Ductility of Steel: Insights and Applications
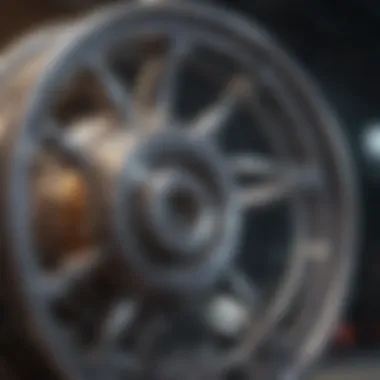
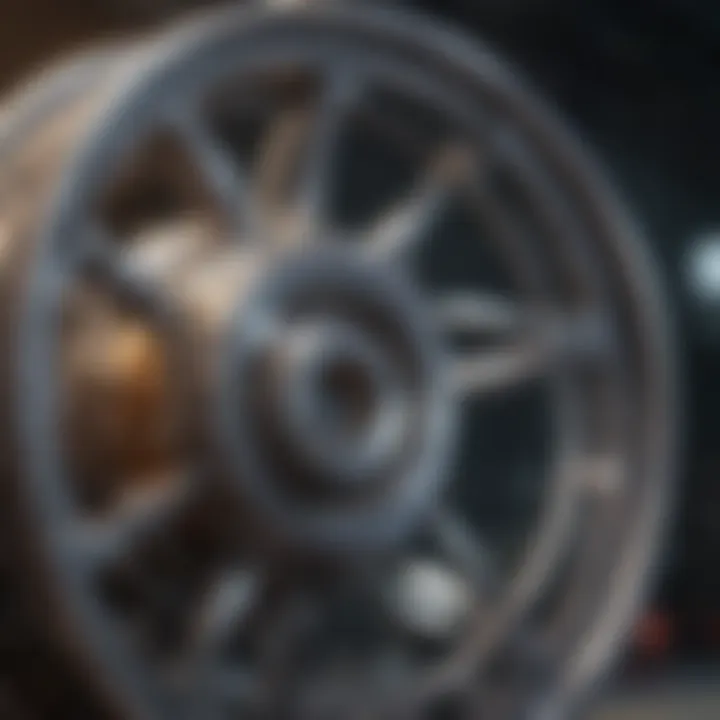
Research Overview
Ductility in steel is more than just a buzzword tossed around by materials scientists; it's a pivotal characteristic that determines how steel will perform under stress. Understanding ductility is akin to acquiring the keys to the castle of structural integrity. This section delves into the crucial aspects of ductility, shedding light on its benefits, challenges, and relevance in contemporary engineering.
Summary of Key Findings
The exploration of ductility reveals several key insights about this versatile material. For instance:
- Ductility is proportional to temperature: Steel generally becomes more ductile when heated, a factor often leveraged in forging and welding processes.
- Material composition plays a vital role: The inclusion of elements like carbon influences ductility. Higher carbon content tends to make steels more brittle while lower amounts promote ductility.
- Microstructure is significant: Variations in the microstructure of steel, such as the presence of martensite or pearlite, can affect ductility, illustrating the nuanced relationship between chemical makeup and mechanical properties.
- Temperature and strain rate: The temperature at which steel is used along with the rate of deformation affects how ductile the steel will be at a given moment.
These findings point to the multifaceted nature of ductility, cementing its role in engineering applications.
Relevance to Current Scientific Discussions
In an era where material reformulation and innovation are at the forefront, understanding ductility has become increasingly vital. The implications of ductility are profound, reaching into many areas:
- Safety regulations: As structures become more complex and are subjected to unprecedented forces from natural disasters or human activity, the understanding of ductility ensures safer infrastructures.
- Sustainable Development: With the push towards sustainable materials, ductility becomes a discussion point in creating steel that not only holds up under pressure but also promotes an environmentally friendly footprint.
This knowledge forms the backbone of current research, where engineers and scientists strive to push the boundaries of what steel can achieve without compromising safety or functionality. In the same breath, the historical context of steel usage reflects an ongoing evolution toward making it more adaptable and reliable.
"A deep understanding of ductility isn't just academic; it shapes real-world applications bridging the gap between theory and practice."
In the next section, we will discuss the methodologies employed to study ductility in steel, which will further illuminate its vital role in engineering.
Understanding Ductility
Ductility is a key property of materials, particularly steels, that allows them to undergo significant plastic deformation before rupture. It plays a vital role in various applications, ensuring integrity and safety in structural engineering and manufacturing. Understanding ductility means appreciating how materials react under stress, which is paramount for engineers, designers, and materials scientists alike.
When a material has high ductility, it tends to absorb energy well, which can be crucial in scenarios like construction or automotive design. By incorporating ductile materials, structures can withstand unexpected loads, like those experienced during an earthquake, enhancing safety and longevity.
Moreover, recognizing the factors that affect ductility enables professionals to manipulate material properties through alloying, heat treatment, or structural changes to achieve desired performance. This comprehension is essential not just for producing quality products, but also for innovating in fields ranging from aerospace to everyday consumables.
Definition of Ductility
Ductility refers to the ability of a material to deform under tensile stress. In simpler terms, if you can stretch or shape a metal without it breaking, it’s considered ductile. A classic example is drawing copper wire—this process highlights how a ductile material can be elongated significantly without failure.
Ductility is quantitatively measured as the percentage of elongation or reduction in area after a tensile test.
"Ductility’s significance extends beyond mere flexibility; it embodies a material’s capacity to endure challenges without fracturing, ensuring performance in critical applications."
Many common metals, such as aluminum and gold, exhibit high ductility, while others, like cast iron, demonstrate brittleness. This difference largely arises from the atomic structure of materials and how they respond to stress.
Historical Perspective
The concept of ductility has been studied for centuries, dating back to ancient civilizations that utilized metals for tools and construction. The Greeks and Romans recognized the importance of using metals like bronze, which offered a combination of strength and ductility, for their architectural feats.
During the Industrial Revolution, engineers started to systematically explore material properties, including ductility, leading to significant advancements in steel production. Steel, primarily introduced in manufacturing, was recognized for its superior ductile properties compared to iron. This development revolutionized building structures like bridges and skyscrapers, making them safer and more efficient.
With the modern age, ductility became a focal point in materials science. Rigorous testing methods evolved, providing deeper insights into how different alloys react under load. This historical journey has paved the way for the contemporary understanding of ductility, allowing us to refine and innovate materials for a broad spectrum of applications.
Understanding the historical context not only enriches the knowledge of ductility but also facilitates innovations that push the bounds of engineering today.
The Science Behind Ductility
Ductility is not merely a property that makes steel useful; it is a fundamental aspect intricately linked to its internal structure and behavior under stress. Understanding the science behind ductility is essential for engineers and material scientists alike. It helps them predict how materials will behave when subjected to different forces, which in turn influences design and safety standards across various applications. Whether it is building skyscrapers or designing vehicle components, grasping the principles of ductility is crucial. It allows for innovation and adaptation of materials to meet precise performance criteria.
Crystal Structure and Ductility
At the core of ductility lies the atomic arrangement of steel. Most steel types crystallize in the face-centered cubic structure, also known as FCC. This unique arrangement permits atoms to slide past one another relatively easily, thus allowing for deformation without immediate fracture. When a sample of steel is pulled, the layers of atoms can shift, and this sliding contributes directly to the observed ductility.
- Grain Size: The size of these grains can also significantly impact ductility. Smaller grains typically lead to higher ductility due to increased boundaries that hinder dislocation motion.
- Phase Transformations: Moreover, phase transformations like those in martensitic steel can alter the ductility properties, as different phases have unique responses to stress.
In essence, if one wants to understand why a certain steel is ductile or brittle, one must look to its crystal structure. The interplay between grain boundaries, phase type, and external forces creates the conditions for ductility.
Dislocation Theory
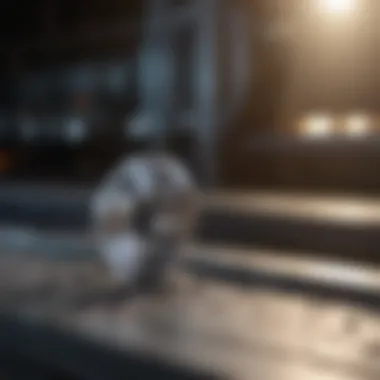
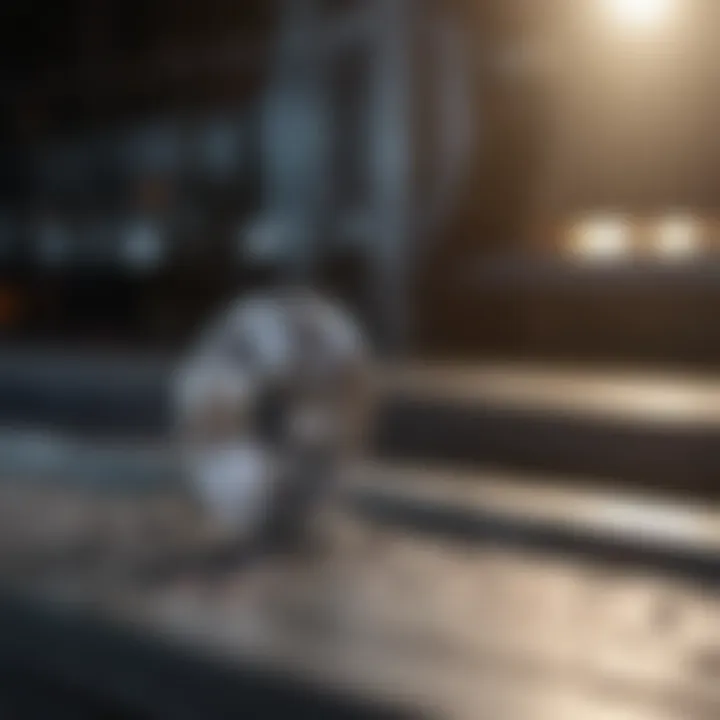
Dislocations are defects within the crystal structure. They play a pivotal role in ductility by enabling deformation to occur at lower stress levels than would otherwise be required. This concept is captured in the dislocation theory, which states:
- Movement of Dislocations: When stress is applied, dislocations move through the crystal lattice. This movement contributes to plastic deformation, allowing the material to change shape without breaking.
- Work Hardening: As dislocations multiply and interact, they create more obstacles, increasing the strength of the material but often at the expense of ductility. Thus, there’s a delicate balance between strength and ductility that must be managed in engineering applications.
Understanding these dislocation dynamics can provide insights into how to strengthen materials while maintaining their necessary ductility for specific applications, such as in seismic-resistant structures.
Role of Temperature
Temperature is a significant factor that affects ductility. Generally, as temperature increases, ductility improves. This phenomenon can be explained through a couple of mechanisms:
- Thermal Energy: With elevated temperatures, atoms vibrate more vigorously. This increased atomic movement helps dislocations to overcome barriers more easily, leading to enhanced plastic deformation.
- Diffusion Effects: High temperatures also promote diffusion, which can rearrange atomic structures to minimize stress concentrations, allowing for more ductile behavior.
On the flip side, at low temperatures, steel can become much more brittle. Engineers must take temperature into account, especially in environments subject to extreme conditions, ensuring that materials behave predictably under stress.
"Understanding the subtle interplay between crystal structures, dislocations, and temperature gives engineers the foresight to predict material behavior effectively."
Grasping the science behind ductility—its microstructural origins and cascading effects—is essential not just for innovating new materials but also for ensuring robust safety standards in engineering designs.
Factors Influencing Ductility
Understanding the factors influencing ductility is crucial for both researchers and practitioners in materials science and engineering. Ductility, the ability of a material to deform under tensile stress, plays an essential role in determining the suitability of various steel grades for specific applications. It influences not just the performance of the material but also the safety and reliability of structures made from it. Knowing the key elements that affect ductility can lead to enhanced material properties, optimizing performance in real-world conditions.
Chemical Composition
The chemical makeup of steel is a primary determinant of its ductility. Different elements can either enhance or reduce a material’s ability to stretch and deform. For example, the inclusion of carbon is a double-edged sword. While carbon is essential for the development of strength in steel, excessive amounts can contribute to brittleness, leading to catastrophic failure under stress. On the other hand, alloying elements such as manganese or nickel are well-known for improving ductility. Manganese works by refining microstructures and enhancing toughness, effectively allowing steel to withstand larger deformations.
Moreover, the proportions of elements like sulfur and phosphorus should be carefully controlled. High levels of sulfur can lead to microstructural flaws, diminishing ductility. Therefore, a balanced chemical composition tailored to specific applications is fundamental for achieving desired ductility levels.
Microstructural Characteristics
Microstructure refers to the arrangement and size of the crystals in a material. This characteristic significantly influences a steel's ductility. For instance, a finer grain structure usually enhances ductility. When the crystal grains are smaller, there are more boundaries available to absorb deformation, and thus the material can stretch more readily before experiencing failure. This phenomenon is a direct result of how dislocations move through the crystal lattice.
Heat treatment processes such as annealing can be employed to manipulate the microstructure of steel. Annealing promotes recovery and recrystallization, often leading to a more uniform and finer microstructure. While each treatment comes with its trade-offs in strength and toughness, understanding the balance through detailed analysis is essential for optimizing ductility in practical applications.
Strain Rate Effects
Strain rate, the speed at which a material is deformed, also holds significance in ductility discussions. At lower strain rates, materials tend to exhibit more ductile behavior as they can absorb more energy before failure occurs. In contrast, at high strain rates, such as those found in impact situations, steel might behave more brittlely. This behavior is influenced by several factors, including temperature and the material's microstructure.
For example, if steel is subjected to rapid deformation, it may not have significant time to rearrange its dislocations, which can lead to premature failure. On the flip side, ductility can improve under some controlled high-rate loading conditions, such as in certain automotive applications where high-energy absorption is beneficial.
"Understanding the influence of strain rate is pivotal for applications exposed to dynamic loads. Knowing how materials behave under varying conditions could make the difference between success and failure in engineering designs."
In closing, grasping the intricacies of chemical composition, microstructural characteristics, and strain rate effects provides insights into the ductility of steel. It enables engineers and researchers to design and select materials best suited for specific demands, enhancing safety and performance in their respective environments.
Testing Ductility
Ductility testing plays a pivotal role in understanding the mechanical properties of steel. This aspect is crucial not just for engineers but also for researchers and industry professionals looking to ensure safety and reliability in various applications. Knowing how ductile a steel is can influence design choices, affect pricing, and impact performance in real-world scenarios.
When we talk about ductility, we don’t mean just bending and twisting the material at random. It's a precise measurement that helps predict how steel behaves under stress and strain. How steel reacts when led to its limits can tell an engineer if it's fit for projects like bridges, buildings, or even the frame of a new car.
Standard Testing Methods
To evaluate the ductility of steel accurately, several standardized tests are often employed. Among the most commonly used are the tensile tests and bend tests. These methods offer a systematic approach to measuring how a sample performs under tension.
- Tensile Test: In this test, a steel sample is pulled until it either deforms or breaks. The key parameters measured are:
- Bend Test: As straightforward as the name suggests, a sample is bent until it reaches its yield point. This method helps in determining if the material will crack or maintain integrity under bending stress.
- Elongation: This indicates how much a material can stretch. It’s expressed as a percentage of the original length.
- Reduction of Area: This measures the decrease in cross-sectional area of the sample after fracture, offering insight into how the steel will perform when subjected to loads.
These testing methods are crucial, as they provide quantitative data on ductility, allowing for comparisons across different steel grades and formulations.
Evaluating Tensile Properties
When evaluating tensile properties, it's important to consider not only the outcome of the tests but also how these results correlate to real-world application. For instance, the yield strength and ultimate tensile strength are critical metrics derived from the tensile test. These values help in determining the maximum load the steel can sustain before it yields or undergoes plastic deformation.
Factors such as the following can significantly impact tensile properties:
- Grain Structure: The arrangement of atoms in steel can alter its ductility. A finer grain structure generally contributes to better ductility.
- Temperature: Testing at varying temperatures can uncover how steel responds under different environmental conditions; lower temperatures might make steel more brittle, while higher temps can enhance ductility.
- Strain Rate: The speed at which force is applied can also modify the properties of the material. A slower application rate often results in a more ductile behavior.
"Understanding tensile properties provides insights that extend beyond the lab, helping to predict material performance in the field.”
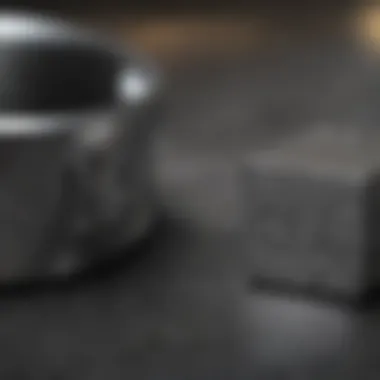
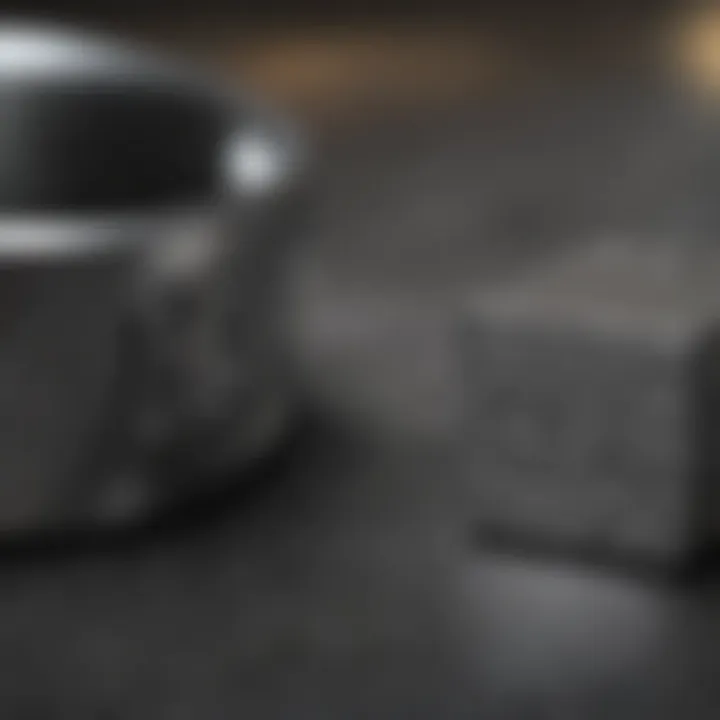
Impact Testing Procedures
Impact testing further complements the assessment of ductility by measuring resistance to sudden forces. This is particularly vital in applications where steel might experience dynamic loads, such as in earthquake-prone areas or in automotive collisions.
Common impact testing methods include the Charpy and Izod tests:
- Charpy Test: In this method, a notched sample is struck by a swinging hammer, and the energy absorbed during the fracture gives an indication of toughness—a property closely related to ductility. The resulting data helps engineers make decisions about materials used in structural applications.
- Izod Test: Similarly to the Charpy, it also measures the impact resistance but involves a different sample setup. It provides information on how materials can handle shock loads, a critical aspect when assessing their ductility.
By employing these testing procedures effectively, one can obtain a comprehensive understanding of ductility in steel, ensuring that material choices are both safe and efficient for their intended applications.
Ductility in Different Steel Grades
Ductility plays a pivotal role in the performance of various steel grades, influencing their applications across multiple industries. Understanding how ductility varies among different types of steel is crucial for engineers and designers because it directly affects structural integrity, material selection, and safety considerations. Ultimately, assessing a steel's ductility characteristics informs decisions that can prevent failure in engineering structures while optimizing performance under stress.
Mild Steel
Mild steel, known for its relatively low carbon content, exhibits commendable ductility. This property is primarily attributed to its ferritic structure, which promotes dislocation movement during deformation. This characteristic allows mild steel to undergo considerable elongation before fracture, making it incredibly useful in construction applications.
One of its notable benefits is the ease of fabrication. Mild steel can be rolled, drawn, or forged into a variety of shapes without losing its structural integrity. Such flexibility makes it a preferred choice for beams, columns, and other structural elements in buildings. Yet, while mild steel has excellent ductility, its lower strength means that it may not be suitable for applications requiring higher load-bearing capabilities without reinforcement.
High-Strength Low-Alloy Steel
High-strength low-alloy (HSLA) steels combine enhanced strength with ductility, making them attractive in situations where weight reduction is essential, such as in the automotive and aerospace industries. These steels typically possess lower alloying elements compared to conventional high-strength steels, which helps retain ductility while improving tensile strength.
A key consideration when using HSLA steels is the balance they provide. They maintain sufficient ductility to allow for energy absorption during impact, which is critical in crash-resistant vehicle designs. The challenge, however, is to avoid too much alloying, which may lead to lower ductility if the composition is not managed appropriately.
Stainless Steel
Stainless steel is often associated with corrosion resistance, but its ductility is a substantial part of its overall performance. The presence of austenitic structures in many stainless steel grades contributes significantly to their ductility. These structures can absorb significant strain without cracking, allowing stainless steel to be formed into intricate shapes.
This property is particularly beneficial in architectural applications, where aesthetic considerations are accompanied by performance. Despite its favorable ductility, designers need to remain mindful of work-hardening effects that can occur during fabrication, increasing the risk of brittleness if not properly managed.
Tool Steel and Its Ductility Challenges
Tool steel, while recognized for its hardness and wear resistance, faces challenges in terms of ductility. Depending on the specific type, tool steels can range from low to high ductility. For instance, high-speed steels (HSS) are designed to retain hardness at elevated temperatures but can sacrifice ductility in the process.
When applied in tools that require both hardness and ductility, a careful balance is necessary. Understanding the heat treatment processes and the resulting microstructural changes is critical. If improperly treated, the ductility may suffer, leading to early tool failure during operations.
"A balance of properties is vital in tool steels; understanding the limits of ductility can prevent costly operational mishaps."
Considering the nuances of ductility in different steel grades provides invaluable insights for professionals in materials science and engineering. Not only does it encourage informed choices in material selection, it also enhances safety and performance in practical applications.
Applications Relating to Ductility
Ductility plays a crucial role in determining how steel performs under stress and strain. Various industries leverage this property to enhance performance, safety, and longevity in their products. From construction to automotive engineering, the ability of steel to deform without breaking offers multiple advantages, making it essential in applications where resilience is key.
Construction and Structural Engineering
In the realm of construction, ductility is often regarded as a non-negotiable trait in structural materials. When buildings or bridges experience heavy loads or seismic activities, materials that can absorb energy and undergo deformation without failing are vital. Steel, particularly that designed with high ductility, can accommodate these demands.
- Impact Resistance: Structures must withstand extreme weather, earthquakes, or accidental impacts. Ductile steel bends rather than fractures, which can be a lifesaver in quake-prone areas.
- Load Bearing: A ductile material ensures that loads are distributed evenly, preventing localized failures that could lead to catastrophic results.
- Construction Techniques: Modern practices often employ pre-tensioned or post-tensioned steel, where the ductility enhances the effectiveness of these methods, ensuring structures remain sound over time.
The flexibility offered by ductility allows engineers to design safer buildings, creating end-products that can stand the test of time and elements.
Automotive Industry Considerations
When it comes to vehicles, ductility isn't just about strength; it's about forming and shaping. In the automotive sector, steel parts undergo numerous processes, from stamping to welding, and must maintain integrity through various stresses during operation. This is where ductility shines, offering several benefits:
- Crash Safety: In the event of a collision, ductile steel can absorb impact energy, providing crumple zones that protect passengers.
- Manufacturing Versatility: Components such as car frames and body panels can be molded to desired shapes without compromising their strength, making designs more aesthetically appealing and aerodynamic.
- Durability and Maintenance: Over time, vehicles wear from use. The ductility of steel allows for some degree of deformation under stress without leading to immediate failure, extending the lifespan of automotive components.
As these structures must endure rigorous conditions, ductility ensures that vehicles not only perform well but also prioritize safety.
Marine Applications
The marine industry, which faces unique environmental challenges, also benefits significantly from the ductility of steel. Ships and offshore structures need to withstand dynamic forces occurring from waves and weather conditions.
- Corrosion Resistance: With additional treatments, ductile steel can tolerate harsh sea conditions better, maintaining structural integrity over time.
- Flexibility Under Stress: Vessels encounter bending moments that might lead to cracks in less ductile materials. Ductile steel can flex, absorbing shock and preventing significant damage.
- Structural Innovation: Incorporating ductile steel into ship designs allows for innovative forms that can improve buoyancy and reduce drag, enhancing overall performance.
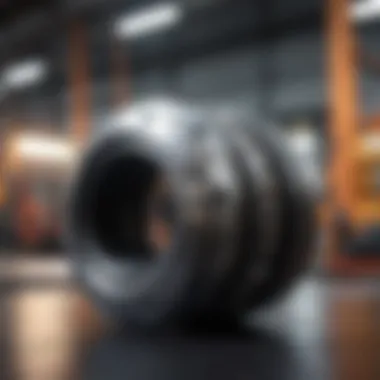
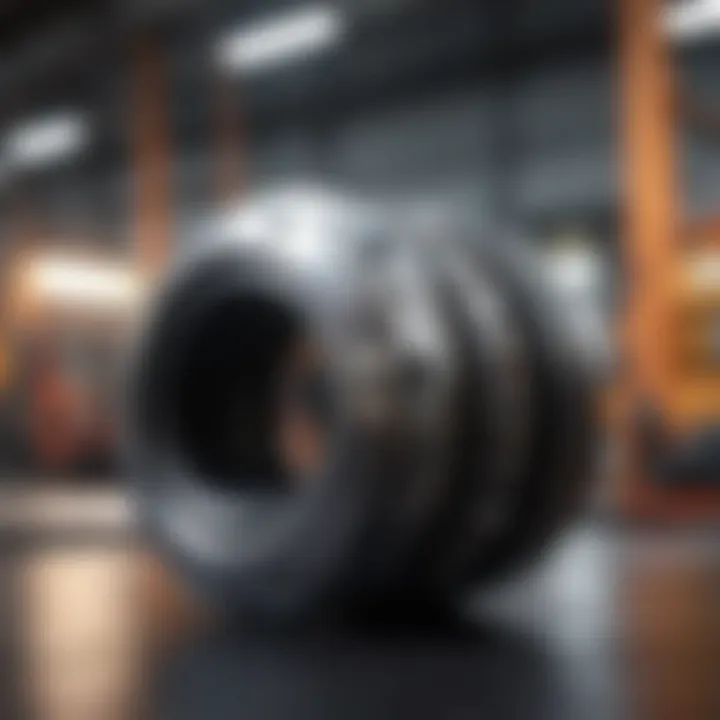
In challenging conditions like the open sea, the ductility of steel is a critical factor that enables the construction of navigable vessels and infrastructure.
In summary, the applications of ductility across various industries underline its significance, illustrating that beyond mere strength, the ability to adapt and absorb stress is fundamental in offering safety, performance, and longevity.
Ductility and Structural Integrity
Ductility plays a pivotal role in maintaining the structural integrity of materials, particularly in steel used for construction and engineering applications. Understanding this relationship is vital for professionals engaged in material science, civil engineering, and architecture. When evaluating materials for construction, it’s not merely about strength; ductility becomes a crucial factor in ensuring that structures can withstand various stresses without failing catastrophically.
Ductile materials can endure significant deformation before fracturing. This capacity for yielding instead of snapping makes steel exceptionally reliable. Several key elements highlight its significance in structural integrity:
- Energy Absorption: In dynamic loads, such as those experienced during earthquakes or impacts, ductile steel can absorb energy through deformation. This characteristic mitigates the force transferred to the structure, reducing the likelihood of failure
- Predictable Failure Mechanism: A ductile material exhibits plastic deformation, offering visible warnings of stress before total collapse occurs. Structural engineers appreciate this trait, as it allows for timely maintenance or reinforcement rather than unexpected disasters.
- Design Flexibility: The ductility of steel provides architects and engineers with the freedom to design innovative structures that can bend without breaking, promoting creativity without compromising safety.
The consideration of ductility becomes multifaceted when designing for seismic events. Buildings erected in earthquake-prone areas must not only be strong but also ductile to absorb shocks.
"Material ductility is not just a technical term; it's a bridge between safety and creativity in architectural design."
\
Failure Mechanisms in Ductile Materials
Understanding how ductile materials fail is equally important. Unlike brittle materials that may shatter unexpectedly, ductile materials like steel exhibit a gradual failure mode. This failure is usually preceded by deformation, allowing for warning signs such as cracking or excessive bending.
Key failure mechanisms in ductile materials include:
- Necking: This occurs when a localized reduction in cross-section takes place after reaching the yield point. It can signal that the material is nearing its ultimate tensile strength.
- Creep: Over time and with continuous stress, ductile materials can slowly deform under high temperatures and loads. This phenomenon can lead to structural failures, especially in long-term applications.
- Fatigue: Repeated loading and unloading can induce microstructural changes over time, leading to eventual cracks and failure even under stress levels below the material’s yield strength.
Engineers must consider these failure mechanisms to enhance safety protocols and maintenance schedules in design work.
Importance of Ductility in Earthquake-Resistant Design
In seismic design, the need for ductility cannot be overstated. The dynamic forces at play during an earthquake require materials that can not only support loads but also adapt to sudden changes without failing. In particular, the design must integrate ductility to ensure:
- Energy Dissipation: Ductility allows structures to absorb and dissipate seismic energy, reducing the forces that would otherwise damage or destroy the building.
- System Redundancy: Structures designed with ductility in mind often incorporate redundancy. This means even if one path of load transfer fails, the remaining connections can take over, preventing a total collapse.
- Serviceability and Safety: Ductile designs consider the serviceability of buildings after an earthquake. While some damage is acceptable, the structure must remain safe for occupants, enabling quick evacuation if necessary.
Incorporating ductility in structures not only safeguards lives but also preserves the integrity of facilities and infrastructure, building community resilience against natural disasters.
Advancements in Ductility Enhancements
The continual evolution in steel technology has spotlighted advancements in ductility enhancements as a cructial component in the field of materials science. Enhancing the ductility of steel not only contributes to its usability in various industrial applications but also ensures higher safety standards in structural integrity. As societal demands grow, understanding innovative methods to bolster ductility has become an increasingly important area of research.
Recent Research Developments
Recent studies in the realm of ductility enhancements have revealed numerous pathways to improve steel's mechanical properties. Research institutions and universities have been working overtime to develop methods that not only increase yield strength but also enhance ductility. One such study published in a materials science journal highlighted the role of microalloying. By deliberately adding trace elements to steel, researchers found that they could significantly alter the microstructure, resulting in improved ductile behavior under stress.
Moreover, collaborative projects between academia and industry have emphasized the practical implications of these findings. These partnerships aim to deliver new grades of steel with tailored properties that meet specific engineering requirements. Notably, artificial intelligence is finding its place in this field, assisting researchers in discovering new alloy combinations and predicting their performance under different conditions.
"The unique composition of steel can define its ductility; it's all about getting that right mix."
Innovative Alloying Techniques
Alloying is a key strategy in the production of ductile steel. Innovative techniques are transforming traditional methods. For instance, employing a combination of chromium, nickel, and manganese enhances the toughness of steel, presenting a case of effective tweaking of the alloying elements. A focus on low carbon, high manganese steel has also emerged. This approach showcases how manipulating conventional alloy formulas can produce steel with remarkable ductility and an impressive hardening capacity.
Additionally, researchers have trialed advanced welding methods, such as friction stir welding, alongside these innovative alloys. The incorporation of such techniques has the potential to enhance the structural integrity of joints in steel, providing further reliability without compromising ductility.
Nanotechnology Applications
Nanotechnology is revolutionizing ductility enhancements. At the nanoscale, materials exhibit unique properties that differ significantly from their bulk counterparts. Researchers have begun experimenting with nano-sized particles added to molten steel to promote better grain refinement. This leads to a finer microstructure, which is well-known to enhance ductility. A current trend is to use nanoparticles made of titanium and carbides to not only strengthen the steel but also significantly improve its ductibility.
Furthermore, coatings that utilize nanotechnology offer another layer of protection, minimizing wear and enhancing performance over time. With ongoing research into integrating nano-coatings that refine the steel's behavior, the future of ductility enhancement looks promising.
In summary, understanding and implementing advancements in ductility enhancements is key to unlocking the full potential of steel in modern engineering applications. Each approach, from innovative alloying to the applications of nanotechnology, carries implications that extend to diverse sectors from construction to automotive manufacturing, highlighting the critical nature of ongoing research in this field.
Culmination
In wrapping up our exploration of ductility in steel, it's essential to highlight the numerous facets we've traversed. Ductility isn't just a fanciful term tossed around in metalworking discussions; it represents a critical property influencing both the longevity and safety of structures we interact with daily. From the foundational scientific principles, such as atomic behavior and temperature effects, to the practical applications seen in fields ranging from construction to automotive engineering, every aspect underscores ductility's significance.
Summary of Key Points
- Ductility Defined: We’ve established that ductility refers to the ability of steel to deform under tensile stress without fracturing. It allows structures to absorb energy, aiding in damage prevention during extreme conditions.
- The Role of Ductility in Safety: A ductile material can provide visual warning signs before failure. This characteristic is paramount in earthquake-resistant designs, where it can mean the difference between life and death during seismic events.
- Steel Grades and Their Ductility: Different grades of steel exhibit varying ductility levels. While mild steel shows great ductility, other high-strength variants like tool steel can present challenges, demonstrating that not all steels are equal in their ductile properties.
Future Directions in Ductility Research
As we look forward, the future of ductility research appears promising, with several avenues worth exploration.
- Advanced Alloying Techniques: Research into new alloy compositions may yield steels that offer enhanced ductility while maintaining strength. Using elements like niobium and vanadium is currently garnering interest.
- Nanotechnology: Delving into the nanoscale structure of materials can reveal insights on enhancing ductility. It’s an exciting frontier that may change how we think about material science altogether.
- Real-time Monitoring: The integration of sensors in steel structures for real-time assessment of ductility properties could revolutionize safety measures. This technology could allow for scaffolding, bridges, and other structures to alert us to changes in their integrity, giving us crucial time to act.