involves adopting advanced thermal oxidation technologies. Companies must invest in both equipment and monitoring systems to demonstrate compliance. Regular inspections and emissions testing are part of the compliance process. Non-compliance can lead not only to financial repercussions but also significant reputational damage. Ensuring stringent adherence to regulatory standards further promotes an emphasis on cleaner production methods in the industry.
"Adhering to environmental regulations is not just a legal obligation; it is a commitment to sustainable progress."
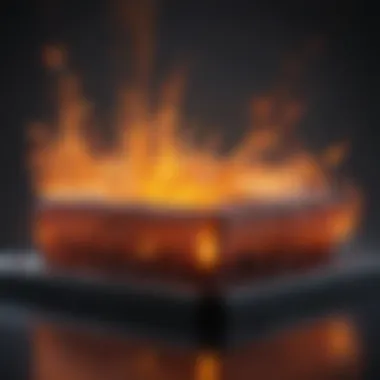
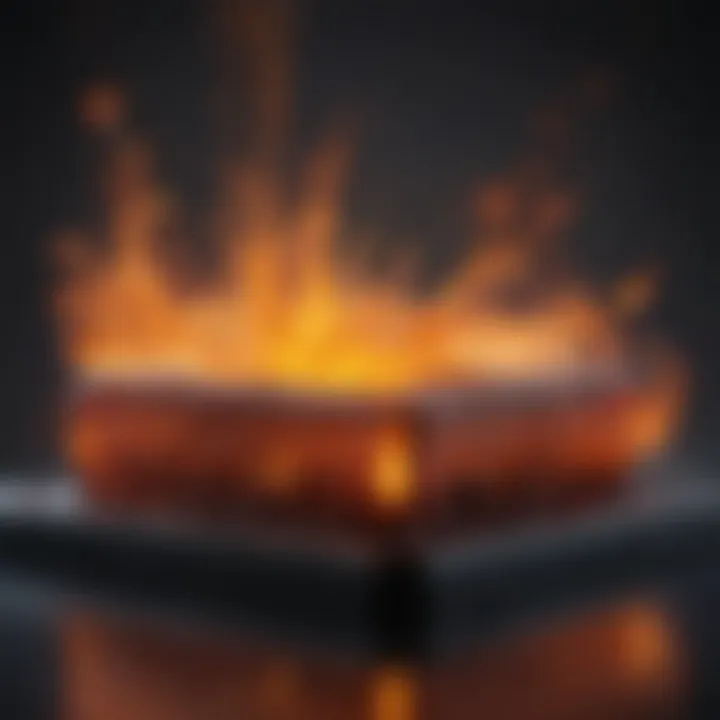
In summary, both the impact on air quality and adherence to regulatory standards are primary environmental considerations in the thermal oxidation process. As industries evolve, these aspects become increasingly critical in promoting sustainability and ensuring industrial practices align with environmental safety.
Challenges in Thermal Oxidation
The discussion on thermal oxidation is incomplete without addressing the challenges associated with its implementation. Understanding these challenges is crucial for researchers and industry practitioners. They can have significant implications on process efficiency, material integrity, and overall sustainability. These challenges necessitate careful consideration during the design and optimization phases of thermal oxidation processes.
Material Limitations
Material limitations present a primary concern in thermal oxidation. Various substrates can react differently under thermal oxidation conditions, leading to complications such as oxidation defects or material degradation. For instance, silicon forms a native oxide layer effectively. However, materials like certain polymers or metallic alloys can suffer severe performance drops when subjected to high-temperature environments.
The choice of materials for components in thermal oxidation setups must also take into account thermal stability, chemical reactivity, and long-term performance. Using inadequate materials not only risks operational inefficiencies but could also lead to increased maintenance costs and unscheduled downtime.
Common issues related to material limitations include:
- Thermal Cracking: High temperature can cause stresses in the material leading to fractures. This is especially true for brittle materials.
- Corrosion: Some materials may oxidize or corrode in the presence of reactive gases, diminishing their longevity.
- Insufficient Adhesion: Oxides formed on substrates sometimes do not adhere strongly, resulting in flaking and other surface issues.
Efficiency Constraints
Efficiency constraints are another critical aspect when evaluating thermal oxidation processes. High energy costs associated with maintaining elevated temperatures can make thermal oxidation less appealing in a cost-sensitive marketplace. Furthermore, achieving optimal reaction conditions often requires fine-tuning many variables, including temperature, time, and reactant concentrations.
Performance can be hindered by:
- Sub-optimal Reaction Conditions: Slight variations in temperature or exposure time can create significant differences in product quality. Finding the right balance is essential but often challenging.
- Heat Transfer Limitations: In larger batches, heat distribution may become uneven, causing inconsistent oxidation levels across materials.
- Contamination Risks: The presence of contaminants can alter reaction dynamics, leading to reduced efficiency and defects in the final product.
Consideration: Developers and engineers must focus on continuous monitoring and advanced controls to improve thermal oxidation efficiency.
Overall, while thermal oxidation holds significant advantages across various industries, addressing material limitations and efficiency constraints is vital to maximize its effectiveness. Each factor needs careful analysis to refine existing processes or develop new methodologies, ensuring that thermal oxidation remains a viable option in materials science and engineering.
Future Trends and Developments
Future trends in thermal oxidation are essential to understand. This section will explore specific elements, benefits, and considerations regarding the ongoing evolution of this technology. As industries seek improved efficiency and environmental compliance, significant changes are already emerging.
Research Directions
Research in thermal oxidation continues to expand. New findings are vital for refining processes and improving outputs. Current areas of focus include:
- Optimization of Reaction Conditions: Studies are enhancing understanding of temperature and duration in thermal oxidation. Adjustments can improve yield and reduce waste.
- Sustainable Materials: Research is exploring the compatibility of eco-friendly materials with thermal oxidation. This shift is to minimize environmental footprints.
- Advanced Control Systems: Development of real-time monitoring tools assists with precision in thermal oxidation processes. These systems can lead to significant improvements in process control and results.
A growing number of institutions and organizations are investing in this type of research. The aim is to align thermal oxidation processes with modern demands and regulations. Researchers seek to make these technologies more accessible and affordable, encouraging innovation in various fields.
Potential Industry Shifts
As advancements continue to unfold, industries dependent on thermal oxidation may undergo shifts. These changes will shape practices in different sectors:
- Increased Automation: Automation is becoming more prevalent. Integrating machine learning can amplify the efficiency and responsiveness of thermal oxidation systems.
- Regulatory Compliance: The evolving landscape of environmental regulations will push industries to adopt better thermal oxidation techniques. This complies with standards while reducing harmful emissions.
- Focus on Circular Economy: Companies are shifting towards practices that embrace sustainability. Thermal oxidation can play a role in waste-to-energy initiatives, capturing value from materials previously deemed waste.
In summary, the future of thermal oxidation will hold promising developments. By exploring new research avenues and adapting to industry needs, this process can become more efficient and environmentally friendly. It can significantly influence materials science and chemical engineering, making ongoing exploration critical.
Culmination
The conclusion serves as a vital section in this article as it encapsulates the key insights gathered throughout the exploration of thermal oxidation. This process significantly enhances our understanding of various applications ranging from environmental remediation to semiconductor manufacturing. By summarizing the essential components, readers gain a holistic perspective on how thermal oxidation operates within different contexts.
Summary of Key Insights
In review, the thermal oxidation process stands out due to its applicability and importance. Here are some key insights:
- Fundamental Mechanisms: The core principles of thermal oxidation involve chemical reactions in which materials, particularly semiconductors, react with oxygen under heat. This understanding is crucial for optimizing production and developing innovative materials.
- Industrial and Environmental Impact: The scope of thermal oxidation extends beyond manufacturing. Its role in environmental remediation demonstrates its dual functionality, aiding in air quality improvements by breaking down harmful pollutants.
- Challenges and Innovations: Despite the benefits, material limitations and efficiency constraints are challenges that need continuous addressing. Recent advancements reflect a trend towards improving these aspects, thereby increasing the viability of thermal oxidation in the long run.
Call for Continued Research
To advance the field of thermal oxidation, ongoing research is essential. There are several areas warranting deeper investigation:
- Optimization of Conditions: More studies should focus on refining temperature and time parameters to enhance efficiency without compromising material integrity.
- Exploration of Alternative Materials: Research into new materials that withstand the rigors of thermal oxidation can open avenues for improved applications across industries.
- Regulations and Practices: As environmental concerns grow, further exploration into compliance with evolving regulatory standards will be critical for practitioners and technologists alike.