Exploring Aluminium Injection: Key Processes and Trends
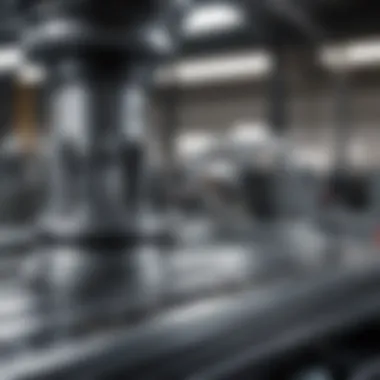
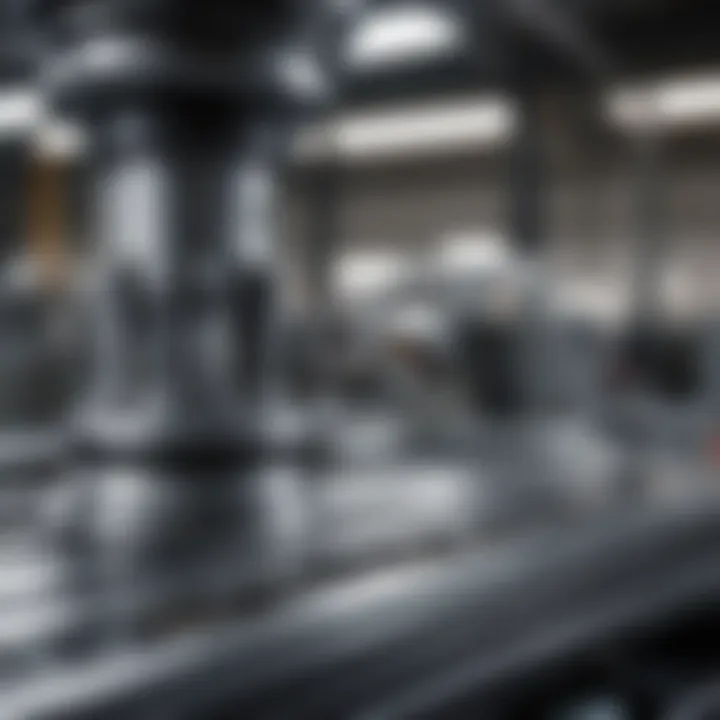
Intro
Aluminium injection molding stands as a keystone in the realm of manufacturing, symbolizing not just a technique but a blend of science and art. This method has transformed the way industries approach production, offering a cost-effective and efficient means to create complex shapes and components that are lightweight yet durable. The very properties of aluminium, such as its resistance to corrosion and high thermal conductivity, have made it a favored material in sectors ranging from automotive engineering to consumer electronics.
The core of this article aims to dissect the aluminium injection process while shedding light on its myriad applications and the innovations that propel it forward. As industries evolve, so too does the demand for materials and processes that meet stringent performance requirements. Aluminium injection fits snugly within this narrative, making it an essential topic for students, researchers, educators, and professionals alike.
To clarify the landscape, we will begin with an overview of key findings and their relevance to ongoing discussions in the field. This will provide a backdrop for understanding the importance of this manufacturing technique in today's fast-paced environment.
Prelims to Aluminium Injection
Aluminium injection has become a cornerstone in modern manufacturing, playing a vital role across various industries. This section introduces readers to the intricate world of aluminium injection, shedding light on its significance, processes, and wide-ranging applications. By unpacking how aluminium injection works, one can better appreciate its relevance in todayās fast-paced production environments.
Definition and Overview
Aluminium injection refers to a method of manufacturing where molten aluminium is injected into a mold to create precise components. The process involves melting the metal, then forcing it into a prepared mold cavity under high pressure. This method allows for intricate designs and complex shapes that might not be achievable through traditional casting methods. Essentially, aluminium injection enables the creation of lightweight and strong parts, a vital characteristic in sectors such as automotive, aerospace, and electronics.
The efficiency of aluminium injection stands out, as it generally reduces waste and shortens production times, making it an attractive option for manufacturers striving for both quality and economical production.
Historical Context and Development
The roots of aluminium injection go back to the mid-20th century, when industries began to realize the potential of aluminium as a material. Initially, the focus was on conventional casting techniques, but limitations soon became apparent, leading to the need for more innovative manufacturing methods. By the late 1950s, experiments in high-pressure die casting laid the groundwork for modern aluminium injection techniques.
As understanding of the materials' properties evolved, so too did the technology surrounding its injection. Machinery became more sophisticated, enabling tighter tolerances and enhanced surface finishes, which in turn opened up new possibilities in application areas like automotive engines and high-precision electronic enclosures.
With technology continuing to advance, developments in the process have made aluminium injection more appealing than ever.
The evolution of aluminium injection is a testament to how industry adapts and innovates in response to material advancements and design demands.
However, itās worth noting that the path hasnāt always been smooth. Initially expensive and complex, the equipment needed for effective aluminium injection limited its use to only larger, resource-rich companies. Over time, competition has driven costs down while improvements in technology have made the process more accessible to smaller manufacturers.
As we continue to explore aluminium injection, understanding the technicalities of the process along with its historical journey offers valuable insights into why this method has become a mainstay in modern manufacturing.
The Aluminium Injection Process
The aluminium injection process stands at the core of modern manufacturing, providing a method to produce intricate and high-quality parts across various industries. This process not only facilitates efficiency in production but also ensures versatility in design, leading to widespread adoption. By examining the techniques and machinery involved, one gains a clearer perspective on how this method streamlines operations and enhances productivity. The significance of mastering the aluminium injection process can't be overstated, especially in an ever-evolving industrial landscape. It supports innovative designs, addresses market needs, and ultimately shapes the future of manufacturing.
Techniques of Injection
When it comes to the techniques used in aluminium injection, each has its unique set of characteristics, benefits, and applications. Hereās a closer look:
Die Casting
Die casting is a well-established method that involves forcing molten aluminium into a mold at high pressure. This technique is prized for producing parts with smooth surfaces and fine details, making it a go-to choice in sectors requiring precision, like automotive and electronics.
One key characteristic of die casting is its ability to create complex geometries with high dimensional accuracy. Because the process allows for rapid cooling, it's also capable of producing components quickly, which is beneficial in high-volume production runs. However, the initial costs for the molds can be pretty steep, which may deter small-scale producers.
Vacuum Die Casting
As the name suggests, vacuum die casting introduces a vacuum into the process, helping eliminate air from the molten aluminium before it enters the mold. This method excels in reducing defects such as porosity, resulting in stronger and more reliable parts.
The unique feature of vacuum die casting lies in its capacity for producing high-integrity components that resist cracking and bending, which is crucial in high-stress applications like aerospace. While its setup may require more investment, the resulting quality and reduced rework can lead to cost-effectiveness in the long run.
Low-Pressure Die Casting
Low-pressure die casting, in contrast, relies on gas pressure to propel the molten aluminium into molds. This technique offers superior control of the filling process and results in better surface finish compared to traditional methods.
This techniqueās distinguishing benefit is its ability to produce lightweight yet robust components, making it a favorite in industries where weight reduction is critical. However, the cycle times can be longer, which may not favor industries needing extremely fast turnaround times.
Machinery and Equipment
The machinery and equipment utilized in aluminium injection play a vital role in determining the quality and efficiency of the production process. Understanding the different components is crucial for anyone involved in or studying this field.
Injection Machines
Injection machines are the heart of the aluminium injection process. They are designed to handle the molten metal at varying temperatures and pressures. A significant benefit of modern injection machines is their versatility; they can accommodate different types of materials and shapes, allowing manufacturers to optimize their production lines.
The unique focus on automation and precision in these machines enhances overall productivity and reduces human error. However, reliance on advanced technology may necessitate additional training and ongoing maintenance costs.
Heating Systems
Heating systems are critical as they maintain the appropriate temperature for melting aluminum. Good thermal control ensures consistent quality in production. Many facilities now employ advanced heating systems that offer energy savings while maintaining reliability in operation.
One of the key advantages of modern heating systems is their ability to minimize energy losses, which not only cuts down production costs but also lessens the environmental impact. However, upfront expenses can be a concern for startups entering the market.
Casting Dies
Casting dies are the molds used for shaping the molten aluminium as it cools and solidifies. The design and material of these dies dictate the final dimensions and surface finish of the products being manufactured.
An important characteristic of casting dies is their durability, which allows them to withstand high-temperature and high-pressure conditions over prolonged periods. Creating high-quality dies requires skilled craftsmanship, as errors can lead to significant cost overruns due to rejection rates in production. Yet, their long lifespan can make them a worthwhile investment.
"Understanding the nuances of each technique and the machinery involved in aluminium injection can prove invaluable for industry players aiming to optimize costs and improve product quality."
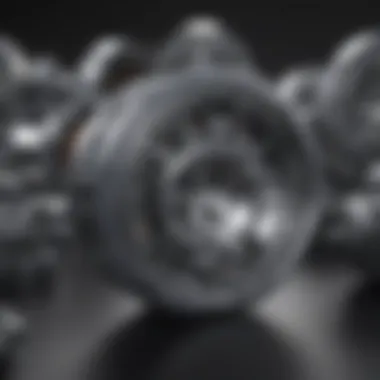
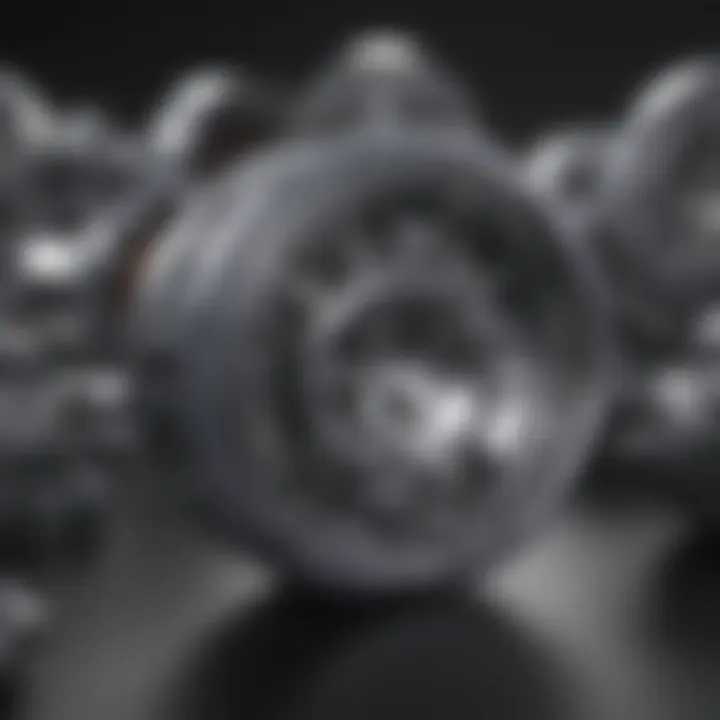
In summary, the aluminium injection process encompasses a range of techniques and machinery, each tailored for specific applications and requirements. By choosing the appropriate methods and the right equipment, manufacturers can effectively navigate the complexities of modern production while meeting the ever-evolving demands of the market.
Material Properties of Aluminium
The material properties of aluminium play a pivotal role in its popularity across various industries. These properties not only influence the effectiveness of aluminium injection but also shape the applications it can be employed for. Understanding these characteristicsāespecially the physical and mechanical aspectsāprovides valuable insights into why aluminium is a material of choice in manufacturing.
Physical Characteristics
Weight and Density
When it comes to the weight and density of aluminium, it's important to note its lightweight nature. Aluminium weighs about one-third that of steel. This characteristic is particularly beneficial in industries like automotive and aerospace, where reducing weight is directly tied to fuel efficiency and performance.
The key feature of weight and density in aluminium is its strength-to-weight ratio. This makes aluminium a desirable option for manufacturers looking to create strong yet lightweight components. For instance, in the automotive sector, using aluminium helps minimize vehicle mass without sacrificing structural integrity.
One unique advantage of this low density is its ease of handling during production. This does, however, come with a disadvantage; lighter materials can sometimes be perceived as less durable. But advancements in technology have largely mitigated these concerns, allowing aluminium to meet the rigorous demands of various applications.
Thermal Conductivity
Aluminiumās thermal conductivity is another crucial aspect, especially in applications involving heat management. The metal exhibits excellent thermal conductivity, which allows for effective heat dissipation in electronic components, automotive engines, and other equipment exposed to high temperatures.
This is significant for thermal conductivity because it prevents overheating and facilitates optimal performance in critical situations. A unique feature here is that, when used in electronics, it can enhance energy efficiency and prolong device lifespan. Nonetheless, the downside is that this high conductivity can sometimes create challenges in insulation when designing products meant to conserve heat.
Corrosion Resistance
Corrosion resistance is an indispensable property of aluminium, achieved primarily through its natural oxide layer. This barrier develops when aluminium is exposed to oxygen, protecting it from corrosive environments. In sectors like construction and transportation, this property is invaluable since it ensures longevity and reduces maintenance costs.
The most remarkable feature of corrosion resistance lies in its effectiveness in various conditions, including acidic and alkaline environments. Many industries prefer aluminium due to its ability to resist rust, placing it as a preferred material for outdoor applications. Nevertheless, it is worth mentioning that while this protective layer is strong, it can be compromised if the aluminium surface is scratched or damaged.
Mechanical Properties
Strength and Hardness
The strength and hardness of aluminium alloys are vital for structural applications. While aluminium is not as strong as steel, certain alloys can offer remarkable strength, making it suitable for demanding applications. For example, alloy 7075 is widely used in aircraft due to its impressive strength.
A key characteristic here is the versatility of aluminium; it can be treated and alloyed to enhance its strength displays. This feature benefits industries where high-performance materials are required, though process adjustments and careful selection of alloy types can lead to variations, potentially complicating production.
Elasticity and Ductility
Elasticity and ductility are crucial when considering how materials behave under stress. Aluminium is known for its good ductility, which means it can be easily shaped and formed without breaking. This capability allows for intricate designs and complex shapes, particularly in die casting applications.
The unique aspect of elasticity and ductility in aluminium grants manufacturers the ability to fabricate parts with tight tolerances. However, this flexibility can occasionally lead to deformation under heavy loads, posing a challenge in specific applications where rigidity is paramount.
Tensile and Yield Strength
Finally, the tensile and yield strength of aluminium is fundamental in ascertaining how much force a material can withstand before permanent deformation occurs. Generally, aluminium exhibits lower yield strength compared to heavier metals like steel. However, its alloys can boast impressive tensile strengths that compete with many higher-density materials.
The notable feature of tensile and yield strength is its relevance, especially in the context of safety in design criteria. For instance, in aerospace, understanding these values is pivotal for ensuring the reliability of every component. Yet, itās important to balance strength with weight, leading to the potential compromise in material performance based on application needs.
Advantages and Challenges
In examining aluminium injection as a crucial manufacturing technique, itās essential to discuss both its advantages and its challenges. Understanding these two sides is fundamental, as they impact various facets of production, design, and environmental considerations. When companies or individuals weigh the options for using aluminium injection, they must consider not just the benefits but also the potential hurdles. This section delves into these elements to give a well-rounded view of what aluminium injection can offer and what issues might arise.
Benefits of Aluminium Injection
Cost Efficiency
Cost efficiency is often the first point of discussion around aluminium injection. This feature allows manufacturers to save money while still achieving high-quality results. Products can be designed and produced without excessive waste, effectively reducing material costs. Another point to consider is that, compared to other metals, aluminium itself is relatively inexpensive and readily available.
With lower production costs and the potential for bulk purchasing, businesses can see significant savings in their bottom lines. The unique aspect of this cost efficiency is its compounded nature; savings on material expenses can also translate to savings on labor costs due to quicker production times compared to other methods.
- Benefit: Reduced waste leads to lower overall costs.
- Potential downside: Initial investment in machinery can be steep.
Speed of Production
When it comes to speed, aluminium injection shines bright. The quicker turnaround time means that products can reach the market faster, giving companies a competitive edge. With advanced technologies, production can happen in larger batches without sacrificing precision, thereby improving the overall throughput of manufacturing.
This particular aspect allows for rapid prototyping and quick adjustments, which are vital in industries that thrive on innovation and change. But, as with everything, there's a flip side. The rapid pace may lead to rushed decisions that could compromise quality.
- Strength: Faster production enhances market responsiveness.
- Drawback: Speed may risk errors if not monitored properly.
Design Flexibility
Design flexibility is another cornerstone advantage of aluminium injection. It allows for intricate, complex shapes that wouldnāt be feasible with other manufacturing methods. This opens up a world of opportunities in product design, letting engineers create components that are not just functional, but aesthetically pleasing as well.
The ability to mold aluminium quickly into specific shapes can also facilitate unique applications across diverse sectors, from consumer goods to aerospace. However, this flexibility may come at a cost, as more intricate designs can require more sophisticated equipment and higher initial design investments.
- Advantage: Enables innovation and creativity in product design.
- Complication: More complex designs can drive up initial costs.
Challenges Faced
Environmental Concerns
One of the pressing challenges today is environmental concerns surrounding aluminium injection. The entire process has a notable impact on sustainability, particularly concerning emissions and energy usage. The production of aluminium typically involves energy-intensive processes, which can contribute to greenhouse gas emissions.
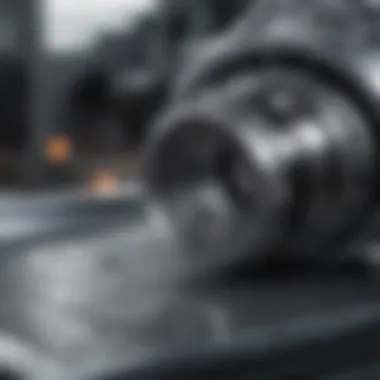
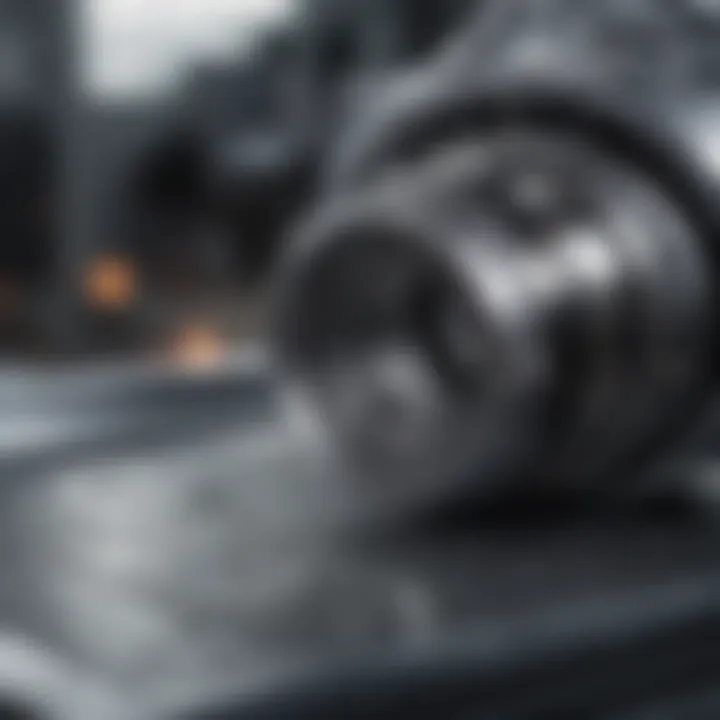
In addition, recycling aluminium can also be challenging. Even if the raw material is recyclable, the energy costs linked to remelting toughen the sustainability angle. Thereās hope, however, with ongoing innovations, but the issue remains a significant consideration.
- Concern: Significant energy consumption during production.
- Opportunity: New sustainable practices are being developed.
Material Limitations
Aluminium does have its share of material limitations, which can be a hurdle in its injection applications. For starters, the metal can be less durable compared to others like steel. While aluminium has great lightweight characteristics, it may not always hold up under extreme stress or conditions, leading to considerations of potential replacement or reinforcement.
These limitations might pose challenges for industries requiring super high-performance materials, forcing them to weigh the pros and cons of choosing aluminium over other metals. Sometimes the benefits simply donāt outweigh the necessary performance requirements, particularly in critical applications such as aerospace or heavy machinery.
- Limitation: Weaker under high stress compared to some alternatives.
- Solution: Use of alloys or layered materials can mitigate this issue.
Quality Control Issues
Finally, quality control is a prevalent challenge in the aluminium injection process. Ensuring consistent quality across batches can be a battle. Given the complexity involved in machinery and process settings, even slight variations can lead to defects or inconsistencies in the final products.
Moreover, factors like temperature, pressure, and cooling times must be meticulously monitored. If not, the overall quality can suffer, creating a ripple effect that impacts not just production costs but also customer trust. Effective quality control systems and regular testing become indispensable tools to tackle these challenges.
- Issue: Variations in production can result in inconsistencies.
- Strategy: Implementation of rigorous quality checks to ensure standards.
Applications of Aluminium Injection
Aluminium injection plays a significant role in various industries, fundamentally shaping their manufacturing processes. By leveraging the unique properties of aluminium, tasks that once required extensive time and resources are streamlined. From automotive to aerospace, the applications are vast and impactful. This section delves into the specific uses of aluminium injection across different sectors and highlights its immense benefits and considerations that come with it.
Automotive Industry
Engine Components
The production of engine components through aluminium injection is paramount, as it combines strength with lightweight properties. Automotive manufacturers utilize aluminium for engine parts, such as cylinder heads and blocks. One key characteristic of these components is their ability to withstand extreme temperatures while maintaining structural integrity. This makes aluminium-based engine components a wise choice for ensuring performance and durability.
A distinct advantage of utilizing aluminium is the reduction in weight without compromising on strength. This leads to better fuel efficiency, as lighter engines require less power. However, one disadvantage is that while aluminium can handle heat, it may have issues with thermal expansion compared to steel, potentially affecting engine performance over time.
Chassis and Body Parts
When it comes to chassis and body parts, aluminium injection shines brightly. The primary appeal lies in its superior strength-to-weight ratio which provides robustness while ensuring lower overall vehicle weight. This substantially contributes to improved vehicle dynamics and fuel efficiency.
A notable feature is the ease of shaping aluminium into complex designs, which is essential for modern automotive aesthetics and aerodynamics. While these benefits are significant, manufacturers must be cautious of possible corrosion issues, particularly when exposed to certain environmental conditions.
Lightweight Design Solutions
In the quest for innovation, lightweight design solutions have emerged as a game changer in the automotive world. Aluminium injection technology facilitates the creation of parts that not only meet stringent safety and performance requirements but also drive down energy consumption.
The lightweight nature of these solutions allows for explosive advancements in electric vehicles where every kilogram saved leads to extended range. However, the challenge lies in achieving the necessary strength and rigidity, especially for safety-critical components.
Consumer Electronics
Smartphone Casings
Aluminium is increasingly favored in the manufacturing of smartphone casings. The main aspect here is its sleek design and ability to maintain structural integrity under stress. This not only appeals to the aesthetics of modern devices but also offers durability against drops and scratches.
Smartphone casings crafted from aluminium provide excellent heat dissipation, a crucial feature for high-performance devices that may overheat during extensive use. On the downside, aluminium can be more costly compared to plastics, which might affect pricing strategies for some brands.
Laptop Frames
Laptop frames made of aluminium offer an exquisite blend of style and durability. A defining characteristic of these frames is their lightweight nature, which contributes to the overall portability of the devices, a feature highly valued by users today.
Aluminium frames, while they add a premium touch, can sometimes be susceptible to dents and dings. Balancing the aesthetics with usability is paramount for manufacturers in this competitive sector.
Component Housing
In consumer electronics, component housing constructed from aluminium serves critical roles. They enhance the appearance of devices while ensuring protection against impacts and external damage. Its ease of production also means manufacturers can produce intricate designs without running into issues typical of other materials.
One unique feature of aluminium as a housing material is its ability to be anodized, adding a layer of protection and design flexibility. However, it requires careful handling during manufacturing to avoid defects that could compromise the electronic components housed within.
Aerospace Sector
Structural Components
In the aerospace industry, structural components made from aluminium injection are indispensable. Their light weight, combined with high tensile strength, enables engineers to design aircraft that are both efficient and capable of withstanding rigorous conditions. This choice significantly contributes to fuel savings due to reduced overall mass.
A unique aspect of these components is their capacity for precision engineering, allowing for intricate shapes and forms critical to aerodynamic efficiency. The downside, however, is the high cost associated with these specialized materials.
Weight Reduction Techniques
Adopting weight reduction techniques in aircraft design is beyond essential; it is life-saving. Techniques using aluminium injection are at the forefront, enabling manufacturers to reduce weight while maintaining safety and performance standards. This is pivotal in enhancing fuel efficiency and operational range for commercial and military aircraft.
An important characteristic of these strategies is their reliance on computational simulations to predict performance under various loads, which fosters innovation. A drawback includes stringent testing processes that can delay production schedules.
High-Performance Part Applications
High-performance part applications in aerospace are where aluminium injection really flexes its muscles. Itās crucial for creating parts that need to resist extreme stresses, such as those found in jet engines. The strength and thermal stability of aluminium allow for designs that push the limits of currently achievable performance.
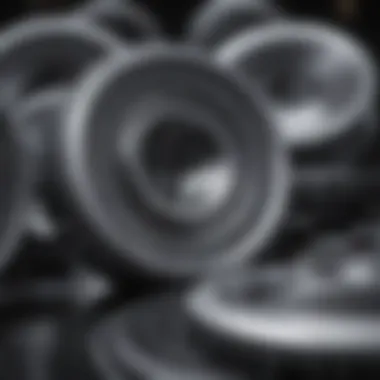
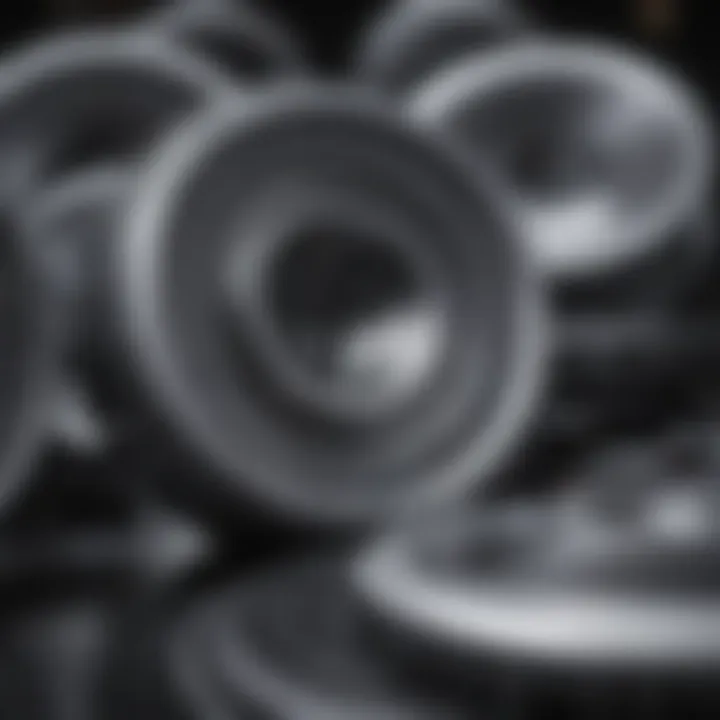
One standout feature of these parts is their ability to be tailored for application-specific demands, enhancing safety and function. The tradeoff, however, involves navigating complex regulations and standards that can be quite challenging for new entrants to the market.
Overall, the applications of aluminium injection technology underscore its versatility, catering to diverse needs across different industries. Key benefits include improved efficiency, weight reduction, and the ability to manufacture complex shapes. However, companies must remain vigilant to challenges such as cost, strength limitations, and environmental impacts in their operational strategies.
Innovations in Aluminium Injection Technology
The evolution of aluminium injection has significantly benefited from ongoing innovations in technology. These advancements are not just a trend; they play a pivotal role in enhancing efficiency, productivity, and sustainability in manufacturing processes. Through better machinery and emerging trends, the industry is positioning itself to meet future demand while addressing pressing environmental concerns. Innovations in this field are crucial not only for existing applications, but also for potential new uses that can emerge with improved techniques.
Advancements in Machinery
Automation and Robotics
The integration of automation and robotics stands out as a game changer in the aluminium injection landscape. This shift allows for greater precision in the injection process, reducing human error and enhancing consistency. One key characteristic of automation is its ability to operate 24/7, thus maximizing output without the need for breaks. This constant production cycle can lead to significant cost savings in the long run.
"Automation is to manufacturing what the wheel is to transportation; it transforms the efficiency of the process."
Moreover, robotics introduces flexibility. It can swiftly adapt to changes in product designs without significant downtime. However, the initial investments for automated machinery can be substantial, and it requires a workforce skilled in operating and maintaining these advanced systems.
Energy Efficiency Improvements
Energy consumption is a critical concern in manufacturing, and improving efficiency in this area is a primary focus for many companies. Upgrading heating systems and optimizing the injection process can yield significant energy savings. One of the standout features of energy-efficient machinery is their ability to use less electricity while maintaining production rates.
This represents a cost-effective approach for manufacturers, not only reducing operational expenses but also aligning with global sustainability efforts. Still, the transition to energy-efficient solutions may involve upfront costs and require a recalibration of existing processes.
Smart Manufacturing Technologies
Smart manufacturing technologies have revolutionized how aluminium injection is viewed. They provide real-time data analytics, allowing for immediate adjustments to the production process based on specific metrics. A remarkable feature of smart technologies is their predictive maintenance capability, which can anticipate machinery failures before they occur. This is beneficial as it minimizes unexpected downtimes and upkeep compromises.
The integration of Internet of Things (IoT) within manufacturing facilitates seamless communication between machines, enabling a more streamlined workflow. However, incorporating these advanced systems requires not only financial investment but also a cultural shift in how the workforce interacts with technology in the workspace.
Emerging Trends
Sustainability Efforts
The industrial sector faces increasing scrutiny regarding its environmental impact. Sustainability efforts are becoming paramount in aluminium injection, focusing on reducing waste and carbon footprints. A central aspect of these efforts involves adopting eco-friendly processes and materials. The push for sustainable practices benefits both the environment and companiesāthose that prioritize sustainability are often viewed more favorably by consumers.
However, the challenge remains to balance sustainability with cost and productivity. While implementing greener solutions may initially be expensive, they can lead to long-term gains and improved public perception.
Recyclability of Aluminium
Recyclability plays a critical role in the lifecycle of materials in the manufacturing industry. Aluminium is one of the most recyclable materials available, making it an exceptionally appealing choice for manufacturers. A distinctive feature of aluminium is that it retains its properties even after multiple recycling processes. This characteristic not only reduces resource consumption but also minimizes waste.
The advancement in recycling technology can further enhance the efficiency of reusing aluminium, creating a circular economy. However, the industry's challenge lies in establishing a robust infrastructure that supports extensive recycling initiatives.
Innovative Alloys
The development of innovative alloys has opened new avenues in aluminium injection. These alloys are designed to offer superior strength while maintaining lightweight characteristics, which is particularly important in sectors like aerospace and automotive. Their unique feature often includes resistance to extreme conditions, which traditional aluminium may not withstand.
The application of these alloys can improve overall product performance considerably. But, on the downside, developing these materials may involve more research and development investments before they can be commercially successful.
Innovations in aluminium injection not only emphasize the industry's movement toward efficiency and sustainability; they also lay the groundwork for future advancements that can redefine manufacturing. As new technologies emerge, they will reshape practices, enabling adjustments that respond to both consumer demands and environmental responsibilities.
Future Prospects in Aluminium Injection
The domain of aluminium injection holds immense promise for the future, driven predominantly by advancements in technology and a growing industrial demand. Understanding the potential trajectories of aluminium injection is crucial for industry stakeholders. This section explores the landscape ahead, highlighting the expected growth, new applications, and the evolution of the technology itself.
Market Demand and Growth
The market for aluminium injection is on an upward trajectory, reflecting broader trends in global manufacturing and consumer preferences. The lightweight, durable nature of aluminium allows for efficiency in various applications, making it a sought-after material. Factors contributing to this rising demand include:
- Sustainability Initiatives: Companies increasingly focus on reducing carbon footprints, and aluminiumās recyclability plays a pivotal role. It can be reprocessed without losing its desirable properties.
- Automotive Industry Expansion: With the shift towards electric vehicles, manufacturers are seeking lightweight materials to enhance performance and reduce energy consumption. Aluminium injection is perfectly positioned to meet this need.
- Consumer Electronics Growth: The surge in demand for tech gadgets continues to favor aluminium due to its modern aesthetic and protective features.
Projections indicate significant growth in the aluminium injection market over the next decade. Analysts believe that reaching new heights in production capacities and process efficiencies will be essential. Innovations in machinery can help meet this escalating demand, ushering in a new era of aluminium manufacturing.
Potential Applications on the Horizon
As the technology behind aluminium injection evolves, so do the types of applications that leverage its advantages. The following areas show keen potential:
- Health and Medical sectors: As industries seek lighter materials for medical devices and equipment, aluminiumās corrosion resistance and strength can contribute greatly.
- Building and Construction: The demand for sustainable and efficient building materials might lead to aluminium being utilized more frequently for infrastructural projects, particularly in facade systems and structural components.
- Aerospace Innovations: The aerospace sector is always on the lookout for ways to minimize weight while maintaining safety. Aluminium injection can facilitate the production of intricate components that adhere to strict regulatory standards.
The infusion of technology like artificial intelligence and smart manufacturing practices also hints at a future where aluminium injection is more efficient and adaptable. Machine learning can lead to enhanced quality control, reductions in waste, and streamlined operations.
"The future of aluminium injection is not merely about maintaining current standards; itās about setting new benchmarks for what is possible in manufacturing and sustainability."
Culmination
Wrapping up our journey through aluminium injection, it's evident that this manufacturing process stands at a significant intersection of efficiency and versatility. The importance of understanding the intricacies of aluminium injection cannot be overstated, especially given its profound impact across myriad industries. The insights provided throughout this article stress the necessity of comprehending not only the mechanisms of injection but also the material properties that make aluminium a leading choice among manufacturers.
Summary of Key Insights
In summarizing the key insights we've explored, we note that aluminiumās propertiesāincluding lightweight nature and resistance to corrosionāare pivotal in its selection for various applications. From the automotive industry to aerospace, the benefits of aluminium injection extend to cost efficiency, speed, and adaptability in design, serving as a catalyst for innovation. Moreover, the diverse techniques in aluminium injection such as die casting and low-pressure die casting showcase the process's flexibility, allowing manufacturers to select the best method for their specific needs.
"Understanding these properties and processes today is crucial for optimizing practices in the rapidly evolving manufacturing landscape."
Implications for the Industry
The implications for the industry are particularly significant as we consider the future demands for lighter, stronger, and more sustainable materials. As environmental concerns escalate, the aluminium injection process adapts by embracing innovative technologies that prioritize energy efficiency and recycling. Manufacturers would do well to re-evaluate their approaches to meet market demands, staying ahead of competitors who harness the full potential of aluminium injection. Ultimately, a firm grasp of these insights not only informs current practices but also fosters innovation, ensuring relevance in an increasingly competitive arena.
Engaging with the prompt further expands the understanding of how crucial aluminium injection is as a cornerstone in contemporary manufacturing. The continuous evolution of this process must remain at the forefront of discussions and research, helping stakeholders navigate the changing landscapes of technology and sustainability.