Laser Ultrasonic Testing: Insights and Innovations
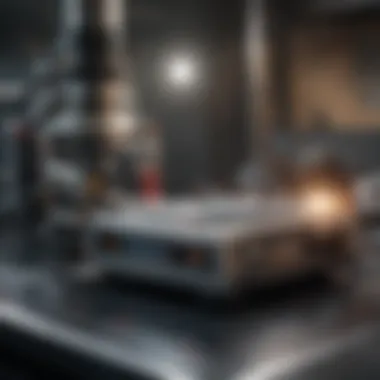

Intro
Laser ultrasonic testing stands at the intersection of advanced technology and practical applications in industrial settings. This innovative non-destructive testing (NDT) method employs laser-generated ultrasonic waves to assess the integrity of various materials without causing any physical damage. As industries strive for higher safety standards and efficiency, understanding laser ultrasonic testing has become increasingly essential.
This article will unravel the core principles of laser ultrasonic testing, exploring its mechanisms, diverse applications, and the recent advancements shaping its future. The aim is to deliver a clear and comprehensive understanding of how this technique operates and its significance across multiple fields, including aerospace, manufacturing, and civil engineering.
Key topics cover:
- Principles of Ultrasonic Wave Generation: A closer look at how laser technology generates ultrasonic waves, providing insight into the fundamentals of testing.
- Applications in Various Industries: Highlighting practical uses in sectors like aerospace and manufacturing, where material integrity is crucial.
- Technological Innovations: Examining advancements that improve the accuracy and efficiency of testing methods.
- Comparison with Traditional Testing: Understanding how laser ultrasonic testing stacks up against conventional techniques.
Through a detailed examination, readers will grasp not only the operational aspects but also the broader implications of laser ultrasonic testing in maintaining quality assurance and enhancing safety protocols.
Important Note: The relevance of laser ultrasonic testing stretches beyond theoretical knowledge; it impacts real-world applications, influencing policy and practice in industrial operations.
This exploration will deliver valuable insights for students, researchers, educators, and professionals alike, providing tools to navigate the rapidly evolving landscape of non-destructive testing.
Foreword to Laser Ultrasonic Testing
Laser ultrasonic testing represents a significant evolution in the realm of non-destructive testing (NDT). This technique harnesses the precision of laser technology to generate and assess ultrasonic waves, making it an invaluable tool for evaluating material integrity without causing damage. Understanding the nuances of this method is essential, especially for professionals engaged in quality assurance across various sectors.
Definition and Overview
Laser ultrasonic testing is a non-contact method that creates ultrasonic waves by focusing laser pulses onto a material. When the laser strikes the surface, it induces stress, leading to the generation of acoustic waves. These waves then propagate through the material. The interaction of these waves with potential defects or anomalies is analyzed to gain insights into the material's condition. This overview encapsulates how laser ultrasonic testing operates within the broader field of material science and engineering, providing an efficient means of ensuring safety and compliance in various applications.
Historical Context
The roots of ultrasonic testing date back to the early 20th century when scientists began exploring the use of sound waves for material evaluation. However, it wasn't until the advent of laser technology in the 1960s that laser ultrasonic testing emerged as a distinct method. The combination of lasers with ultrasonic techniques facilitated advancements in precision and sensitivity. Over the decades, continuous refinement of both laser and detection technologies has propelled laser ultrasonic testing into mainstream use, particularly in high-stakes industries such as aerospace and manufacturing.
Importance in Non-Destructive Testing
In the field of non-destructive testing, laser ultrasonic testing stands out for several reasons:
- Safety: By enabling thorough inspections without damaging materials, this technique significantly enhances safety protocols in industries that rely on robust material properties, like aviation and energy.
- Sensitivity: The ability to detect minute flaws makes this method suitable for critical component analysis, thus ensuring reliability and durability.
- Versatility: It can be applied to a wide range of materials, from metals to composites, adding to its utility across diverse sectors.
"Laser ultrasonic testing exemplifies the harmony of innovation and practicality, allowing for thorough checks without impairing the subject material."
Given its extensive applicability and reliability, laser ultrasonic testing is becoming an increasingly critical component in the framework of modern engineering and industrial quality control.
Fundamental Principles of Laser Ultrasonic Testing
Understanding the fundamental principles of laser ultrasonic testing is essential for grasping how this innovative technique enables effective evaluation of materials. Laser ultrasonic testing revolves around the ability to generate, propagate, and detect ultrasonic waves through various materials. The comprehension of this process leads to identifying defects, measuring thickness, and determining material integrity with a high degree of precision.
Laser Generation of Ultrasonic Waves
The process starts with the generation of ultrasonic waves using laser technology. Typically, a pulsed laser beam is focused onto the surface of the test material. The intensity of the laser light causes localized heating, resulting in thermal expansion. This expansion generates stress, which leads to the creation of ultrasonic waves that travel into the material. The key components involved here include:
- Laser Source: Commonly, Nd:YAG (neodymium-doped yttrium aluminum garnet) lasers are used due to their efficiency in producing short, high-energy pulses.
- Focused Delivery: The laser must be precisely focused on the material's surface to ensure efficient wave generation.
- Wave Characteristics: The generated ultrasonic waves can vary in frequency and type, including longitudinal and shear waves, depending on the application and material characteristics.
Propagation of Ultrasonic Waves
Once generated, the ultrasonic waves propagate through the material. Understanding this propagation is crucial because it determines how the waves interact with any flaws present in the material. The waves can reflect, refract, or diffract based on the properties of the medium, such as density and elastic modulus.
Several considerations concerning wave propagation include:
- Material Properties: Different materials affect the speed and attenuation of ultrasonic waves. For example, metallic materials generally allow for faster wave propagation than plastics.
- Flaw Interaction: When waves encounter defects like cracks or voids, they reflect back or scatter, which can be used to assess the integrity of the structure.
- Transducer Considerations: Laser ultrasonic testing utilizes optical transducers that can detect these waves, enhancing the sensitivity and resolution of the examination outputs.
Detection Techniques
Detecting the generated ultrasonic waves is fundamental to analyzing the data for material integrity assessment. Several techniques can be employed for detection:
- Interferometry: This technique involves measuring the phase changes of the ultrasonic waves using laser-based interferometers. It enables precise measurements of displacements and surface vibrations.
- Optical Sensors: Specialized detectors can capture the response of ultrasonics as they travel through the material, allowing for real-time monitoring.
- Signal Processing: Advanced algorithms assist in interpreting the ultrasonic wave data, filtering noise and enhancing the clarity of results.
Investing in understanding these fundamental principles offers advantages in quality assurance and harsh environment testing processes. Through laser ultrasonic testing, industries can ensure higher reliability in their materials while adhering to stringent regulatory standards.
Comparative Analysis with Conventional Testing Methods
Understanding the distinctions between laser ultrasonic testing and traditional non-destructive testing methods is crucial. This analysis provides insight into the efficacy and practicality of laser ultrasonic testing in various applications. By evaluating its advantages, limitations, and applicable scenarios, one can gain a clearer view of its role in contemporary industry.
Advantages of Laser Ultrasonic Testing

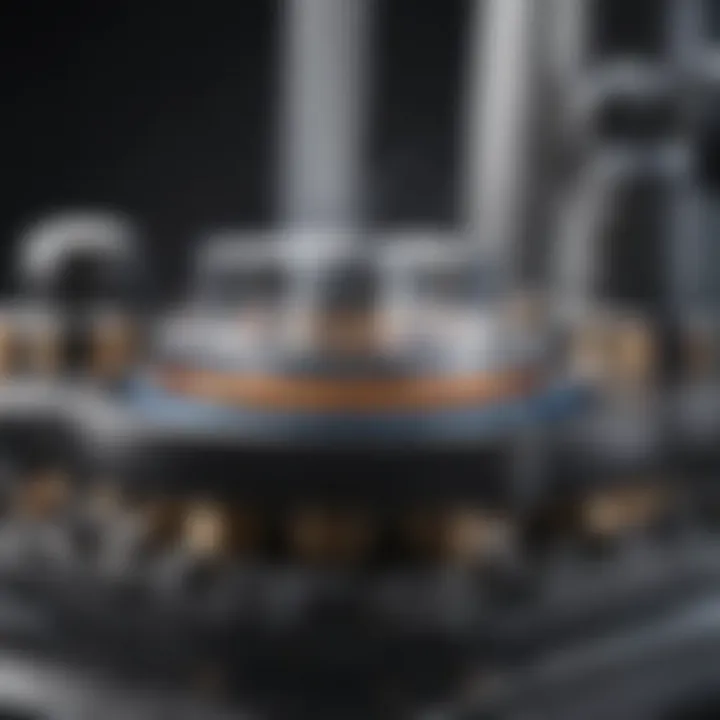
One of the significant benefits of laser ultrasonic testing lies in its ability to measure with precision without physical contact. This non-invasive method allows for the evaluation of sensitive materials where conventional methods may cause damage. In addition, it offers:
- High spatial resolution: Laser ultrasonic testing can detect very fine features in materials, improving overall inspection quality.
- Remote inspection: The capacity to inspect components from a safe distance enhances operator safety while increasing accessibility to hard-to-reach areas.
- Real-time analysis: The immediate feedback from tests enables swift decision-making and efficient workflow.
- Reduced coupling issues: Traditional methods often require gels or other couplings, which can introduce variables into measurements. Laser techniques eliminate this concern.
Limitations and Challenges
Despite its advantages, laser ultrasonic testing comes with its own set of challenges. Understanding these is essential for appropriate application. Some of the main limitations are:
- Cost: The equipment needed for laser ultrasonic testing can be expensive, which may deter small enterprises from adoption.
- Skill requirements: Proper operation and interpretation of data necessitate specialized training, making it less accessible for some users.
- Surface conditions: The effectiveness of laser measurements can be affected by surface imperfections. Difficulties are found if the surface is rough, painted, or contaminated.
Situational Applicability
The choice between laser ultrasonic testing and traditional methods often hinges on the specific requirements of a project. Scenarios where laser technology excels include:
- Aerospace component integrity: Given the stringent safety requirements, precise measurement of defects is paramount. Laser ultrasonic testing provides a reliable solution.
- Thin materials: When dealing with thin-walled structures, the non-contact nature of laser tests minimizes risk of damage.
- Complex geometries: Laser ultrasonic testing adapts well to complex shapes, providing detailed insights where traditional methods may struggle.
Technological Innovations in Laser Ultrasonic Testing
Technological advancements have played a crucial role in the development and refinement of Laser Ultrasonic Testing (LUT). Innovating within this field introduces significant benefits, improves accuracy, and enhances the efficiency of testing procedures. It is crucial to analyze the specific elements of these innovations, the benefits they provide, and considerations that need to be made when implementing them.
Recent Advancements in Laser Technology
Recent advancements in laser technology have revolutionized Laser Ultrasonic Testing. The development of high-power, ultrafast lasers allows for more precise generation of ultrasonic waves. These new lasers can produce short pulses of light that quickly excite materials, resulting in higher resolution images.
Advantages of these advancements include:
- Increased Sensitivity: New laser systems are more sensitive, allowing for the detection of smaller defects in materials.
- Higher Frequency Generation: Advanced laser technologies enable the generation of ultrasonic waves at higher frequencies. This leads to better resolutions in testing results.
- Versatility: Modern laser technologies can be adapted for different materials, enabling broader applications across various industries.
Integration with Digital Technologies
The integration of digital technologies with laser ultrasonic testing systems has enhanced operational efficiency and data management. Modern LUT devices can now incorporate artificial intelligence and machine learning algorithms to analyze testing data. This automation streamlines the evaluation process, making it faster and more accurate.
Key components of this integration include:
- Real-time Data Processing: Digital systems enable immediate processing and feedback, which is essential for high-stakes testing environments like aerospace.
- Data Visualization and Reporting Tools: Enhanced software provides graphical representations of data, making it easier for engineers to understand results.
- Remote Testing Capabilities: With cloud technology, inspection can occur in remote locations without compromising data integrity.
Improvements in Data Analysis Techniques
Improvements in data analysis techniques are transforming how data from laser ultrasonic tests is interpreted. Advanced algorithms and software have been developed to analyze waveforms more effectively, which allows for more comprehensive assessments of material integrity.
Considerations within this realm include:
- Enhanced Defect Detection: Improved algorithms can identify subtle defects that previous techniques might have missed.
- Predictive Analytics: Techniques now allow for predictive modeling based on historical data trends, aiding in proactive maintenance decision-making.
- Cross-Platform Compatibility: New tools can integrate data from different systems, promoting collaborative environments among engineers and researchers.
The advancements in laser ultrasonic testing not only increase the reliability of testing but also expand its applicability across various fields, from aviation to infrastructure.
In summary, the technological innovations in laser ultrasonic testing, including advancements in laser technology, digital integration, and data analysis techniques, provide substantial improvements in effectiveness and efficiency. They enable the industry to meet evolving standards while ensuring material integrity and safety.
Applications of Laser Ultrasonic Testing
The applications of laser ultrasonic testing (LUT) span a wide array of industries, ranging from aerospace to medical device testing. Understanding these applications is crucial, as they not only demonstrate the technique’s versatility but also highlight its role in ensuring safety and reliability in various sectors. The following subsections provide an in-depth examination of specific fields where LUT plays a pivotal role, considering the benefits and considerations associated with each.
Aerospace Industry
In the aerospace sector, precision and safety are paramount. Laser ultrasonic testing is employed to inspect critical components such as turbine blades, wing structures, and fuselage sections. The use of this technique allows for early detection of flaws that could lead to catastrophic failures.
Some key advantages include:
- High Sensitivity: LUT can detect minute cracks and imperfections which are often missed by traditional methods.
- Non-Invasive: Unlike some methods, laser ultrasonic testing does not require contact with the material, preventing damage during inspection.
- Speed: The efficiency of this technique allows for faster assessments, which is essential in the aerospace industry where production times may be tight.
Manufacturing Sector
In the manufacturing industry, laser ultrasonic testing enhances quality control processes, ensuring that products meet strict industry standards. This technique is used in the inspection of welds, castings, and other manufactured components.
Benefits of LUT in manufacturing include:
- Cost-Effective: Early identification of defects can significantly reduce waste and rework costs.
- Adaptability: LUT can be used on a variety of materials, including metals, plastics, and composites, making it suitable for diverse manufacturing environments.
- Data Collection: The ability to gather and analyze high-quality data enhances decision-making processes regarding production quality.
Civil Engineering Applications
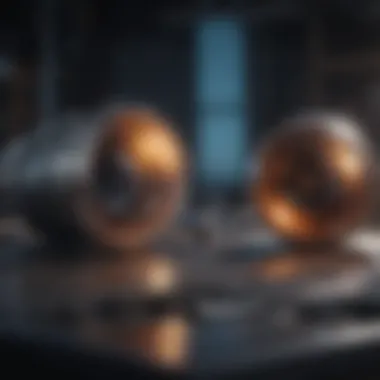
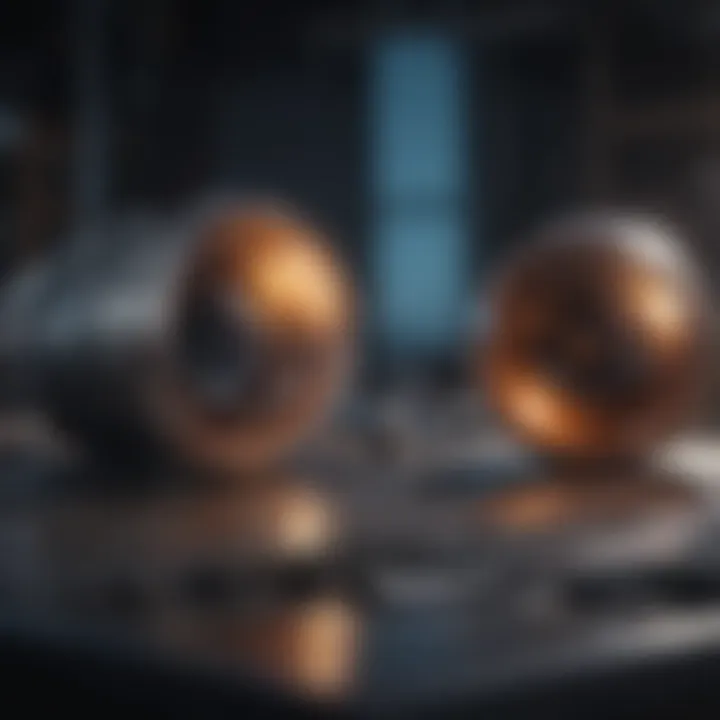
Civil engineering relies on the integrity of structures such as bridges, tunnels, and buildings. Laser ultrasonic testing plays a critical role in assessing the conditions of these infrastructures.
Key considerations for using LUT in civil engineering include:
- Structural Health Monitoring: Regular assessments using LUT can help in monitoring the health of existing structures, potentially extending their lifespan.
- Risk Management: It aids in identifying areas of concern, thereby reducing the risk of structural failures and improving public safety.
- Compliance: Helps ensure that structures comply with safety regulations and standards.
Medical Device Testing
In the medical field, ensuring the integrity of devices is crucial, especially those used in critical applications. Laser ultrasonic testing is vital in the validation of materials used in medical devices, such as implants and surgical instruments.
The advantages of LUT in medical device testing can include:
- Precision: High-resolution imaging provided by LUT ensures that even the smallest defects are identified in complex geometries.
- Quality Assurance: Continuous monitoring throughout the manufacturing process ensures compliance with rigorous health standards.
- Regulatory Alignment: Helps manufacturers comply with health regulations by providing evidence of material integrity.
In summary, laser ultrasonic testing is indispensable across multiple industries, offering numerous advantages in terms of quality assurance, safety, and efficiency. As technology evolves, its role in various applications will likely expand further, making it a critical tool for future innovations.
Case Studies in Laser Ultrasonic Testing
Exploring case studies in laser ultrasonic testing is crucial for understanding its practical applications. These studies provide real-world examples that showcase the effectiveness and versatility of this advanced technique. They highlight the challenges faced in various industries and demonstrate how laser ultrasonic testing can be a reliable solution for ensuring material integrity and safety. By analyzing specific instances, we can gather insights that inform best practices and future innovations in this technology.
Application in Aerospace Component Inspection
The aerospace industry demands the highest standards of quality assurance. Components must meet strict safety and regulatory requirements to prevent catastrophic failures. Laser ultrasonic testing serves as a powerful tool in this sector.
In one notable case, a leading aerospace manufacturer utilized laser ultrasonic testing to assess the integrity of critical aircraft components, such as wings and fuselage sections. Traditional methods often fell short in detecting subtle defects, especially in complex geometries. Using this advanced technique, engineers were able to generate and analyze ultrasonic waves with high precision. They identified flaws that conventional methods missed, thus enhancing safety and performance.
Benefits of Using Laser Ultrasonic Testing in Aerospace:
- High resolution and sensitivity to defects
- Ability to inspect complex shapes and structures
- Non-contact nature minimizes potential damage
- Faster inspection times compared to traditional methods
Use in Pipeline Integrity Assessment
Pipeline integrity is vital for industries like oil and gas, where any faults can have severe consequences. Laser ultrasonic testing offers an innovative approach for monitoring the health of pipelines.
In a specific project, engineers deployed laser ultrasonic technology to evaluate a section of an aging pipeline in a remote location. This area was difficult to access using conventional testing methods. The laser-based system was able to gather data on wall thickness and internal defects without direct contact. By analyzing the ultrasonic waves, they could detect anomalies that indicated wear and potential leaks.
Considerations for Pipeline Integrity Assessment:
- Periodic monitoring is essential to prevent failures
- Laser ultrasonic testing can cover large areas quickly
- Use of remote sensing technologies enhances accessibility
- Data analysis capabilities support proactive maintenance
Laser Ultrasound for Weld Quality Evaluation
Welds are critical points of structural integrity in various applications, from construction to manufacturing. Ensuring their quality is paramount. Laser ultrasonic testing provides a stringent evaluation method for welds, making it a preferred choice in many fields.
In one case, a manufacturing company used laser ultrasonic testing to assess the quality of welds in pressure vessels. The method allowed for real-time analysis during production. As a result, they could detect discontinuities and irregularities instantaneously. This not only improved the overall quality of the vessels but also reduced rework and scrap rates.
Key Advantages in Weld Quality Evaluation:
- Real-time monitoring improves quality control
- Capability to detect subsurface defects
- Minimal disruption to the production process
- Enhances reliability in critical applications
In summary, case studies in laser ultrasonic testing significantly enhance our understanding of its capabilities and applications across various industries. Through examining specific instances like aerospace inspections, pipeline assessments, and weld evaluations, we can appreciate the importance of these technologies in maintaining safety and quality standards.
Regulatory Standards and Guidelines
The significance of regulatory standards and guidelines in Laser Ultrasonic Testing (LUT) cannot be overstated. These standards ensure that testing methods meet minimum quality and safety requirements. By adhering to well-established protocols, professionals in various industries can guarantee the integrity of their testing processes and results. Regulatory standards act as a framework that informs best practices in operations, equipment calibration, and personnel competency.
When discussing Laser Ultrasonic Testing, the benefits of these standards include increases in confidence and assurance. Clients and stakeholders find reassurance in knowing that the practices used to evaluate materials and structures are consistent with global benchmarks. Such adherence leads to increased credibility in the results produced by these sophisticated techniques.
Moreover, compliance with regulatory standards often aids in minimizing legal liability. By following the prescribed guidelines, organizations can defend against potential claims related to negligence or inaccuracies in testing. Hence, it is clear that regulatory standards not only enhance quality but also provide legal safeguards for organizations reliant on these methodologies.
"Standards are essential as they create a baseline for quality and safety in testing practices."
ISO Standards
International Organization for Standardization (ISO) standards play a pivotal role in the realm of Laser Ultrasonic Testing. These standards are designed to unify testing processes across international borders. Specifically, ISO standards such as ISO 11666 cover the basic principles and processes involved in ultrasonic testing. These guidelines focus on aspects like equipment calibration, testing procedures, and technical qualifications of the personnel involved.
The ISO standards ensure consistency and reliability in testing outcomes. By following these established norms, professionals and organizations can align themselves with a global standard. This alignment is particularly beneficial for multinational companies that operate in various jurisdictions and need to comply with different regulatory environments. Adhering to ISO standards also fosters a culture of continuous improvement within organizations.
In addition, ISO standards help facilitate communication and understanding among professionals in the field. When everyone utilizes the same terminology and methodologies, the potential for misunderstanding diminishes significantly. As a result, the industry benefits from enhanced collaboration and innovation, particularly in terms of new technologies and methodologies.
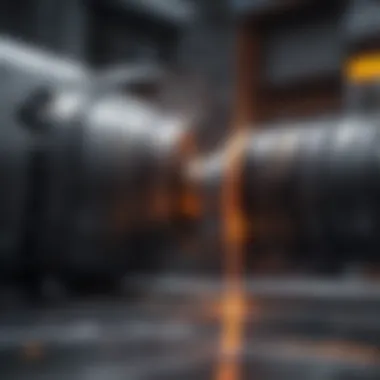
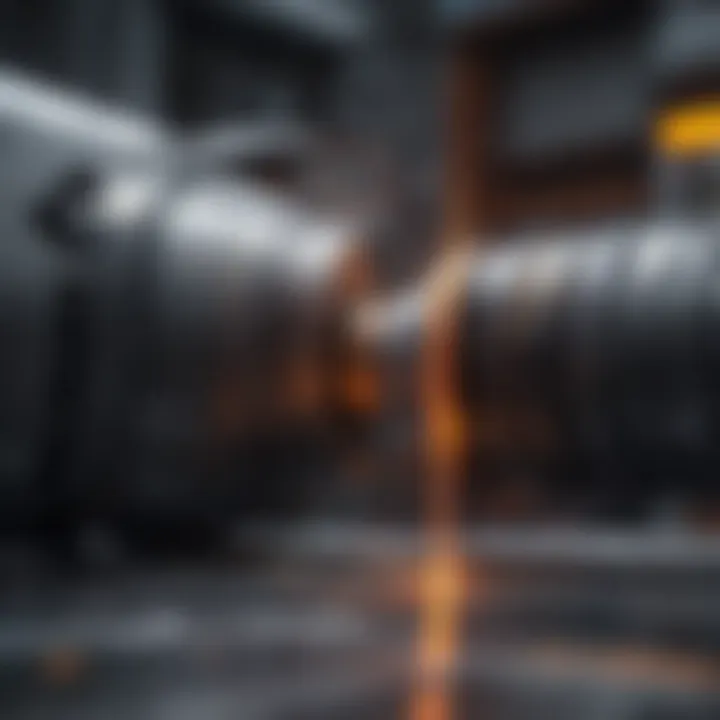
Industry-Specific Regulations
Aside from ISO standards, there are also numerous industry-specific regulations that dictate the practice of Laser Ultrasonic Testing. Different sectors have unique requirements due to the varied nature of the materials being tested and the associated risks. For instance, the aerospace industry is subject to stringent standards laid out by the Federal Aviation Administration (FAA). These guidelines necessitate meticulous inspection of components to ensure they meet high safety standards essential for aviation.
Similarly, in manufacturing, organizations often must adhere to standards established by the American National Standards Institute (ANSI). These regulations provide protocols for equipment testing and quality control measures that must be implemented in manufacturing processes. By complying with these industry-specific regulations, manufacturers can maintain consistent quality in their products while also protecting their customers from potential failures.
In sectors such as oil and gas, regulations often emphasize environmental safety and equipment integrity. Compliance with such regulations can lead to reduced environmental risks and improved operational efficiency. This is a direct reflection of the ongoing evolution of regulatory frameworks in response to industry demands and safety imperatives.
In summary, the regulatory landscape surrounding Laser Ultrasonic Testing is pivotal for ensuring quality, safety, and innovation in various industries. As the field continues to develop, keeping abreast of these guidelines is essential for professionals dedicated to maintaining high standards in non-destructive testing.
Training and Certification in Laser Ultrasonic Testing
Training and certification in laser ultrasonic testing (LUT) are vital parts of ensuring the integrity and effectiveness of the technique. As industries adopt this advanced method for material evaluation, the need for skilled professionals is increasing. Proper training guarantees that technicians understand the principles of laser ultrasonic testing as well as its applications, ensuring accurate results. Certification provides a level of assurance to employers and clients that the personnel have necessary skills and knowledge to perform the testing effectively.
Educational Programs
Educational programs in laser ultrasonic testing vary widely, catering to different levels of expertise. Some programs offer basic courses aimed at introducing the key concepts of ultrasonic testing, while others delve deeper into the technical specifics of laser applications.
Many institutions provide practical training paired with theoretical knowledge. This dual approach helps students build essential skills. Some common features of these programs include:
- Hands-on Experience: Workshops and labs facilitate practical application of concepts.
- Online Courses: For professionals, many reputable sites offer flexible online training.
- University Degrees: Some universities integrate laser ultrasonic testing into broader materials science or engineering programs.
Each educational pathway equips students with knowledge to handle specialized equipment and analyze ultrasonic wave data.
Certification Bodies and Requirements
Acquiring certification in laser ultrasonic testing signifies a recognized capability in performing this non-destructive testing technique. There are specific organizations that oversee the certification process, which may vary by region or industry. Generally, certification requires successful completion of a training program followed by an examination.
Key requirements often include:
- Completion of a Certified Course: Candidate must complete a recognized LUT program.
- Work Experience: Many certification bodies require a minimum number of hours of practical experience.
- Passing an Exam: Candidates typically must demonstrate their understanding through a written test.
Certification is maintained through periodic renewal, which includes ongoing education or re-testing standards. This ensures that certified technicians stay current with advancements in laser technology and testing techniques.
"The quality of laser ultrasonic testing depends not only on the technology itself but significantly on the competency of those operating it."
Future Prospects of Laser Ultrasonic Testing
The future of laser ultrasonic testing holds considerable promise for advancing non-destructive testing methods. This technique has already transformed material evaluation processes, yet it continues to evolve in ways that can significantly impact several industries. With advancements in technology, changing industry demands, and increased focus on safety and efficiency, the potential for laser ultrasonic testing is vast.
One critical aspect is the increasing integration of artificial intelligence and machine learning into data analysis. These technologies can enhance the interpretation of ultrasonic signals, enabling more accurate defect detection. The automation of data processing not only increases the efficiency of inspections but also reduces the chances of human error. As a result, companies can ensure higher quality standards while minimizing costs.
Additionally, the advent of portable laser systems is another trend shaping the future of this field. Compact and lightweight equipment allows for inspections to be performed on-site, providing immediate results. This capability is especially beneficial in industries such as aerospace and manufacturing, where quick decision-making is essential. On-site testing can also decrease downtime associated with transporting materials to laboratories for analysis.
Emerging Trends
Several emerging trends in laser ultrasonic testing are setting the stage for its enhanced application and relevance. These trends include:
- Increased Miniaturization: As technology advances, devices are becoming smaller yet more powerful. Miniaturized laser ultrasonic systems can be integrated into production lines for continuous monitoring of material integrity.
- Real-time Monitoring: Advancements in communication technologies such as IoT enable real-time monitoring of materials during processing. This facilitates proactive maintenance actions, thus preventing costly failures.
- Expanded Use in Complex Geometries: Continued advancements in laser optics are improving the ability to conduct tests on complex geometrical structures. This means that even intricate designs, such as those in aerospace components, can be evaluated efficiently.
"The continuous research and development in laser ultrasonic testing can lead to ground-breaking applications that improve safety and efficiency across several sectors."
Potential Areas for Research
Research can significantly contribute to the future of laser ultrasonic testing. Some notable areas include:
- New Waveform Techniques: The exploration of new and exotic waveform generation techniques may yield better insights into material behavior under stress.
- Investigation of Multi-material Assemblies: Understanding how different materials interact when bonded together is critical. Research focused on this can uncover important parameters that influence the performance of components in various applications.
- Standardization of Procedures: With the increasing adoption of laser ultrasonic testing, the development of standardized procedures can enhance its acceptance and application across industries. Research into best practices can be a path toward establishing such standards.
- Integration with Other Technologies: Examining the synergy between laser ultrasonic testing and other non-destructive testing methods, like radiographic or magnetic particle testing, could open new avenues for comprehensive assessments.
The future prospects of laser ultrasonic testing present exciting opportunities. Continued advancements will likely lead to safer, more efficient methods of assessing material integrity across various sectors.
Closure
In evaluating the intricate world of laser ultrasonic testing, one finds a technique that is not only innovative but also essential for quality assurance across multiple industries. The conclusion of this article underscores the significance of laser ultrasonic testing in modern non-destructive evaluation practices. As technology progresses, the demand for precise and non-intrusive methods becomes increasingly critical. This method presents notable benefits, such as improved accuracy and the ability to assess components without compromising integrity.
Summary of Key Points
- Definition: Laser ultrasonic testing utilizes laser technologies to generate ultrasonic waves for material evaluation.
- Historical Context: This technique has evolved, integrating advancements in technology and meeting industrial requirements.
- Comparative Analysis: Laser ultrasonic testing offers advantages over traditional methods, including enhanced accuracy and the capability of remote testing.
- Applications: It serves diverse sectors such as aerospace, manufacturing, civil engineering, and medical device testing.
- Regulatory standards: Compliance with ISO standards and industry-specific regulations ensure reliability and safety.
- Future of the industry: Emerging trends indicate continuous advancement in technology and further research potential, which will enrich this testing method.
Final Thoughts on the Impact of Laser Ultrasonic Testing
The importance of laser ultrasonic testing transcends mere functionality; it positions itself as a pivotal component in the field of non-destructive testing. As industries strive for greater efficiency, safety, and quality, this testing method demonstrates its multifaceted benefits. It addresses critical assessments where traditional methods may fall short. The integration of digital technologies and data analysis enhances capabilities, ensuring that industries can meet stringent regulatory standards and customer expectations. The unfolding future promises even more innovations and applications, sustaining the relevance and necessity of laser ultrasonic testing in engineering and manufacturing landscapes.
"The commitment to quality assurance starts with understanding and employing methods that reduce risk while maximizing reliability."
In summary, this article captures the essence and relevance of laser ultrasonic testing. The ongoing advancements and its widespread applicability ensure it remains a revered technique in various fields.