Exploring the Impact and Uses of PE Sensors
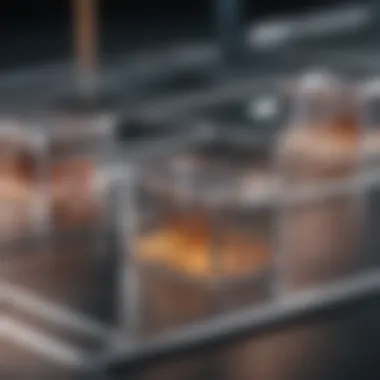
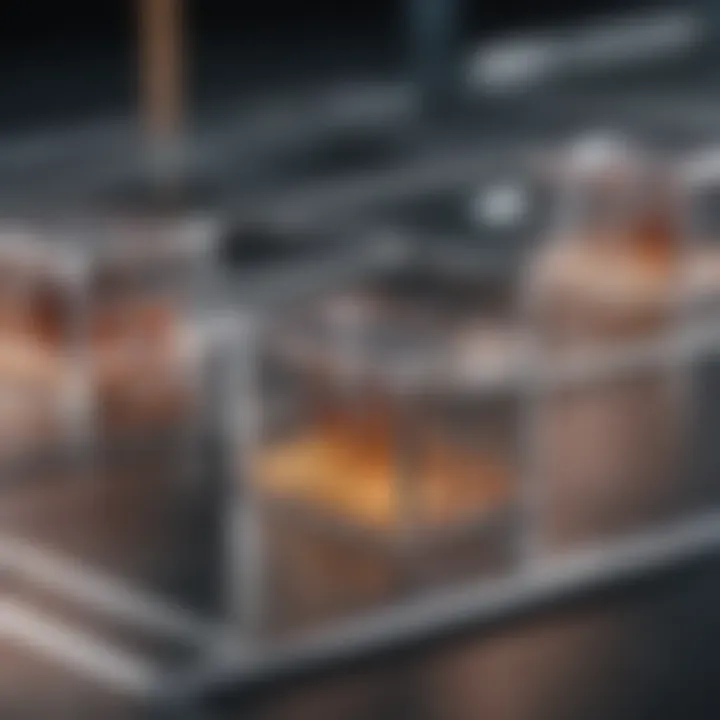
Intro
Polymer Electrolyte (PE) sensors have been gaining traction across various industries due to their unique operational characteristics and advantages over traditional sensing technologies. As technology evolves, so do the demands for enhanced precision and reliability in measurement systems. PE sensors offer innovative solutions that are not only effective but also versatile, making them an attractive choice in various applications ranging from automotive to healthcare.
The world of sensor technology is intricate, with each type catering to specific needs. PE sensors, in particular, utilize the properties of polymer electrolytes, enabling them to exhibit enhanced performance metrics. This article delves deeper into the principles that govern these sensors, their strengths and weaknesses, and a broad spectrum of applications they serve.
With a focus on insightful exploration, the subsequent sections will discuss the cutting-edge advancements in PE sensor technology, offering a glimpse into future trends and potential implications across multiple industry sectors.
Preamble to PE Sensors
The landscape of sensor technology has evolved significantly over the past few decades. Among the myriad of options available, Polymer Electrolyte (PE) sensors stand out as a significant achievement in precision measurement. Their ability to assess and measure pressure accurately has established them as vital components in various industries. Understanding PE sensors can provide critical insights, especially in fields like automotive safety, medical diagnostics, and industrial automation.
Definition and Overview
PE sensors can be succinctly defined as devices that measure pressure through electrochemical reactions in a polymer electrolyte medium. This definition, however, barely scratches the surface of their functionality and the unique properties they offer. Unlike traditional pressure sensors, PE sensors exhibit remarkable sensitivity to pressure changes and a wider operational range. This sensitivity makes PE sensors indispensable in applications where precision and reliability are non-negotiable.
These sensors operate on the principles of ion conduction and electrochemical potentials. The mechanism helps in translating mechanical pressure into an electrical signal. As a result, they not only cater to high accuracy but also ensure minimal drift over time, which is critical in many applications.
To put it plainly, if you're seeking a sensor that measures pressure without the common pitfalls of older technologies, PE sensors might just be the ticket.
Historical Background
The genesis of PE sensor technology is rooted in the broader development of polymer chemistry and electrochemistry that began to gain momentum in the mid-20th century. Initially designed for simple applications, engineering advancements and material science breakthroughs have propelled PE sensors to the forefront of measurement technologies. Early iterations of these sensors were bulky and primarily served niche markets.
By the 1980s, researchers began to recognize the potential of integrating flexible polymer materials with electronic components. This led to the development of sensors that could not only endure a range of environmental conditions but also provide real-time feedback. Industries that required precise pressure measurements, like aerospace and medical, were quick to adopt these groundbreaking devices.
At present, PE sensors are not just limited to specialized fields; they have made their way into consumer electronics, automotive industry, and beyond, demonstrating just how versatile and crucial they have become. Their role has only deepened over time, underscoring their growing importance in our technologically-driven world.
Operational Principles
Understanding the operational principles of Polymer Electrolyte (PE) sensors is crucial for grasping how they function and their significance in various applications. These principles are the foundation on which the performance and reliability of PE sensors stand, influencing factors such as sensitivity, accuracy, and overall effectiveness in pressure measurement.
Detection Mechanisms
PE sensors utilize a host of detection mechanisms to measure pressure effectively. The core principle revolves around the conversion of pressure into an electrical signal. When pressure is applied to the sensor, it affects the polymer electrolyte material.
- Capacitive Mechanism: In some PE sensors, changes in capacitance corresponding to pressure variations are measured. The configuration and dielectric properties of the material may vary due to applied pressure, translating these alterations into electrical signals.
- Piezoelectric Effect: Certain PE sensors exploit piezoelectric materials that generate an electric charge response when subjected to mechanical stress. This phenomenon allows for real-time pressure monitoring, with the generated electrical signal directly proportional to the applied pressure.
- Resistive Measurement: Additionally, resistive methods can be used where the resistance of a conductive polymer changes with pressure. The resistance change is then correlated with specific pressure levels.
These mechanisms are not merely academic; they represent what keeps the wheels of various industries turning smoothly. For instance, automotive applications greatly benefit from the precision of these detection methods, ensuring that safety measures are always in check.
Material Properties of PE Sensors
The effectiveness of PE sensors hinges significantly on the material properties of the polymer electrolytes utilized. Fundamental characteristics include:
- Conductivity: The ionic conductivity of the polymer must be high enough to facilitate efficient ion transport. This is pivotal for accurate pressure sensing since a well-conducting electrolyte can yield better performance.
- Mechanical Strength: The polymer's strength ensures its ability to withstand environmental factors such as humidity and temperature fluctuations. A robust material means longevity and reliability in sensor performance.
- Temperature Stability: Different applications expose sensors to varied temperature ranges. Therefore, the selected polymer must maintain its structural and functional properties across these temperatures.
These material considerations often dictate the suitability of PE sensors for particular applications, especially where precision and reliability are non-negotiable.
Electrical Characteristics
The electrical characteristics of PE sensors dictate how efficiently they operate and convey pressure information. Each of the factors plays a critical role in determining sensor performance:
- Sensitivity: A high sensitivity implies that minute changes in pressure will result in significant output signals. This characteristic is paramount in fields where even tiny pressure variations have serious implications.
- Linearity: Ideally, the relationship between pressure and output signal should be linear. A linear response allows for straightforward interpretation of measurements, facilitating easier integration into systems requiring precise measurements.
- Response Time: The speed at which the sensor responds to pressure changes is vital in high-speed applications. A fast response time ensures that systems can react promptly to any pressure changes, particularly in automotive or aerospace settings where time is of the essence.
In summary, the operational principles of PE sensors underscore their vital function in various applications. By focusing on detection mechanisms, material properties, and electrical characteristics, one can appreciate the roles these sensors play across industries. As technology advances, the capabilities and applications of PE sensors are expected to expand, offering even greater precision and sensitivity for diverse uses.
Types of PE Sensors
Understanding the various types of Polymer Electrolyte (PE) sensors is crucial in grasping their capabilities and roles in many applications. Each type serves specific functions tailored to distinct measurement needs, while also presenting unique advantages and limitations. Developers, engineers, and researchers must carefully consider the intended application when selecting a particular sensor type. This attention to detail ensures the effectiveness of the technology in various environments and challenges.
Differential Pressure Sensors
Differential pressure sensors measure the difference in pressure between two points. This type is particularly vital in processes where knowing the pressure drop across a device, such as filters, valves, or pipelines, is necessary.
Applications:
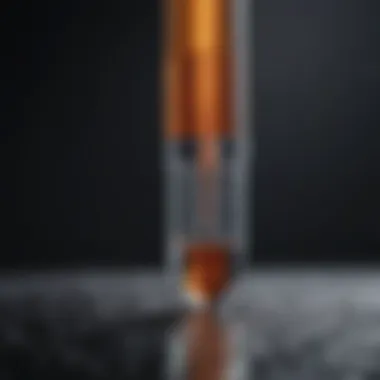
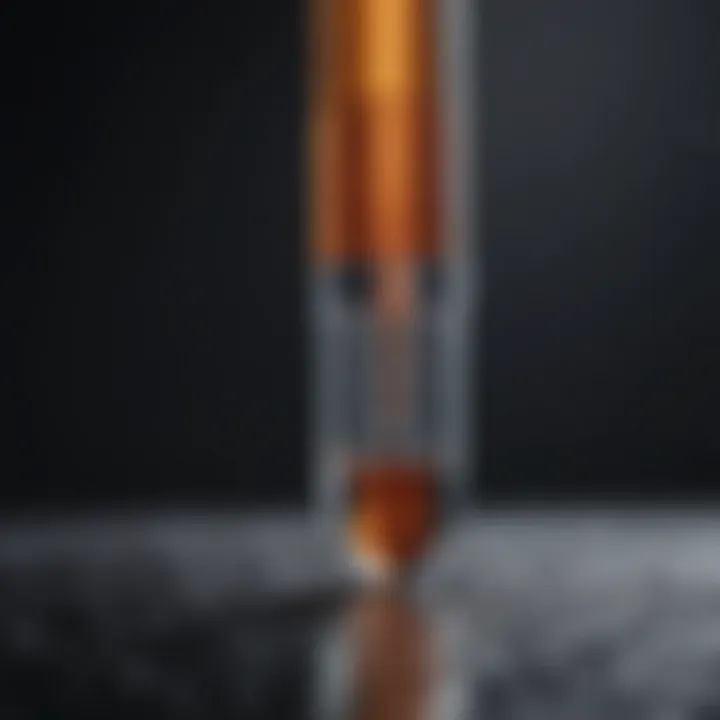
- Industrial Automation: These sensors help monitor fluid dynamics and optimize equipment performance.
- HVAC Systems: Keeping tabs on filters' condition or ductwork integrity can enhance system efficiency.
Such sensors operate based on specific design principles that translate mechanical deformation under applied pressure into an electrical signal. This function is fundamental in facilities that rely on maintaining precise pressure settings for operation.
"Differential pressure sensors are the unsung heroes in improving energy efficiency and system performance across numerous sectors."
Absolute Pressure Sensors
Absolute pressure sensors gauge pressure relative to a perfect vacuum. Unlike other types, they don't reference atmospheric pressure, making them highly accurate under varying environmental conditions.
Common Uses:
- Meteorology: These sensors are essential for weather stations, measuring atmospheric pressure changes.
- Aerospace: In these high-stakes environments, knowing the precise pressure is crucial.
Due to their inherent stability, absolute pressure sensors are often preferred in critical applications requiring high precision to ensure reliability and safety. Failing to account for absolute pressure can have significant consequences in various fields.
Vacuum Pressure Sensors
Vacuum pressure sensors measure pressures that are below atmospheric levels. They play an essential role in applications where maintaining a vacuum is critical, such as in semiconductor manufacturing or research laboratories.
Key Considerations:
- Semiconductor Industry: They monitor vacuum levels during production processes, crucial for product quality.
- Medical Devices: Vacuum sensors ensure safety standards are met during medical processes involving critical conditions.
The ability of vacuum sensors to accurately gauge low pressures has made them a standard solution in situations where avoiding contamination is paramount, directing their application in fields where minute pressures are routine.
Comparison with Other Sensor Technologies
In the realm of sensing technologies, Polymer Electrolyte (PE) sensors stand out, yet they are often juxtaposed against various other sensor types. This comparison is critical in understanding the unique advantages and limitations of PE sensors. As technologies evolve, recognizing how they compete or complement one another helps industries make informed choices based on specific applications and requirements.
The significance of comparing PE sensors with other sensor technologies cannot be overstated. Each sensor exhibits distinct traits that can either enhance or inhibit performance based on the operational environment and desired outcomes. In this section, we will break down the comparison of PE sensors with capacitive, piezoelectric, and resistive sensors, offering a nuanced understanding of each technology's unique characteristics.
PE Sensors vs. Capacitive Sensors
When we look at PE sensors, their strengths lie in sensing pressure without consuming too much power. Capacitive sensors, on the other hand, excel in measuring changes in capacitance caused by variations in pressure or displacement. Here are key points to consider when comparing these two technologies:
- Operating Principle: PE sensors measure pressure by detecting electrical properties that change as pressure is applied. Capacitive sensors measure the variation in capacitance due to the change in distance between conductive plates caused by pressure.
- Sensitivity: Capacitive sensors tend to offer higher sensitivity for minute changes, which is beneficial in applications needing precise measurements, like in touch-sensitive devices. PE sensors provide adequate sensitivity but may not match the granularity of capacitive options.
- Cost: In terms of production, PE sensors can often be less expensive to manufacture while still being reliable. Capacitive sensors, especially advanced designs, may carry a heftier price tag.
- Environment Adaptability: PE sensors are generally more robust in varied environmental conditions, including moisture and extreme temperatures, whereas capacitive sensors might struggle in such scenarios.
This comparison highlights that while capacitive sensors can provide extreme sensitivity, PE sensors offer a broader applicability in demanding environments.
PE Sensors vs. Piezoelectric Sensors
Now, stepping into the realm of piezoelectric sensors, this comparison showcases yet another layer of functionality.
- Operating Mechanism: While PE sensors rely on the movement of electrolyte fluid to establish pressure readings, piezoelectric sensors work on the principle of generating an electric charge in response to applied mechanical stress.
- Response Times: PE sensors typically have a slower response time compared to piezoelectric types, which can react almost instantaneously to changes in pressure. This makes piezoelectric sensors advantageous in dynamic applications, such as pressure shifts in industrial processes.
- Calibration and Maintenance: PE sensors generally require less calibration and are often seen as more user-friendly in terms of maintenance. On the contrary, piezoelectric sensors, although highly precise, can need frequent recalibration depending on their application.
"In the right context, both PE and piezoelectric sensors offer distinct advantages that cater to diverse industrial needs. Their unique operational characteristics ensure that choice should be informed by specific application requirements rather than perceived superiority."
Having evaluated these differences, it’s clear each sensor type occupies a niche and the choice hinges on factors like precision requirements, environment, and costs.
PE Sensors vs. Resistive Sensors
Finally, consider the relationship between PE sensors and resistive sensors. These sensors measure resistance changes when pressure is applied.
- Measurement Basis: Resistance-based sensing, as in resistive sensors, can be impacted by temperature fluctuations, affecting accuracy. On the other hand, PE sensors maintain stability against temperature changes, ensuring reliable readings across various conditions.
- Application Range: While resistive sensors find use in specific applications like load cells, PE sensors have a wider adaptability in areas ranging from medical monitoring to automotive pressure sensing.
- Durability and Lifespan: Typically, PE sensors can have a longer life cycle under harsh conditions than resistive types, which are more susceptible to wear and tear over time.
In essence, each sensor technology comes with its own set of strengths and weaknesses. The choice between them should be guided by a thorough evaluation of specific needs, including environmental factors, cost implications, and the critical nature of the required measurements. Understanding these contrasts allows industry professionals to harness the right sensor, optimizing both reliability and performance.
Advantages of PE Sensors
Understanding the advantages of PE sensors is crucial because it brings light to why they are increasingly favored in various applications. These sensors not only promise reliability but also enhance performance across diverse fields. In this section, we will dissect three pivotal advantages of PE sensors, each of which contributes to their growing popularity in modern technology.
High Sensitivity and Accuracy
One of the standout features of Polymer Electrolyte sensors is their high sensitivity and accuracy. This quality is paramount for precision in measurement, allowing these sensors to detect minute changes in pressure. For instance, in medical applications, even a slight fluctuation can indicate a critical change in patient health. The technology enables healthcare providers to respond swiftly, enhancing patient outcomes.
"In many cases, the difference between life and death can hinge on accurate pressure readings."
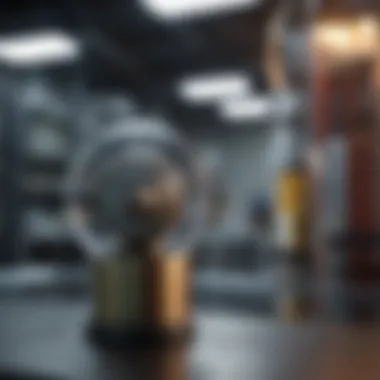
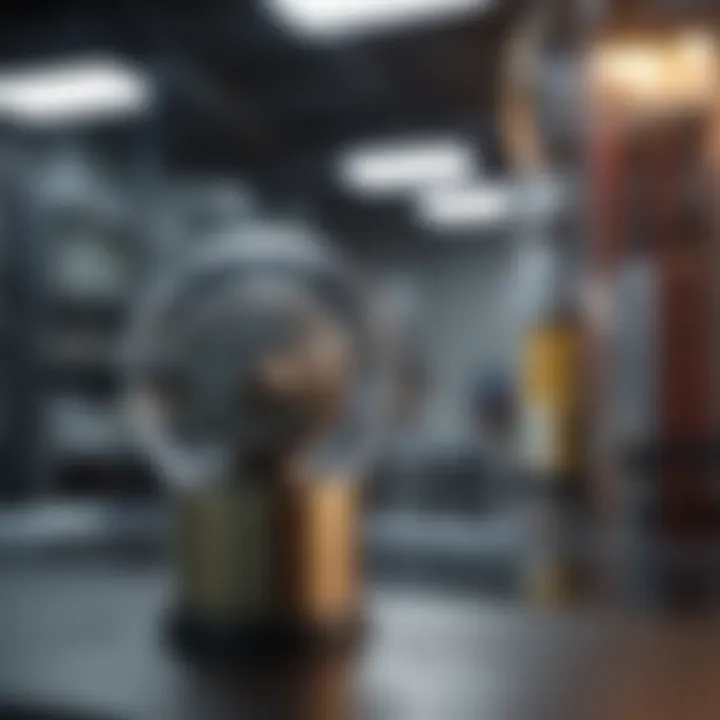
The mechanisms behind this high sensitivity are rooted in the umissible properties of the materials used in PE sensors. Their response time is noticeably quicker than many traditional sensors, leading to data that is both timely and reliable. As a result, industries like aerospace and automotive, where precision is non-negotiable, increasingly rely on these sensors for various systems, including flight control and engine performance monitoring.
Wide Range of Operating Conditions
Another significant advantage is the wide range of operating conditions in which PE sensors can function effectively. Whether subjected to extreme temperatures, humidity, or pressure levels, PE sensors tend to maintain operational integrity, setting them apart in comparison with other sensor types. This versatility is vital for industries that often face harsh environments, such as oil and gas exploration or environmental monitoring in varied climates.
For example, in an oil rig, sensors need to withstand high pressure and corrosive environments. PE sensors excel here, allowing for continuous monitoring while ensuring that equipment remains safe from catastrophic failures. This robustness is a testament to their engineering, making them suitable for demanding applications where failure is not an option.
Lightweight and Compact Design
Lastly, the lightweight and compact design of PE sensors cannot be overstated. This physical characteristic allows for easier integration into various systems without adding significant bulk or weight. For applications in smartphones and portable medical devices, every ounce counts. PE sensors can fit into tight spaces and are often lighter than their mechanical counterparts while maintaining high performance.
Innovations in miniaturization also mean that these sensors can be produced at scale, allowing for widespread adoption across consumer electronics. The convenience of having non-intrusive measuring devices not only enhances user experience but fosters the development of smarter products that require pressure measurement, from smartwatches to advanced health monitoring systems.
Disadvantages and Limitations
Understanding the disadvantages and limitations of Polymer Electrolyte (PE) sensors is crucial for a well-rounded assessment of their role in today's technological landscape. While these sensors present numerous advantages, it’s equally important to acknowledge their shortcomings. A balanced view allows researchers, engineers, and industry professionals to make informed decisions when integrating PE sensors into applications.
Temperature Sensitivity
PE sensors, while lauded for their exceptional sensitivity and accuracy, exhibit notable temperature sensitivity. This characteristic can be a double-edged sword. For instance, in environments with fluctuating temperatures, the performance of PE sensors may significantly deviate from expected readings. This sensitivity can be particularly problematic in applications like automotive systems, where extreme temperature variations are commonplace.
In practice, high temperatures can lead to expanded measurement errors, compromising data integrity. Conversely, at low temperatures, the response time can slow down, making these sensors less reliable in rapid-response applications. Designing systems that account for these variations is essential, but it adds an extra layer of complexity in sensor deployment. Therefore, engineers need to consider thermal compensation strategies to ensure optimal functionality of PE sensors in varying environmental conditions.
Cost Considerations
Cost poses another challenge when adopting PE sensors. Compared to traditional sensors, the price point for high-quality PE sensors can be on the higher side. This financial factor becomes vital in industries like consumer electronics, where profit margins can be thin. Embedding advanced PE sensors into low-cost devices may lead to budget constraints.
While the initial investment in high-precision sensors can yield benefits in terms of performance, the upfront cost often hampers their widespread adoption, especially in small-scale applications. Consequently, companies must evaluate the return on investment and weigh the advantages of enhanced accuracy against the cost implications. Finding cost-effective alternatives, or negotiating volume pricing with manufacturers, could mitigate this limitation. Despite this, some sectors may shy away from integrating PE sensors due to budget restrictions, impacting overall technological advancement.
Durability Issues
Durability remains an area of concern when utilizing PE sensors. In harsh environments—subject to moisture, chemicals, or physical strain—these sensors can face significant challenges. Unlike more robust sensor types, PE sensors are sometimes at risk of rapid degradation under extreme conditions. For example, exposure to corrosive substances can lead to a decrease in lifespan, affecting long-term reliability.
In industrial applications, where sensors are expected to endure tough environments, durability cannot be an afterthought. Implementing protective housings might provide a solution, but it can also complicate installation and increase costs. Thus, selecting PE sensors for demanding settings requires careful consideration and due diligence.
"In an environment where conditions can rapidly fluctuate, the lifespan and accuracy of your sensor dictate the success of your application."
Applications of PE Sensors
In today's fast-paced technological landscape, Polymer Electrolyte (PE) sensors play an increasingly pivotal role across various sectors. Their ability to accurately measure pressure and other physical parameters makes them indispensable in contexts requiring precision. Highlighting the applications of PE sensors not only sheds light on their versatility but also demonstrates the substantial benefits they bring to diverse fields like automotive, aerospace, medical devices, and consumer electronics. This exploration will delve into specific case studies and scenarios where PE sensors have made significant impacts, providing a clearer picture of their relevance and effectiveness.
Automotive Industry
One of the biggest arenas where PE sensors find their application is the automotive sector. In modern vehicles, pressure sensors are used for monitoring tire pressure, facilitating engine performance, and enhancing overall safety systems. Imagine a world where a car could alert you to low tire pressure before it becomes a safety hazard—this is made possible through the sheer reliability of PE sensors.
- Tire Pressure Monitoring Systems (TPMS): This system uses PE sensors to alert drivers when tire pressure falls below safe levels, thus preventing blowouts and improving fuel efficiency.
- Boost Pressure Regulation: In turbocharged engines, PE sensors measure the boost pressure, ensuring optimal performance and emissions control.
- Brake Systems: Some advanced braking systems utilize PE sensors to ascertain pressure levels for more effective braking mechanisms.
These advancements not only enhance safety but also contribute to energy efficiency, a vital aspect considering today’s environmental concerns.
Aerospace Engineering
In the aerospace industry, the reliability and accuracy of PE sensors are indispensable for ensuring the safety of aircraft. With such high stakes, every measurement must be precise.
- Altitude Measurement: PE sensors are essential for altimeters, which rely on accurate pressure readings to determine an aircraft’s altitude, aiding in navigation and operational safety.
- Cabin Pressure Control: Maintaining cabin pressure is crucial for passenger comfort and safety during flight. PE sensors help monitor and adjust pressure levels accordingly.
- Fuel Systems: In some cases, these sensors assist in fuel management by monitoring pressure within the fuel systems, ensuring efficient operation and reducing the risk of leaks.
As aircraft become more complex, the demand for such sensors increases, with companies constantly seeking out advancements for greater reliability.
Medical Devices
The medical field benefits greatly from PE sensor technology, pushing the boundaries of patient care. Their application is not limited to traditional methods, making them critical for innovation in medical devices.
- Blood Pressure Monitors: In devices that consistently track blood pressure, PE sensors provide precise measurements that are vital for diagnosis and treatment.
- Ventilators: PE sensors facilitate the measurement of pressure levels in respiratory equipment, ensuring accurate delivery of air and oxygen to patients.
- Wearable Health Devices: As personal health technology evolves, the use of PE sensors in wearables allows users to monitor their vital signs seamlessly, promoting preventative healthcare.
The mere presence of PE sensors in these devices exemplifies their core promise: improving patient outcomes and enabling better-informed healthcare decisions.
Consumer Electronics
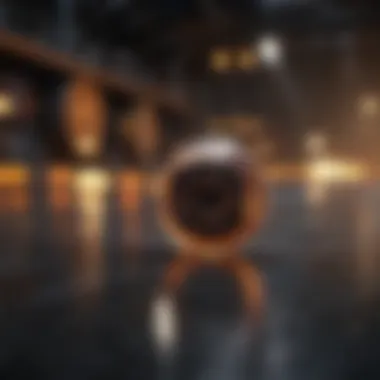
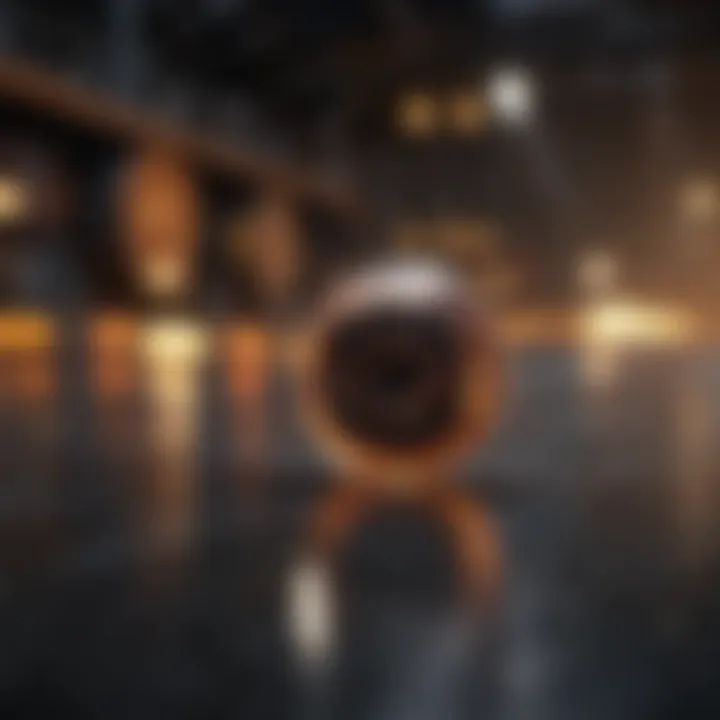
Consumer electronics is another realm where PE sensors have found their niche, merged with the growing trend toward smart technology. Devices are becoming increasingly interactive, and the integration of pressure sensors is a key component of this evolution.
- Smart Phones: Many smartphones now use PE sensors for functions like barometric readings, aiding applications that require altitude detection, such as fitness tracking.
- Home Automation Systems: PE sensors contribute to the operation of various smart home devices, allowing for better environmental controls—such as regulating heating or cooling based on pressure readings.
- Gaming Controllers: Some gaming devices use PE sensors to enhance user experience, providing feedback that makes interactions more immersive.
The integration of these sensors leads to more intuitive designs that take user experience to a whole new level, capturing the imagination of consumers and pushing the envelope in technology.
"Pressure sensors are often the unsung heroes of modern technology, working quietly in the background to ensure our devices perform optimally."
Trends in PE Sensor Technology
The landscape of Polymer Electrolyte (PE) sensors is shifting rapidly, driven by the integration of cutting-edge technology and the growing demand for precise, real-time data collection. As industries aim for increased efficiency and accuracy, it’s becoming inevitable for PE sensors to adopt novel trends that not only enhance their capabilities but also extend their practicality across various applications. The cetral focus here will be on the integration of the Internet of Things (IoT), advancements in materials science, and the miniaturization of devices.
Integration with IoT
In today’s hyper-connected world, IoT hasn’t just become a catchy buzzword; it’s genuinely transforming how we interact with everyday devices. When it comes to PE sensors, this integration holds significant weight. Imagine a smart factory where pressure sensors continuously communicate data to a centralized system. This data stream can facilitate real-time monitoring, predictive maintenance, and streamlined operations, ensuring everything runs smoothly without the usual hiccups.
Incorporating IoT with PE sensors allows for improved analytical capabilities. For instance, pressure readings can be analyzed over time to identify trends, helping in forecasting any potential issues that might arise. This proactive approach not only saves costs but also enhances the reliability of the systems. Moreover, the potential for remote monitoring enhances convenience, allowing technicians to access critical data from anywhere, thereby reducing the need for on-site visits.
Advancements in Materials Science
Materials science is the backbone of sensor technology—especially for PE sensors that utilize polymer substrates. Recent advancements in this field have paved the way for developing more efficient, durable, and adaptable sensors. Innovations include using nanomaterials to enhance sensitivity or utilizing conductive polymers to improve the electrical characteristics of sensors.
Such improvements can translate into a variety of benefits. For example, sensors made with advanced materials could operate effectively under extreme conditions—whether it’s high temperatures in industrial applications or variable humidity levels in medical devices. This versatility means PE sensors can serve a broader range of industrial needs.
"The next generation of PE sensors is evolving due to the material advancements, leading towards improved functionalities and performance capabilities."
Miniaturization of Devices
As technology progresses, there's a constant push for making devices smaller yet more powerful. This trend is no different for PE sensors. Miniaturization allows these sensors to be integrated seamlessly into compact systems without compromising on accuracy or functionality. Think of medical applications where space is a premium, or in consumer electronics where devices need to maintain sleek designs.
The benefits of smaller, more compact sensors are manifold. They require less energy, making them more suitable for battery-operated devices. Furthermore, reduced size often means reduced cost in terms of materials and manufacturing. This gives manufacturers a competitive edge, allowing for quicker production and adaptation to market demands.
In summary, the trends in PE sensor technology reflect a seamless blend of innovation and practicality that aligns with the ever-evolving requirements of various industries. The ongoing integration with IoT, significant strides in materials science, and relentless quest for miniaturization strive to enhance performance while ensuring PE sensors remain at the forefront of technological advancements.
Future Prospects
As we gaze into the horizon of technology, the future of Polymer Electrolyte (PE) sensors holds promising potential. These sensors not only work as essential tools for measurement and control but also act as catalysts for innovation across various industries. Understanding this potential is crucial for stakeholders ranging from researchers and developers to product manufacturers looking to gain a competitive edge.
One of the most significant aspects of the future prospects of PE sensors lies in their adaptability within rapidly evolving technological landscapes. With the integration of advanced materials and smart technologies, the robustness and precision of these sensors are set to improve.
Emerging Research Directions
The path for advancement in PE sensor technology is rife with intriguing research directions. A few noteworthy areas of focus include:
- Nanotechnology: By incorporating nanomaterials, researchers aim to enhance the sensitivity and response times of sensors. This could lead to more precise measurements in applications ranging from environmental monitoring to healthcare.
- Biocompatibility: Research into creating bio-compatible PE sensors is increasing, catering to the medical field's need for devices that can interface safely with human tissue for diagnostics and therapeutic purposes.
- Wireless Technology Integration: The development of wireless PE sensors can potentially revolutionize data collection in hard-to-reach areas, making monitoring more efficient and less intrusive.
- Smart Materials: There is a push to develop PE sensors that can autonomously adjust to their environment, enhancing their applicability in dynamic conditions.
In each of these directions, the emphasis is on improving performance while keeping costs manageable. Thus, it’s not just about finding new uses for PE sensors but also making them more accessible for a variety of applications.
Challenges Ahead
Despite the promising outlook, several challenges could impede the growth and integration of PE sensors into mainstream applications. Some primary concerns include:
- Cost of Raw Materials: The materials needed for high-performance PE sensors can be expensive. This cost factor could be a barrier for smaller companies or start-ups wanting to innovate in this space.
- Technical Limitations: While PE sensors boast many advantages, they also face issues like temperature sensitivity and short life spans in certain conditions, which must be addressed through ongoing research and development.
- Market Competition: The field is becoming crowded with various sensor technologies vying for dominance. PE sensors will need to differentiate themselves clearly to capture and retain market share.
Overall, while the future of PE sensors appears bright, navigating the landscape of challenges is crucial for realizing their full potential. Stakeholders must invest time and resources into addressing these challenges, positioning themselves favorably in an ever-changing market.
The End
In wrapping up our discussion on Polymer Electrolyte (PE) sensors, it is crucial to recognize their significance in today’s technological landscape. These sensors integrate seamlessly into various applications, paving the way for more accurate and reliable measurements. As industries evolve and adapt, the role of PE sensors becomes exemplary in ensuring safety and efficiency.
Summary of Key Insights
- Versatile Applications: PE sensors find use across numerous sectors, such as automotive, aerospace, and medical. Their adaptability allows engineers to design smarter systems tailored to the specific demands of each field.
- Operational Efficiency: Through their ability to measure pressure with high accuracy, these sensors contribute significantly to the functionality of electronic devices. Imagine the precision involved in automotive safety systems or medical devices needing unerring measurements at critical moments.
- Innovation Drive: Advances in materials science and technology herald a new chapter for PE sensors. Enhanced performance attributes mean that their deployment is not just limited to existing applications but extends to emerging fields with complex requirements.
- Environmental Considerations: PE sensors are now being integrated into systems that monitor environmental parameters closely. Their ability to provide reliable data aids initiatives in climate studies and pollution control which are paramount today.
- Future Trajectory: The synergy between PE sensors and Internet of Things devices promises an exciting highway for technological advancement. This confluence hints at devices that can communicate pressure data in real-time, refining processes that aim for optimal performance.
"As we look to the horizon, Polymer Electrolyte sensors are not just paving the way—they are redefining what precision means in the digital age."
Importance of Continued Research
The field of PE sensors is ripe for exploration and could benefit significantly from ongoing research. Investing time and resources here can lead to breakthroughs that elevate sensor technology into unprecedented realms.
Some key areas demanding attention include:
- Enhancing Durability: Understanding the long-term behavior of these sensors under various conditions can help improve their lifespan and reliability.
- Cost Reduction: As technology progresses, finding ways to lower the production costs while maintaining quality could open doors to wider applications.
- Interdisciplinary Approaches: Collaborative research that combines insights from fields like nanotechnology and materials science may yield smarter, more effective PE sensor designs.
- Regulatory Standards: With more applications in sensitive environments, there’s an urgent need for establishing industry-wide protocols and standards that govern the use of PE sensors.
Conclusively, while we've touched tangentially on various aspects of PE sensors, the horizons promise much innovation. Each advancement not only shapes the future of technology but also contributes to broader societal goals, making this an exciting domain with vast possibilities.