Exploring the Advancements in Composite Matrix Composites
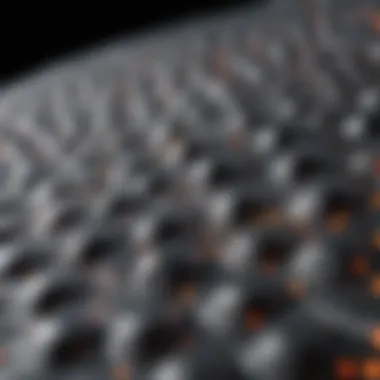
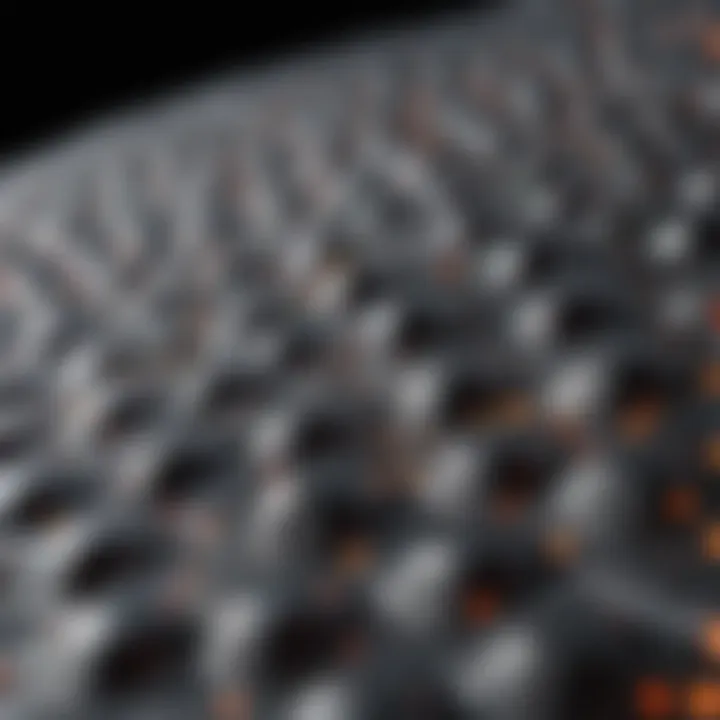
Intro
Composite matrix composites (CMC) represent a significant advancement in material science, offering a unique combination of properties that make them ideal for various applications across different industries. This article aims to provide a thorough examination of CMC materials, focusing on their composition, properties, applications, and the latest developments in the field.
This exploration will also delve into the manufacturing processes that underpin these materials, emphasizing their performance metrics and environmental impacts. Lastly, we will discuss the future prospects of CMC materials, uncovering their potential to shape contemporary and emerging technological landscapes.
Research Overview
Summary of Key Findings
Composite matrix composites are generally made from a matrix of ceramic material reinforced with fibers, typically carbon or ceramic. This structure offers several advantages, such as:
- High strength-to-weight ratio: CMCs maintain structural integrity while being lightweight.
- Thermal resistance: They withstand high temperatures, making them suitable for aerospace and automotive applications.
- Chemical stability: Their resistance to harsh environments prolongs their lifespan in demanding conditions.
The analysis of recent advancements indicates that:
- New manufacturing techniques, such as additive manufacturing, are increasing design flexibility and performance.
- The increase in CMC application in renewable energy sectors, specifically in wind turbine blades and thermal barriers, shows promising trends.
Relevance to Current Scientific Discussions
In recent years, CMC materials have gained attention in scientific discourses due to their contributions to sustainable technology. Their application reduces the need for heavier materials, which in turn enhances fuel efficiency in transportation sectors. Furthermore, ongoing research continues to focus on optimizing CMC properties for even wider application.
Methodology
Research Design and Approach
The study of composite matrix composites utilizes a multi-faceted research design. This includes:
- Case studies on the implementation of CMCs in industries such as aerospace and automotive.
- Analytical reviews of existing literature that covers various CMC compositions and their performance metrics.
Data Collection and Analysis Techniques
Data were collected from peer-reviewed journals, industry reports, and expert interviews. Advanced analysis techniques such as comparative material performance tests and lifecycle assessments were employed to evaluate the effectiveness and sustainability of CMCs.
"Composite matrix composites represent a pivotal technology in the advancement of materials, reflecting ongoing innovations that align with environmental sustainability."
Prolusion to Composite Matrix Composites
Composite matrix composites (CMC) represent a significant advancement in material science. They combine the characteristics of various materials to optimize performance across a range of applications. The appeal of CMCs lies in their ability to provide enhanced mechanical and thermal properties, which are essential in specific sectors like aerospace, automotive, and energy. Understanding CMC materials is crucial for students, researchers, and professionals looking to innovate within these fields.
Definition of Materials
Composite matrix composites are innovative materials that consist of a matrix and reinforcement. The matrix typically is ceramic or metallic, while the reinforcement is often made from fibers or particles. This combination results in materials that maintain high strength and lightweight properties. CMCs have gained attention due to their unique ability to withstand extreme temperatures and resist environmental damage, making them suitable for various applications where traditional materials may fail.
Historical Background and Development
The evolution of composite matrix composites dates back several decades. Initially, researchers focused on traditional materials, but their limitations led to the exploration of composites. In the late 20th century, advancements in materials science enabled the development of CMCs, specifically designed for high-stress environments like turbine engines. Over time, different types of CMCs have been formulated, improving processing techniques and expanding their use in diverse industries. The historical context is essential for appreciating the current innovations and future potential in the field of CMCs.
Composition and Structure of Materials
The composition and structure of composite matrix composites (CMCs) are central to their performance and applicability in various industries. Understanding the key elements that make up CMC materials allows researchers and professionals to better appreciate their advantages and challenges. This segment delves into the materials used in CMCs and their microstructural characteristics, offering insights that underscore their significance in modern technology and engineering.
Types of Materials Used
CMC materials typically consist of a matrix and reinforcement components. The matrix is often ceramic, which provides high-temperature resistance, while the reinforcements can be fibers or particles that enhance mechanical integrity. Common materials include:
- Silicon Carbide (SiC): Known for its high-temperature stability and strength, SiC is widely used in aerospace applications.
- Alumina (Al2O3): This ceramic material offers excellent wear resistance but has lower toughness compared to other materials.
- Carbon Fibers: They offer great strength-to-weight ratios and are often applied as reinforcements in the ceramic matrix.
- Boron Nitride: This material contributes to thermal conductivity, making it useful for high-performance applications.
The selection of these materials impacts the overall performance of CMCs, influencing properties like durability, temperature resistance, and weight.
Microstructure of Composites
The microstructure of CMCs plays a crucial role in determining their mechanical and thermal properties. The arrangement and interaction of the matrix and reinforcement materials create a unique structure that enhances performance. Key aspects include:

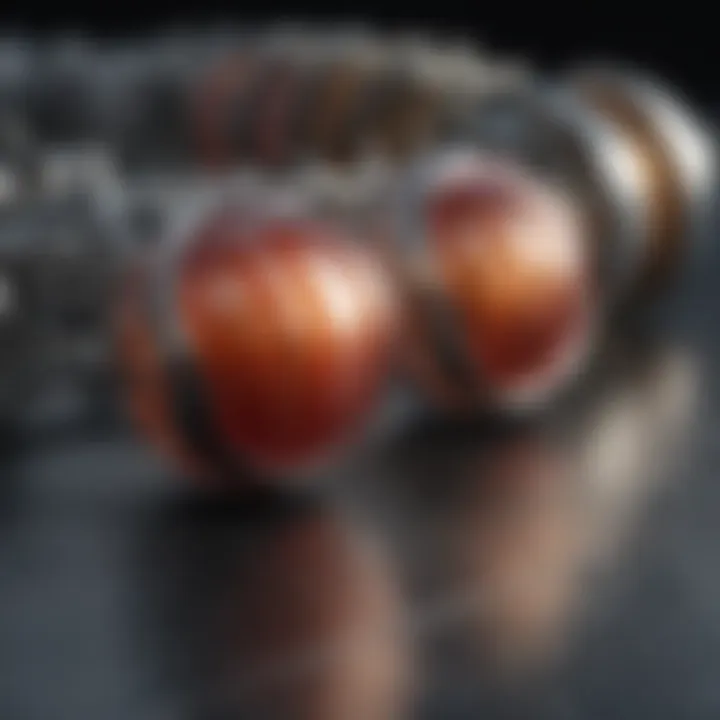
- Interface Quality: The bond quality between the matrix and the reinforcement is vital. A strong interface allows for effective load transfer, improving mechanical properties.
- Distribution of Reinforcements: Uniform distribution of reinforcement materials within the matrix results in consistent strength and reduces weaknesses in specific areas.
- Porosity Levels: The amount of porosity can affect thermal and mechanical behaviors. Lower porosity typically leads to higher strength, but achieving this balance is a complex challenge.
Understanding the microstructure helps in optimizing the performance parameters of CMCs and tailoring them for specific applications.
"The synergy between matrix and reinforcement materials in CMCs is what elevates their performance beyond traditional materials."
In summary, the composition and structure of CMC materials are critical for their use in various high-performance applications. By selectively choosing materials and controlling the microstructure, engineers can develop composites that meet stringent industry requirements.
Manufacturing Processes for CMCs
The manufacturing processes for composite matrix composites (CMCs) are integral to their performance, quality, and overall applicability. Understanding these processes is essential for anyone involved in engineering or materials science. The methods of producing CMCs directly influence their mechanical, thermal, and electrical properties. From cost-effectiveness to dimensional accuracy, various manufacturing techniques impact the final material attributes and application viability.
Traditional Fabrication Techniques
Traditional fabrication techniques play a significant role in the production of CMCs. These methods, though often more labor-intensive, offer established approaches for creating composite materials. Common techniques include:
- Hand Lay-Up: This method involves manually layering the reinforcement materials and resin, allowing for specific customization. It is suitable for creating complex shapes but can be laborious and time-consuming.
- Filament Winding: Here, continuous fibers are wound around a mandrel, allowing for high-strength parts. This technique is often used in aerospace applications where durability is crucial.
- Pultrusion: In this process, composite materials are pulled through a heated die, creating a continuous length of reinforced shape. This method yields consistent cross-sections and is effective for linear applications.
Despite its advantages, traditional methods can have limitations, such as lower production rates and potential inconsistencies in material properties. However, they remain vital due to their simplicity and reliability.
Advanced Manufacturing Methods
The evolution of technology has given rise to advanced manufacturing methods for CMCs, enhancing production capabilities and material performance. Techniques such as:
- Additive Manufacturing (3D Printing): This innovative approach allows for complex geometries and rapid prototyping. CMCs can be printed layer by layer, permitting high customization and potentially reducing material waste.
- Resin Transfer Molding (RTM): RTM involves injecting resin into a closed mold containing dry fibers. This method enables precise control over the fiber-to-resin ratio, resulting in high-quality composites with better mechanical performance.
- Autoclave Processing: This technique uses high-temperature and high-pressure environments to cure composite materials effectively. Autoclaves ensure uniform temperature distribution, enhancing material integrity and reducing voids.
Many of these methods focus on improving efficiency and performance. They enable the production of parts with superior properties, making CMCs more applicable across various industries. Additionally, these advanced methods can often reduce human error, leading to better consistency and overall quality.
"The choice of manufacturing process is crucial; it determines the mechanical performance and longevity of composite matrix composites."
Performance Characteristics of Materials
The performance characteristics of Composite Matrix Composites (CMCs) are indispensable for understanding their application across various industries. This section delves into the specific elements of mechanical, thermal, and electrical properties that define CMC materials. Each characteristic plays a crucial role in determining the usability and efficiency of CMCs, allowing industries to leverage these materials in innovative and effective ways.
Mechanical Properties
Mechanical properties are one of the most critical aspects of CMC materials. These properties include strength, stiffness, and toughness, which dictate how well these materials can withstand various loads or stresses.
- Flexural Strength: CMCs exhibit impressive flexural strength. This means they can endure bending forces without deforming. This is particularly beneficial in applications where structural integrity under stress is essential.
- Hardness: The hardness of CMCs determines their resistance to denting and abrasion. This characteristic is vital in sectors like aerospace and automotive where durability against wear and tear is paramount.
- Impact Resistance: Although CMCs are generally stiff, they also exhibit commendable impact resistance, which is important for applications that may experience sudden forces or shocks.
These mechanical properties ensure that CMCs can be used in high-stakes environments without compromising performance. The superior strength-to-weight ratio of CMCs often outshines traditional materials, promoting efficiency across engineering applications.
Thermal Properties
Another significant characteristic of CMC materials is their thermal properties. These properties include thermal conductivity, heat resistance, and thermal expansion, all of which influence how CMCs behave at various temperatures.
- Heat Resistance: CMCs can withstand extreme temperatures, making them suitable for environments like jet engines where high heat is a constant.
- Thermal Conductivity: This property varies among different CMC compositions. For instance, certain CMCs can conduct heat away from sensitive components rapidly, enhancing performance and safety.
- Low Thermal Expansion: Some CMCs possess low thermal expansion, ensuring that they maintain structural integrity and dimensional stability even when subjected to wide temperature fluctuations.
The unique thermal properties of CMCs not only expand their utility in industries reliant on high thermal performance but also improve efficiency in energy management applications.
Electrical Conductivity
While not all CMCs are designed for electrical applications, understanding their electrical conductivity is vital for specific uses. CMC materials can either be insulative or conductive, depending on their formulation.
- Conductive CMCs: Some composites incorporate conductive fillers. These materials can be utilized in applications where electrical conductivity is necessary, such as in certain aerospace components or sensors.
- Insulative CMCs: In contrast, insulative CMCs are essential in applications needing high dielectric strength. Such properties prevent electrical current from passing through, protecting sensitive electronics.
- Applications: The dual capability of CMCs to either conduct electricity or serve as insulators opens pathways for innovative designs in electronics and robotics, where managing heat and electricity is crucial.
In summary, the performance characteristics of CMC materials—mechanical, thermal, and electrical—are fundamental elements that determine their application breadth. Manufacturers and designers can harness these properties for better outcomes in various fields, ultimately leading to advancements in technology and materials science.
"The ability of CMCs to perform under extreme conditions is what makes them a pivotal choice for industries aiming for high reliability and efficiency."
Understanding these characteristics provides insights into the practical benefits and considerations when selecting CMC materials for specific applications.
Applications of Materials
Composite matrix composites (CMC) materials serve essential roles across various industries, driven by their unique properties. Their lightweight yet strong composition offers remarkable benefits, particularly in applications demanding durability and thermal stability. This section explores CMC usage in several critical sectors, demonstrating how these materials contribute to innovation and efficiency.
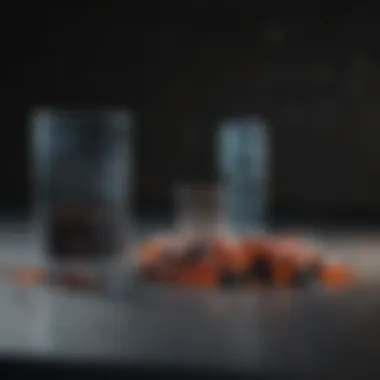
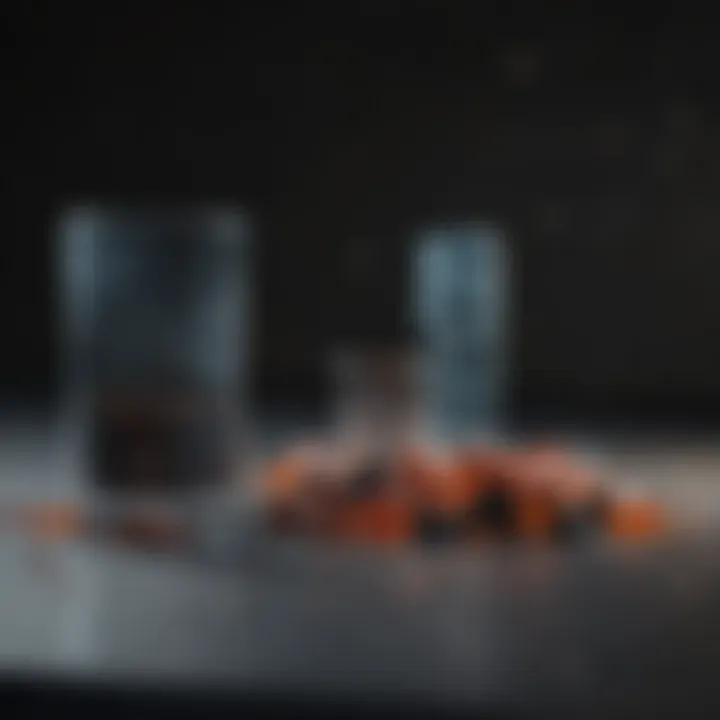
Aerospace Industry Innovations
In the aerospace field, CMC materials are game-changers. They are extensively used in components like turbine blades, combustion chambers, and thermal protection systems. The aerospace industry's focus on weight-saving strategies is crucial, as reducing mass leads to enhanced fuel efficiency. Thus, CMCs provide exceptional strength-to-weight ratios, which optimize performance.
Additionally, thermal resistance of CMCs allows aerospace components to endure extreme temperatures without significant deformation. Their use minimizes maintenance costs and enhances safety, leading to more reliable aircraft. Innovations in this sector are ongoing, with research focusing on improving the performance and manufacturability of CMC components.
Automotive Enhancements
The automotive industry also benefits from the application of CMC materials. Engineers incorporate CMCs into components such as brakes, engine parts, and structural elements. The high strength of CMCs enables lighter vehicles, improving fuel economy and reducing emissions. Notably, companies are integrating CMCs in electric vehicle (EV) applications, where thermal management is vital for battery efficiency and safety.
Moreover, CMCs provide advantages in durability, resisting wear and corrosion over time. The extended lifespan of components translates into long-term cost savings for manufacturers and consumers alike. These factors reinforce CMCs as preferred choices for modern automotive design strategies.
Medical and Biocompatibility
In the medical field, CMC materials are increasingly utilized due to their biocompatibility. They are prominent in the development of implants and prosthetics, where material compatibility with human tissue is critical. Each application must undergo rigorous testing to ensure it meets health and safety standards, making CMCs attractive for their potential success in these applications.
Additionally, the customization of CMCs allows for tailored mechanical properties suitable for various medical needs. Their lightweight nature promotes patient comfort, a significant concern with medical devices. This capability positions CMCs as promising materials in future medical innovations.
Energy Sector Applications
The energy sector requires robust materials for numerous applications, and CMCs fit the bill. Their excellent thermal properties make them ideal for use in power generation, particularly in turbines and furnace construction. As energy demands evolve, CMCs support the transition to greener technologies by enhancing efficiency and reducing material-related issues in energy generation.
Furthermore, CMCs are being studied for use in sustainable energy sources, such as solar and wind. In these areas, their durability and resistance to environmental stressors are advantageous. Given the rapid growth of renewable energy technologies, CMCs play a significant role in shaping future developments.
Environmental and Economic Considerations
Composite matrix composites (CMCs) represent a significant resource in modern materials science. Their impact stretches into environmental and economic realms. It is essential to analyze the environmental implications of CMC manufacturing and usage. Additionally, understanding how these materials fit within economic frameworks can inform their broader adoption.
Lifecycle Assessment of CMCs
Lifecycle assessment (LCA) is vital for evaluating CMCs. This process assesses the environmental effects of materials from their raw extraction to disposal. When applied to CMCs, LCA examines several stages:
- Raw Material Acquisition: Mining and processing can have substantial environmental effects. CMCs are often made from constituents like silicon carbide or carbon fibers. The extraction of these materials can be intensive regarding energy and land use.
- Manufacturing: The production of CMCs is energy-intensive. This stage involves multiple processing steps, including curing and reinforcement. Evaluating energy consumption and waste generated can guide sustainability efforts.
- Use Phase: CMCs typically have a long service life. Their high strength and resistance to heat mean less frequent replacement. This advantage helps to mitigate overall lifecycle emissions.
- End-of-Life Management: Disposing of CMCs raises challenges. Recycling options are limited. Many CMCs end up in landfills. Innovative recycling technologies can address this issue over time.
Through diligent LCA, stakeholders can identify opportunities for improvement. Companies can reduce environmental impacts by focusing on efficient sourcing and manufacturing practices.
Sustainability Challenges and Solutions
Despite their advantages, CMCs face several sustainability challenges. Addressing these obstacles is crucial for maximizing their potential in various applications.
Challenges:
- Resource Intensity: The raw materials for CMCs often require significant energy and environmental resources for extraction.
- Production Emissions: Manufacturing CMCs can result in CO2 and other greenhouse gas emissions.
- Waste Disposal: The difficulty of recycling CMCs poses a disposal problem.
Solutions:
- Alternative Materials: Research into bio-based composites could reduce reliance on traditional raw materials.
- Green Manufacturing Processes: Adopting energy-efficient technologies may minimize emissions and resource consumption.
- Innovative Recycling Techniques: Advancements in recycling methods can enable the repurposing of CMCs after their useful life.
In summary, sustainability is not just a buzzword. It is an imperative for enhancing the role of CMCs in various industries. By focusing on lifecycle assessments and addressing sustainability challenges, industry stakeholders can ensure CMC materials contribute positively to environmental and economic landscapes.
Key Insight: The development of Composite Matrix Composites must balance technological advancement with resource management and sustainability efforts. This dual focus can lead to more responsible material usage and broader industry applications.
Challenges in Material Utilization
The utilization of Composite Matrix Composites (CMCs) presents a series of challenges that are pivotal to understanding their integration into various applications. These challenges can significantly affect the overall effectiveness, cost-efficiency, and feasibility of CMCs in real-world scenarios. Addressing these issues is essential for both researchers and industry professionals. It provides insight into not only the limitations inherent in existing technology but also the considerations for optimizing and advancing CMC performance across different sectors.
Limitations in Current Technology
One major limitation in the current technology of CMC materials is their manufacturing complexity. Producing CMCs often involves intricate processes that can be difficult to standardize. This complexity can lead to variations in quality, resulting in materials that do not consistently meet desired specifications. Furthermore, the high cost of some raw materials, combined with the energy-intensive processes required for CMC production, poses economic barriers to widespread adoption.
Additionally, the inherent properties of CMCs can also be a double-edged sword. While they possess excellent thermal stability and high strength-to-weight ratios, issues such as brittleness can limit their application in dynamic environments. For instance, CMCs may not perform reliably under certain impact conditions, which is critical in fields like aerospace or automotive where both performance and safety are paramount.
Addressing Performance Trade-offs
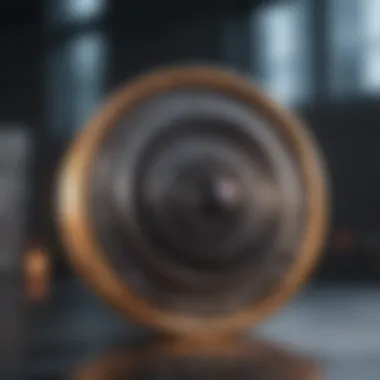
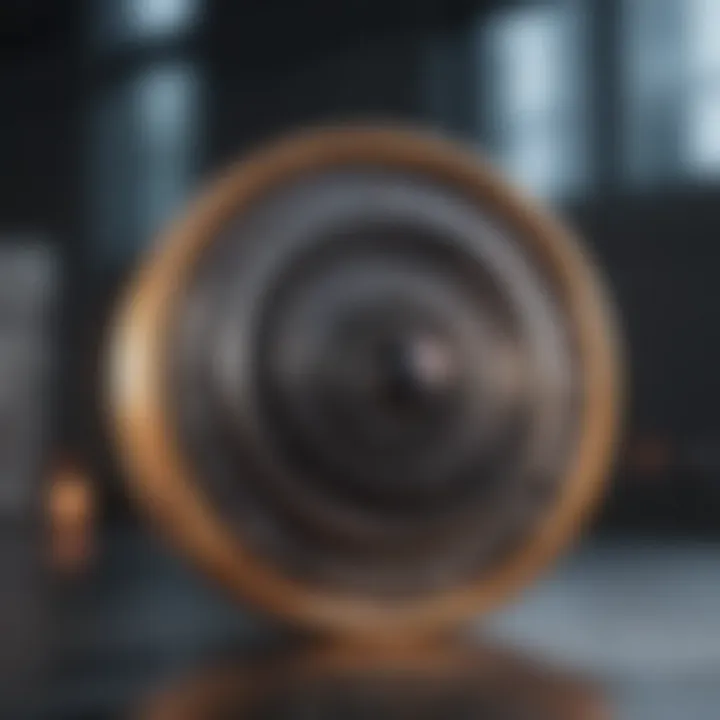
When utilizing CMC materials, manufacturers often face trade-offs between desirable properties. For example, enhancing thermal resistance might compromise mechanical integrity. To tackle these performance trade-offs, extensive research into material formulations and hybrid designs is necessary. By exploring novel compositions and innovative manufacturing techniques, researchers can develop CMCs that balance multiple performance metrics, thus broadening their applicability.
Moreover, collaboration between academia and industry can foster advancements in CMC technology. Developing partnerships can facilitate pilot programs where new materials are tested in real-world environments. This engagement can lead to the identification of practical solutions that might not emerge in strictly academic research settings.
"Understanding challenges is the first step toward innovation."
Navigating the challenges of CMC material utilization ultimately requires a combination of strategic research, technological innovation, and collaboration among various stakeholders. As industries increasingly turn toward advanced materials, addressing these challenges will be critical for the future growth and application of Composite Matrix Composites.
Recent Advancements in Research
The field of Composite Matrix Composites, or CMCs, has seen significant progress in recent years. These advancements are pivotal for the expansion and refinement of applications across various industries. Notably, research has focused on improving the material's performance, durability, and cost-effectiveness. The interrelation between innovative formulations and emerging application trends in CMCs underlies much of this progress. Each improvement directly contributes to enhancing the overall utility of these materials, making them suitable for more demanding environments.
Innovative Compositions and Formulations
Recent studies have explored alternative raw materials and novel formulations for CMCs. Researchers examine the incorporation of ceramic fibers combined with polymer matrices, leading to greater improvements in thermal stability and mechanical strength. The development of hybrid composites, which combine different types of fibers, has shown promising results. For instance, combining silicon carbide fibers with alumina matrices enhances toughness and resilience, crucial for high-temperature applications.
- Additives and fillers are being scrutinized for their roles in increasing CMC performance. Introducing nanomaterials such as carbon nanotubes can significantly enhance properties like electrical conductivity and thermal resistance.
The impact of these innovative formulations affects several industries. In aerospace, for example, the lightness yet strength of newer CMCs provides improved fuel efficiency for aircraft. In the automotive sector, these advancements allow manufacturers to design lighter components, influencing overall vehicle mileage.
Emerging Trends in Applications
The applications of CMC materials are also evolving. Emerging trends reveal a growing preference for CMCs in several critical industries.
- Aerospace: New CMC formulations allow for parts that can withstand extreme temperatures during flight, leading to better performance and safety.
- Medical Devices: The biocompatibility of certain CMCs lends the materials to innovative uses in implants and surgical tools.
- Energy Sector: CMCs are gaining traction in energy applications, particularly in the context of renewable energy solutions. Their thermal properties make them fit for use in turbines and solar panels.
More than just new uses, the adaptation of CMCs to meet specific industry needs is vital. This flexibility offers manufacturers the ability to customize materials for unique applications, ultimately fostering collaboration between researchers and industry players.
"The future of Composite Matrix Composites is intertwined with ongoing research efforts. These advancements are not just about improving existing technology, but also about fostering new possibilities for innovation across sectors."
Future Prospects for Materials
The future of composite matrix composites (CMC) is promising, intersecting the fields of materials science, engineering, and various industries. Understanding this topic helps to grasp how CMCs may shape technological advancements in the coming years. CMC materials are known for their remarkable properties, making them ideal candidates for innovative applications.
Market Trends and Industry Growth
The market for CMC materials is expected to witness significant expansion. Industries such as aerospace, automotive, and energy are rapidly integrating CMCs into their operations. This shift is primarily driven by the need for materials that deliver high performance while remaining lightweight. The aerospace sector, in particular, has shown a growing preference for CMCs due to their ability to withstand extreme temperatures and stress, leading to more fuel-efficient aircraft.
Some key trends driving market growth include:
- Increasing demand for lightweight materials in various applications.
- Ongoing research into enhanced CMC properties such as toughness and reliability.
- The need for sustainable materials, pushing industries toward composites with lower environmental impacts.
- Technological advancements in manufacturing processes that facilitate higher production rates and cost reduction.
With these trends, the CMC market is poised for robust growth, enhancing the overall performance of products across multiple domains.
Potential for New Applications
As CMC materials evolve, their potential applications are becoming broader and more innovative. Industries are beginning to explore uses that were previously not feasible. For instance, in the realm of medical applications, CMCs are being evaluated for potential use in surgical implants and instruments. Their biocompatibility and mechanical properties make them suitable for such uses.
Moreover, the energy sector is turning to CMCs for next-generation components in renewable energy systems. Wind turbine blades, for example, could benefit from CMCs to reduce weight and enhance durability.
Considerations for future applications include:
- Research into novel formulations that combine CMCs with other materials to enhance properties.
- Development of smart materials that can respond to environmental changes, thus broadening functional uses.
- Collaboration between industries and research institutions to foster innovation in CMC applications.
The adaptability and uniqueness of CMC materials make them prime candidates for next-generation applications across various fields, perpetuating a cycle of innovation and exploration.
As we move forward, it is clear that CMC materials will not only maintain their importance but will continue to grow as essential components. This growth will pave the way for breakthroughs in technology that benefit society at large.
The End and Summary of Key Insights
In summation, the exploration of Composite Matrix Composites (CMC) has unveiled critical insights into their structure, properties, and diverse applications. This article articulated the evolution of CMC materials, detailing their remarkable traits such as high strength-to-weight ratios and exceptional thermal resistances that make them indispensable across multiple sectors.
The discussions highlighted specific benefits of CMCs. For instance, their mechanical properties contribute significantly to the aerospace industry, where weight reduction and durability are essential. Similarly, in the automotive field, their use leads to enhanced performance and efficiency. Each application underlines the versatility of CMCs and their growing relevance in today’s technologically advanced landscape.
"Understanding the properties and applications of CMC materials is essential for advancing modern engineering and manufacturing processes."
Furthermore, the article examined environmental considerations, emphasizing the importance of lifecycle assessments of CMCs. As industries move towards sustainable solutions, recognizing the environmental impact of materials will be crucial. Solutions addressing these challenges will not only improve CMCs’ market viability but also align with global sustainability goals.
Recent advancements in CMC research were also covered, showcasing innovations in formulations and emerging trends that indicate a bright future for these materials. Anticipated market growth signals opportunities for new applications, making it vital for professionals and researchers to stay informed about trends in CMC technology.
In essence, the insights gathered provide a solid foundation for understanding the significance of CMC materials. This knowledge not only benefits those in academia but also practitioners and industry stakeholders who rely on advanced materials for innovation and growth. It is evident that CMCs will continue to shape the future of various industries, underscoring the importance of ongoing research and development in this field.